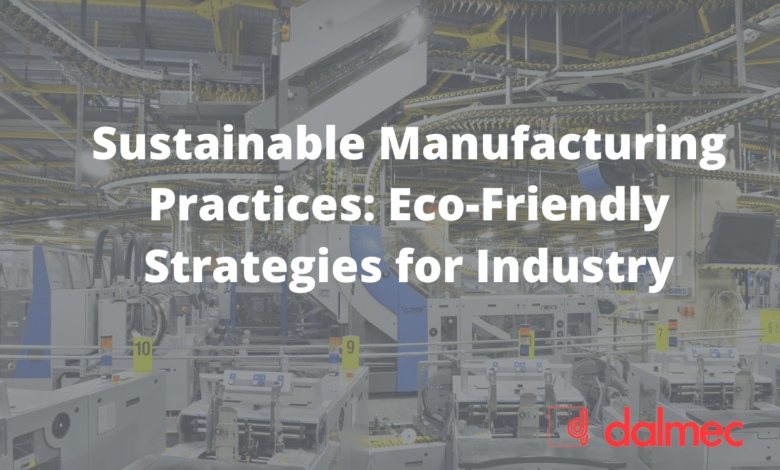
Business Practice & Sustainable Manufacturing Evolution
With business practice and the evolution of sustainable manufacturing at the forefront, this blog post delves into the fascinating journey of how manufacturing processes have transformed over time. From the early days of industrialization to the innovative approaches of today, we’ll explore the key shifts, trends, and challenges in achieving a more environmentally conscious approach to production. This includes examining the historical context, emerging technologies, and the vital role of supply chains in creating a truly sustainable future for manufacturing.
This journey will explore the critical role of environmental impact assessments, the adoption of circular economy principles, and the success stories of companies leading the charge in sustainable manufacturing. We’ll examine the technological advancements propelling this evolution and the ever-increasing importance of consumer demand and government regulations. Ultimately, the goal is to understand the path towards a future where manufacturing thrives alongside environmental responsibility.
Historical Context of Business Practices
The evolution of manufacturing is intrinsically linked to the evolution of business practices. From the rudimentary crafts of the past to the complex, globalized production of today, the methods and philosophies surrounding manufacturing have undergone dramatic transformations. These changes are deeply intertwined with the environment, highlighting a dynamic relationship between economic growth and ecological responsibility.
Early Manufacturing and Resource Utilization
Early manufacturing processes, often localized and handcrafted, relied heavily on readily available local resources. Waterpower, for instance, was a crucial energy source in many early industrial settings. However, these systems were often limited in scale and efficiency. The utilization of resources was largely dictated by local availability and demand, with minimal consideration for long-term impacts. Waste management was generally rudimentary, often involving simple disposal methods or repurposing of materials within the immediate community.
Sustainable manufacturing is rapidly evolving, and businesses are increasingly recognizing the importance of eco-friendly practices. This shift is driven by a need for ethical production and resource conservation, and the future of sustainable energy looks to alternative materials, like bio-plastics and recycled metals, to power these processes the future of sustainable energy looks to alternative materials. Ultimately, embracing these changes will be crucial for long-term business success and a healthier planet.
The Rise of Industrialization and Environmental Impact
The Industrial Revolution brought about significant shifts in production methods. The advent of machinery, powered by fossil fuels, enabled mass production and drastically increased output. This period saw a dramatic expansion in manufacturing capacity, but it also marked a growing environmental footprint. The increased consumption of fossil fuels and the generation of industrial waste became significant concerns, although environmental regulations were largely absent or minimal in their scope.
Shifting Business Practices Towards Sustainability
The growing awareness of environmental problems spurred the development of sustainable manufacturing practices. This shift was not immediate, but rather a gradual process driven by public pressure, technological advancements, and evolving business strategies. Early examples of environmental concern emerged, but it took time for businesses to integrate sustainability into core operations. Companies started to recognize the long-term financial benefits of resource efficiency and waste reduction.
A Timeline of Sustainable Manufacturing Milestones
- 1700s-1800s: Emergence of early factories and steam power, showcasing the start of large-scale production but with minimal environmental safeguards. Early examples of localized pollution are documented.
- Early 1900s: Increasing industrial output and the start of environmental awareness movements, although industrial practices remained largely unregulated.
