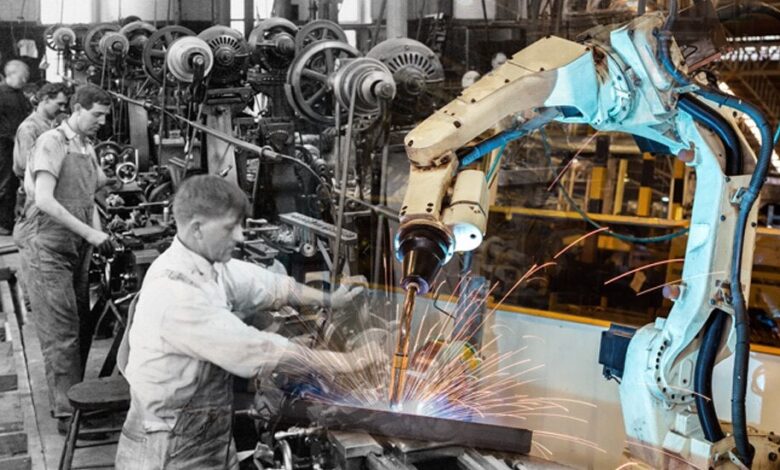
Opportunities Abound in Modern Manufacturing
Opportunities abound in modern manufacturing, offering exciting possibilities for growth and innovation across various sectors. From automation and digitalization to data analytics and AI, the landscape of manufacturing is rapidly evolving, creating new avenues for efficiency, productivity, and profitability. This blog post dives deep into the current trends, challenges, and future of modern manufacturing, exploring the potential returns and hurdles for companies looking to adapt.
The current manufacturing landscape is a dynamic blend of traditional methods and cutting-edge technologies. This exploration examines how these trends are transforming industries like automotive, aerospace, and electronics, highlighting the specific opportunities and challenges unique to each sector. We’ll also explore the importance of workforce development, government support, and ethical considerations in navigating this transition successfully.
Modern Manufacturing Trends
Modern manufacturing is undergoing a profound transformation, driven by technological advancements and a growing need for efficiency and sustainability. These shifts are reshaping the landscape of production, impacting everything from factory floors to supply chains. The integration of automation, digitalization, and data analytics is revolutionizing how products are designed, manufactured, and delivered to consumers.The current trends in modern manufacturing are characterized by a relentless pursuit of optimizing processes and maximizing output while minimizing environmental impact.
Modern manufacturing is booming, with tons of opportunities for growth. Take a look at Oshkosh, for example, where they’re eyeing new development near the Fox River, oshkosh eyes new development near fox river. This expansion hints at the exciting potential for innovation and job creation in the area, and that’s just one example of the many opportunities that abound in this dynamic sector.
This pursuit encompasses a spectrum of activities, from streamlining production lines to leveraging cutting-edge technologies. The result is a more agile, responsive, and data-driven manufacturing sector, better equipped to meet the demands of a rapidly evolving global market.
Automation in Modern Manufacturing
Automation is a cornerstone of modern manufacturing. From robotic arms performing intricate tasks on assembly lines to sophisticated machine vision systems inspecting parts, automation is increasing the speed and precision of production. This leads to reduced errors, increased output, and enhanced worker safety. For instance, in automotive manufacturing, robotic welding and painting are commonplace, leading to higher quality and faster production cycles.
Modern manufacturing is buzzing with innovative possibilities, from 3D printing to sustainable materials. But these advancements aren’t just about efficiency; they also open doors to environmental responsibility, like initiatives from organizations like sustaining our waters the fox wolf watershed alliance. By prioritizing sustainable practices, companies can reduce their environmental footprint while simultaneously boosting their bottom line, proving that opportunities abound in a forward-thinking manufacturing sector.
Further, automation is enabling manufacturers to operate 24/7, optimizing production capacity and lowering labor costs.
Digitalization and Data Analytics in Manufacturing
Digitalization and data analytics are transforming the way manufacturing companies operate. Real-time data from connected machines allows for proactive maintenance, predicting equipment failures before they occur. Data analytics also help optimize inventory management, improve supply chain visibility, and enable better forecasting of demand. The insights gleaned from this data can significantly improve efficiency and reduce waste. For example, predictive maintenance systems can identify potential issues in equipment well before they cause breakdowns, reducing downtime and saving significant costs.
Impact on Productivity, Efficiency, and Quality Control
These trends have a direct and substantial impact on manufacturing. Automation significantly boosts productivity by increasing output and reducing labor costs. Digitalization, through the use of data analytics, improves efficiency by enabling real-time adjustments to production processes. Finally, improved quality control measures, aided by automation and data analytics, minimize defects and ensure higher product quality.
Modern manufacturing is booming, with tons of opportunities for innovation. The need for sustainable energy solutions is driving a huge shift towards alternative materials, like those explored in the future of sustainable energy looks to alternative materials. This creates exciting new avenues for manufacturing companies, from developing new production processes to creating entirely new product lines.
So, while the future is uncertain, one thing is for sure: opportunities abound in modern manufacturing.
Innovative Manufacturing Processes and Technologies
Modern manufacturing is witnessing the emergence of innovative processes and technologies. 3D printing, for example, allows for the creation of complex geometries and customized parts, opening up new possibilities for design and production. Additive manufacturing is also enabling the production of intricate components with reduced material use, a step towards sustainability. Furthermore, Industry 4.0 principles are integrating various systems, creating smart factories that optimize production based on real-time data and feedback.
Comparison of Traditional and Modern Manufacturing Methods
Method | Automation | Data Usage | Efficiency |
---|---|---|---|
Traditional Manufacturing | Low | Limited | Moderate |
Modern Manufacturing | High | Extensive | High |
Opportunities in Specific Manufacturing Sectors
Modern manufacturing is undergoing a rapid transformation, driven by technological advancements and evolving consumer demands. This shift presents significant opportunities for growth and innovation across various sectors. This exploration delves into the specific advantages and challenges in key areas like automotive, aerospace, and electronics, highlighting the