- 1970s-1980s: Growing public concern over pollution, leading to the first significant environmental regulations and the beginnings of pollution control technologies. Notable environmental disasters spurred public outcry and governmental action.
- 1990s-2000s: Emergence of “green” manufacturing principles and ISO 14000 standards, signifying a formal approach to sustainability. The rise of environmental management systems demonstrated a growing awareness of corporate responsibility.
- 2010s-Present: Emphasis on circular economy models, renewable energy integration, and sustainable materials. The increasing adoption of sustainable practices demonstrates a broader commitment to long-term environmental responsibility.
Contrasting Environmental Footprints of Manufacturing Eras
Time Period | Dominant Production Methods | Waste Generation | Resource Consumption | Environmental Impact |
---|---|---|---|---|
Pre-Industrial Revolution | Handcrafted, localized | Low, often reused/recycled locally | Limited, dependent on local resources | Minimal, localized environmental impact |
Industrial Revolution (1700s-1800s) | Steam power, mass production | Increased, often disposed of unsustainably | High, increased reliance on fossil fuels | Significant pollution, localized ecological damage |
Mid-20th Century | Fossil fuel-powered machinery, chemical-intensive processes | High, increased chemical waste | Very high, increased demand for resources | Widespread pollution, degradation of ecosystems |
Late 20th Century – Present | Automation, lean manufacturing, renewable energy integration | Decreased (with efforts), emphasis on waste reduction | Decreased (with efforts), focus on resource efficiency | Mitigation of pollution, emphasis on sustainable practices |
Emerging Trends in Sustainable Manufacturing
Sustainable manufacturing is no longer a niche concept but a crucial element for businesses seeking long-term viability and positive societal impact. The evolution of consumer consciousness and stringent environmental regulations are driving a rapid shift towards environmentally friendly production processes. This transformation requires innovative approaches and a willingness to adapt to new technologies and market demands.The future of manufacturing is intertwined with sustainability.
Businesses are actively seeking ways to minimize their environmental footprint while maintaining profitability and competitiveness. This involves a multifaceted approach encompassing technological advancements, consumer engagement, and government regulations. The adoption of sustainable practices is not just a moral imperative but also a strategic opportunity for companies to enhance their brand image, attract environmentally conscious consumers, and gain a competitive edge in the market.
Current Trends Shaping Sustainable Manufacturing
Several key trends are shaping the future of sustainable manufacturing. These include a growing emphasis on circular economy principles, the adoption of renewable energy sources, and the integration of advanced technologies for waste reduction and resource optimization. These shifts are driven by both consumer preferences and legislative pressures.
Role of Technology in Sustainable Practices
Technology plays a pivotal role in driving sustainable manufacturing. Digital tools and automation enable real-time monitoring of resource consumption, predictive maintenance to minimize downtime, and optimization of production processes for reduced waste. The integration of advanced materials science and biotechnology further enhances sustainability by enabling the development of more efficient and environmentally friendly products and processes.
Influence of Consumer Demand and Government Regulations
Consumer demand for sustainable products and services is escalating, influencing companies to incorporate eco-friendly practices. This demand is reinforced by stringent government regulations and policies aimed at reducing pollution and promoting resource efficiency. Businesses are responding to these pressures by investing in research and development of sustainable solutions.
Examples of Innovative Sustainable Manufacturing Techniques
Several innovative techniques are emerging to address sustainability challenges. One example is the use of 3D printing for customized production, enabling reduced material waste and on-demand manufacturing. Another example involves using bio-based materials in product development, substituting conventional materials with renewable resources. Companies are increasingly exploring closed-loop systems to recover and reuse materials, reducing waste and resource depletion.
Key Technological Advancements Supporting Sustainable Manufacturing
Technology | Application | Environmental Benefits | Limitations |
---|---|---|---|
Additive Manufacturing (3D Printing) | Creation of complex parts with minimal material waste, on-demand production, localized manufacturing. | Reduced material usage, potential for localized production minimizing transportation emissions, customized products. | High initial investment costs, limited material choices, potential for material waste in support structures. |
Renewable Energy Integration | Powering manufacturing facilities with solar, wind, or hydro power. | Reduced reliance on fossil fuels, lower carbon emissions, improved energy security. | Dependence on weather conditions, intermittency of renewable sources, infrastructure costs. |
Closed-Loop Systems | Recovery and reuse of materials, waste reduction, resource optimization. | Minimized waste, enhanced resource efficiency, reduced reliance on virgin materials. | Complexity in implementation, potential for material quality degradation in recycling processes, higher initial setup costs. |
Advanced Materials Science | Development of lightweight, high-performance, and biodegradable materials. | Reduced material consumption, enhanced product performance, minimal environmental impact. | High research and development costs, limited availability of specific materials, potential for material incompatibility. |
Sustainable Business Practices & Supply Chains
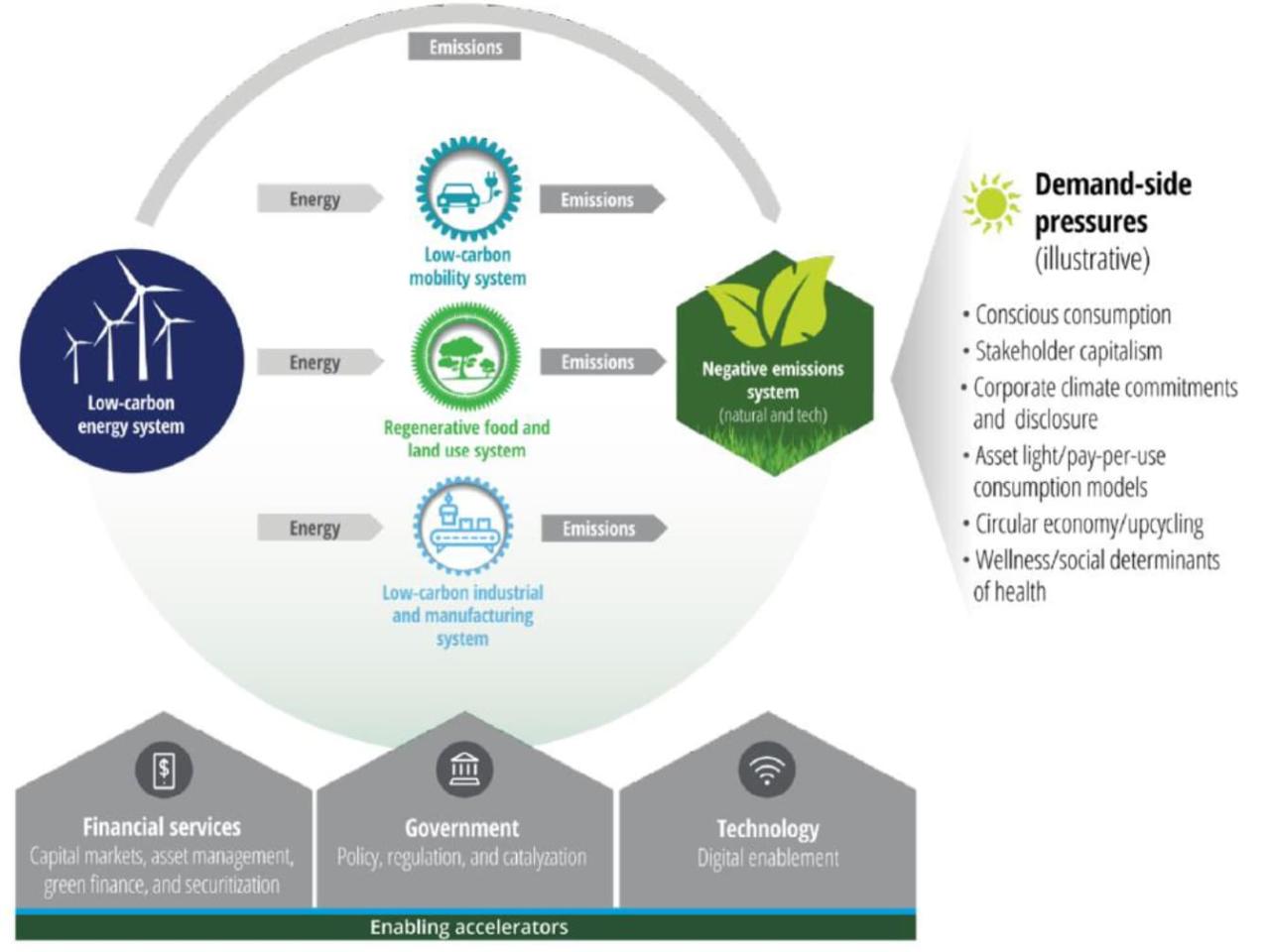
Integrating sustainability into core business strategies is no longer a fringe concept but a crucial component for long-term success. Companies are increasingly recognizing the interconnectedness of environmental, social, and economic factors in their operations, driving a shift towards sustainable practices throughout their value chains. This realization isn’t just about ethical responsibility; it’s also about identifying and capitalizing on new market opportunities and mitigating risks associated with resource depletion and environmental damage.The evolution of business practices now necessitates a profound understanding of how sustainability impacts every stage of production, from raw material sourcing to final product disposal.
A critical aspect of this shift involves the creation of sustainable supply chains, which are not just about ethical sourcing but about building resilience and minimizing environmental footprints across the entire network. The imperative to embrace sustainability is not only a moral imperative, but also a smart business strategy.
Integration of Sustainability into Core Business Strategies
Businesses are embedding sustainability into their core strategies in various ways. This often involves establishing specific sustainability goals, targets, and metrics for performance evaluation. Companies are increasingly aligning their strategic objectives with environmental, social, and governance (ESG) principles. This integration manifests in the development of eco-friendly products, the adoption of circular economy models, and the implementation of renewable energy sources within their operations.
Furthermore, companies are actively engaging with stakeholders, including suppliers, customers, and communities, to foster transparency and accountability.
Modern business practices are increasingly recognizing the need for sustainable manufacturing. This evolution isn’t just about eco-friendliness, but also about long-term profitability. A great example of this shift is seen in initiatives like sustaining our waters the fox wolf watershed alliance , which highlights the importance of clean water for healthy ecosystems and, ultimately, for a thriving business environment.
Ultimately, prioritizing sustainable manufacturing practices benefits both the planet and the bottom line.
Importance of Sustainable Supply Chains
Sustainable supply chains are pivotal in achieving environmental goals. They encompass the entire network of suppliers, manufacturers, distributors, and retailers involved in bringing a product to market. By integrating sustainability principles into each link of the supply chain, companies can significantly reduce their environmental impact. This includes optimizing logistics to minimize transportation emissions, implementing responsible sourcing practices to avoid deforestation or exploitation, and adopting circular economy principles to minimize waste and maximize resource utilization.
Challenges of Implementing Sustainable Practices Across Diverse Supply Chains
Implementing sustainable practices across diverse supply chains presents significant challenges. Different regions, cultures, and economies have varying levels of environmental regulations, labor standards, and access to sustainable resources. Furthermore, the complexity of global supply chains can make it difficult to monitor and manage sustainability throughout the entire network. A lack of transparency in the supply chain, combined with inconsistent standards and practices, poses a significant obstacle to implementing comprehensive sustainable solutions.
Examples of Companies Successfully Implementing Sustainable Supply Chain Management
Several companies have successfully implemented sustainable supply chain management. For example, Patagonia, known for its commitment to environmental protection, has established strict ethical and environmental standards for its suppliers. Similarly, Unilever has implemented sustainable sourcing initiatives across its vast product portfolio, focusing on reducing water usage and deforestation. These examples demonstrate that integrating sustainability into supply chains is achievable and can drive positive change.
Contrasting Approaches to Sustainable Sourcing
Industry | Sourcing Methods | Environmental Impact Assessment | Transparency |
---|---|---|---|
Apparel | Fair Trade certifications, recycled materials, ethical labor practices | Life cycle assessments, water footprint analysis, material sourcing audits | Supplier audits, public reporting, traceability |
Electronics | Conflict-free minerals, recycled components, sustainable packaging | Energy efficiency assessments, material composition analysis, electronic waste management plans | Supply chain mapping, disclosure of materials, third-party certifications |
Food & Beverage | Local sourcing, organic farming, sustainable fishing practices | Carbon footprint analysis, water usage assessment, biodiversity impact studies | Farmer certifications, traceability systems, transparent labeling |
Environmental Impact Assessment & Measurement
Understanding the environmental footprint of manufacturing processes is crucial for driving sustainable practices. Accurate assessments allow companies to identify areas for improvement, track progress, and ultimately minimize their impact on the planet. This crucial step empowers businesses to make informed decisions, adopt innovative technologies, and contribute to a healthier environment.
Methods for Assessing Environmental Impact
A variety of methodologies exist for evaluating the environmental impact of manufacturing processes. These methods typically involve detailed analysis of energy consumption, waste generation, and emissions. A holistic approach considers the entire lifecycle of the product, from raw material extraction to disposal. By adopting a systematic approach, manufacturers can identify areas of significant environmental impact and prioritize actions for improvement.
Measuring and Tracking Sustainability Progress
Tracking progress towards sustainability goals necessitates consistent and accurate data collection. Establish key performance indicators (KPIs) reflecting specific environmental targets, such as reduced water usage, waste diversion, or greenhouse gas emissions. Regular monitoring and reporting are vital for demonstrating accountability and driving continuous improvement. A clear understanding of the metrics used for each aspect of the process ensures that progress can be measured and improvements are effectively tracked.
Importance of Accurate Data Collection and Analysis
Accurate data collection and analysis are paramount in sustainable manufacturing. Inaccurate data can lead to misleading conclusions and ineffective strategies. Robust data management systems and standardized methodologies ensure consistency and reliability. Implementing advanced data analytics tools can uncover patterns and trends, facilitating proactive decision-making and enabling a deeper understanding of the environmental impact of various processes.
Examples of Environmental Performance Metrics
Various metrics are employed to assess environmental performance in manufacturing. Examples include water usage per unit of production, energy consumption per unit of output, and waste generation per unit of product. Specific indicators like carbon footprint, water footprint, and material efficiency can provide comprehensive insights into the environmental performance of a manufacturing process.
Environmental Impact Assessment Methodologies
Method | Data Required | Benefits | Limitations |
---|---|---|---|
Life Cycle Assessment (LCA) | Detailed information on all stages of the product lifecycle (material sourcing, manufacturing, use, and disposal). | Provides a comprehensive understanding of the environmental impact throughout the product’s entire lifecycle, identifying hotspots for improvement. | Can be complex and time-consuming to conduct. Data availability and accuracy can be challenging. |
Material Flow Analysis (MFA) | Data on material inputs, outputs, and transformations within a manufacturing system. | Identifies material flows and potential waste streams, enabling efficient resource management. | May not capture all environmental impacts, such as those related to energy consumption. Requires extensive data collection. |
Environmental Footprint Assessment | Information on energy use, water consumption, waste generation, and emissions. | Offers a standardized approach for evaluating environmental performance. Facilitates comparison with industry benchmarks. | May not capture all relevant environmental impacts depending on the specific footprint type. Implementation of specific standards may be necessary. |
Circular Economy Principles & Manufacturing
The linear “take-make-dispose” model of manufacturing is increasingly unsustainable. Resource depletion and environmental pollution are significant concerns. A circular economy offers a transformative alternative, prioritizing resource efficiency and minimizing waste. This approach focuses on designing products for durability, repairability, and recyclability, keeping materials in use for as long as possible.A circular economy fundamentally shifts the focus from a “make-and-dispose” approach to a model of reuse, repair, and recycling.
This approach aims to close material loops, reducing waste and maximizing the value derived from materials. By adopting this approach, businesses can create long-term value, enhance profitability, and contribute to a more sustainable future.
Circular Economy Principles in Manufacturing
The circular economy rests on three core principles: reuse, repair, and recycling. These principles are essential in transforming manufacturing processes and fostering a sustainable future. By embracing these principles, businesses can minimize waste, conserve resources, and create a more sustainable manufacturing ecosystem.
Reuse
Reuse involves extending the lifespan of products through various methods like remanufacturing, refurbishing, and re-purposing. This reduces the need for virgin materials and lowers the overall environmental footprint. In manufacturing, reuse can manifest in various ways, including the reuse of components in new products or the repurposing of existing products into new forms. A successful example of reuse is the remanufacturing of engines or other components.
Repair
Repairing products instead of replacing them extends their lifespan and reduces waste. In manufacturing, this means designing products for easy repair, using readily available parts, and fostering a culture of repair within the supply chain. Companies can incentivize repairs by offering repair services or promoting the use of repair manuals.
Recycling
Recycling involves converting waste materials into new products. In manufacturing, this requires designing products with recyclability in mind. This involves using recyclable materials, incorporating clear labeling for material types, and establishing effective recycling processes. For example, many companies are now using recycled plastic in their products.
Benefits of a Circular Economy Approach
Implementing a circular economy approach yields numerous benefits for businesses. These benefits include reduced material costs, enhanced brand reputation, increased profitability, and a significant reduction in environmental impact. The transition can lead to substantial cost savings, as businesses can minimize waste and conserve resources. Furthermore, a circular economy fosters innovation and new business opportunities.
Challenges of Implementing Circular Economy Principles
Implementing circular economy principles presents certain challenges. These include the need for new technologies, changes in manufacturing processes, and the establishment of effective recycling systems. There may be initial investment costs associated with the transition, but long-term benefits often outweigh these costs.
Successful Companies Incorporating Circular Economy Principles
Numerous companies are successfully incorporating circular economy principles into their manufacturing processes. Companies like Interface, Patagonia, and IKEA are leading examples, demonstrating how these principles can be implemented in a wide variety of industries. Interface, for example, has implemented a system for the collection and recycling of carpet tiles.
Transitioning to a Circular Economy Model
Stage | Actions | Resources Needed | Expected Outcomes |
---|---|---|---|
Assessment | Analyze current processes, identify waste points, and assess material flows. | Data analysis tools, expert consultants | Understanding current footprint, potential areas for improvement. |
Design | Design products for durability, repairability, and recyclability. | Engineering expertise, design software | Sustainable product designs, minimized waste |
Implementation | Integrate circular economy principles into operations, develop partnerships, and establish recycling processes. | Investment in new equipment, training, and supply chain collaboration. | Reduced material consumption, waste generation. |
Monitoring and Evaluation | Track performance metrics, assess the effectiveness of implemented changes, and adjust strategies as needed. | Data tracking systems, performance analysis tools | Continuous improvement, optimized resource utilization |
Case Studies of Sustainable Manufacturing Success
Sustainable manufacturing isn’t just a trend; it’s a necessity for businesses seeking long-term viability. This evolution demands more than just lip service; it necessitates a fundamental shift in how companies approach production. Successful case studies reveal the tangible benefits and practical strategies that drive this transition.
Examples of Sustainable Manufacturing Leaders
Numerous companies have successfully integrated sustainable practices into their operations, demonstrating the feasibility and rewards of such initiatives. These examples showcase not only the strategies employed but also the quantifiable results and valuable lessons learned.
Thinking about business practices and how sustainable manufacturing is evolving is crucial. It’s exciting to see how organizations are adapting. For example, the recent redesignation of the Stevens Points Breast Care Center, a testament to quality healthcare, aligns with the broader shift towards more sustainable business practices in the medical field. This commitment to sustainability in healthcare operations inspires similar innovative approaches across various industries, demonstrating how crucial ethical business practices are to the evolution of sustainable manufacturing.
Stevens Points Breast Care Center receives redesignation highlights this. This shift in focus really pushes the boundaries of what’s possible in terms of environmentally friendly and responsible business practices in all fields.
Patagonia: Embracing Recycled Materials
Patagonia, a renowned outdoor apparel company, exemplifies a commitment to sustainable materials. They have a strong track record of using recycled polyester and organic cotton in their products. This strategy has reduced their reliance on virgin resources, significantly lowering their environmental footprint. The measurable results include a substantial decrease in greenhouse gas emissions associated with textile production.
Patagonia’s approach emphasizes transparency and consumer education, fostering trust and encouraging further adoption of sustainable practices. A key lesson learned is that sustainability is not just about environmental impact but also about building brand loyalty through ethical and transparent practices.
Interface: A Circular Economy Model
Interface, a leading manufacturer of commercial flooring, has pioneered a circular economy model for their operations. Their strategy revolves around minimizing waste, maximizing material reuse, and designing products for disassembly and recyclability. Interface has implemented innovative waste reduction programs and has shown impressive reductions in landfill waste. The company’s approach extends beyond product design, encompassing the entire supply chain, fostering collaboration with suppliers and customers to ensure the longevity of materials.
The results are not only environmentally positive but also economically beneficial, demonstrating the potential for profitability in sustainable practices. Interface’s case study highlights the importance of systemic change and a holistic approach to sustainability.
Tesla: Optimizing Battery Production
Tesla’s focus on battery production illustrates a different facet of sustainable manufacturing. Their strategy involves optimizing the entire battery production process, including raw material sourcing and end-of-life management. This meticulous approach aims to maximize efficiency and minimize waste. Tesla’s efforts have resulted in reduced energy consumption during production and increased battery life. The lessons learned from Tesla emphasize the importance of technological innovation in driving sustainable manufacturing practices.
Furthermore, the approach underscores the potential for disruption within traditional manufacturing models by implementing new technologies and standards.
Table: Key Success Factors in Sustainable Manufacturing, Business practice and the evolution of sustainable manufacturing
Company | Strategy | Impact | Key Learnings |
---|---|---|---|
Patagonia | Recycled materials, organic cotton | Reduced greenhouse gas emissions, enhanced brand loyalty | Sustainability fosters brand loyalty, transparency is key |
Interface | Circular economy model, material reuse | Reduced landfill waste, economic benefits | Systemic change and holistic approach drive sustainability |
Tesla | Optimized battery production | Reduced energy consumption, increased battery life | Technological innovation drives sustainable manufacturing |
Future of Sustainable Manufacturing
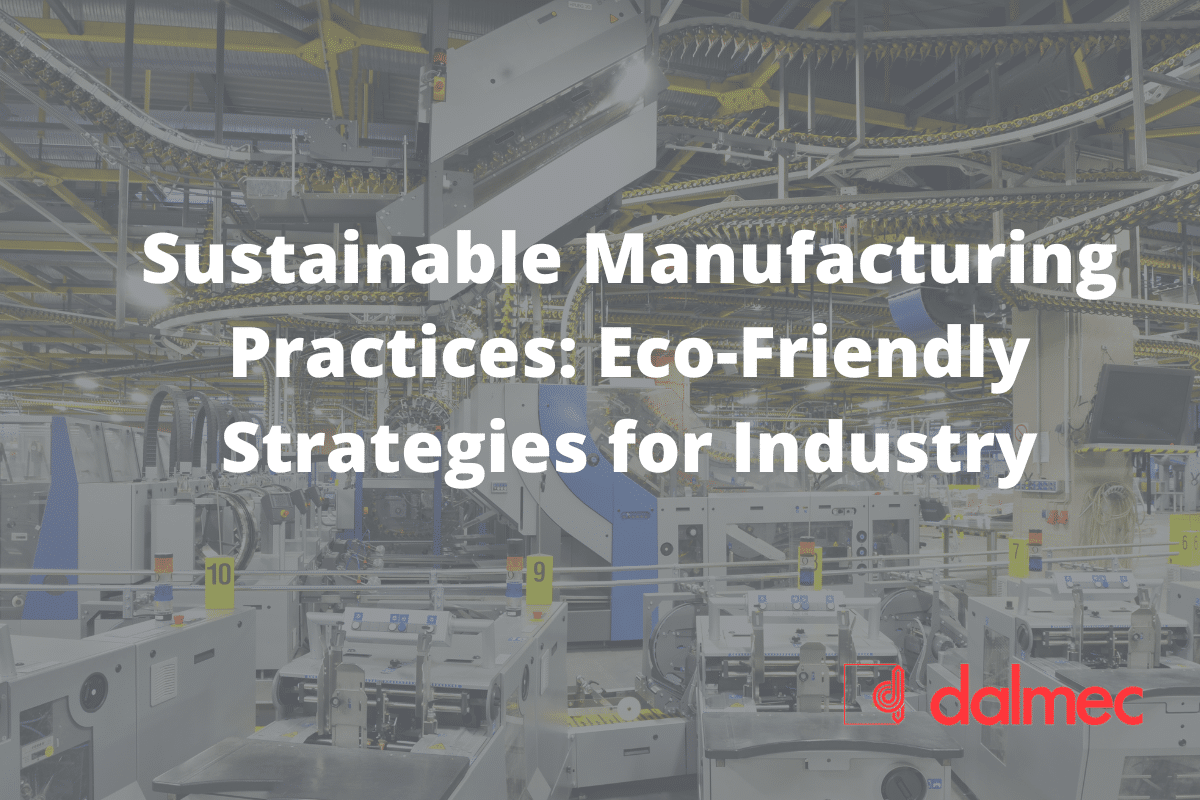
The future of manufacturing hinges on embracing sustainability, moving beyond incremental improvements to transformative change. This requires a fundamental shift in how we design, produce, and consume goods, prioritizing environmental responsibility and social equity. The journey towards sustainable manufacturing is not merely a trend but a necessity for a healthier planet and a more prosperous future.The next decade will witness a dramatic acceleration in the adoption of sustainable practices, driven by both consumer demand and regulatory pressures.
Companies that proactively integrate sustainability into their core strategies will gain a competitive advantage, while those that lag behind risk falling behind. This evolution is not solely about reducing environmental impact; it’s also about enhancing operational efficiency, fostering innovation, and building stronger, more resilient supply chains.
Emerging Technologies and Trends
Technological advancements are poised to revolutionize sustainable manufacturing. Additive manufacturing (3D printing), for instance, offers the potential to reduce material waste and create customized, on-demand products. Similarly, the integration of artificial intelligence (AI) and machine learning (ML) can optimize energy consumption, predict equipment failures, and minimize downtime. Furthermore, the rise of the Internet of Things (IoT) enables real-time monitoring and control of manufacturing processes, facilitating greater efficiency and sustainability.
Potential Challenges in the Next Decade
Despite the numerous opportunities, several challenges remain. Transitioning to sustainable practices often necessitates significant upfront investments in new technologies and processes. Ensuring the availability of sustainable materials and the ethical sourcing of components are also crucial concerns. Finally, the need for skilled labor capable of operating and maintaining these new technologies presents a significant workforce development challenge.
These hurdles must be addressed through strategic planning and collaborative efforts between businesses, researchers, and governments.
Opportunities in the Next Decade
Sustainable manufacturing presents considerable opportunities for innovation and growth. Companies that successfully integrate sustainability into their operations can enhance their brand reputation, attract environmentally conscious consumers, and gain access to new markets. Moreover, the development of sustainable products and processes often leads to cost savings through reduced waste, optimized resource use, and enhanced efficiency. By proactively embracing sustainability, businesses can build a more resilient future for themselves and the planet.
Role of Government Policies and Incentives
Government policies play a critical role in shaping the future of sustainable manufacturing. Incentives, such as tax breaks for investments in green technologies and regulations promoting the use of recycled materials, can significantly accelerate the adoption of sustainable practices. Furthermore, clear and consistent regulations regarding environmental standards can create a level playing field for all businesses. Government policies can provide the framework for the transition and ensure that the shift toward sustainability is fair and equitable.
Importance of Collaboration
Collaboration between businesses, researchers, and policymakers is paramount to driving sustainable manufacturing forward. Sharing knowledge, best practices, and research findings among stakeholders can foster innovation and accelerate the development of sustainable solutions. Joint ventures and partnerships can leverage the strengths of different organizations, leading to more impactful results than any single entity could achieve alone.
Potential Future Trends and Their Impacts
- Circular Economy Integration: Companies will increasingly adopt circular economy principles, designing products for recyclability, reuse, and repairability. This will lead to a significant reduction in waste and a more efficient use of resources.
- Bio-based Materials: The use of bio-based materials, such as plant-derived plastics and biofuels, will become more prevalent. This transition will reduce reliance on fossil fuels and promote biodiversity.
- Personalized Manufacturing: Advanced technologies will enable more personalized production, enabling the creation of customized products with minimal waste and optimized material usage. This trend will drive demand for flexible and adaptable manufacturing processes.
- Sustainable Supply Chains: Supply chains will become more transparent and sustainable, with businesses scrutinizing the environmental and social impacts of their suppliers. Traceability and ethical sourcing will be crucial components of a resilient and responsible supply chain.
- Digital Twins in Manufacturing: Digital twins will enable more precise simulations of manufacturing processes, facilitating optimization of resource usage and the reduction of environmental impact. This approach will improve operational efficiency and lead to cost savings.
Closing Summary: Business Practice And The Evolution Of Sustainable Manufacturing
In conclusion, the evolution of business practice and sustainable manufacturing represents a significant shift in how we approach production. From historical context to emerging trends, the integration of sustainability into core business strategies is no longer a choice, but a necessity. This transformation requires collaboration between businesses, researchers, and policymakers, and embracing innovative technologies and circular economy principles.
The future of manufacturing hinges on our collective ability to create a truly sustainable and responsible system. This journey is not without its challenges, but the potential rewards are immense.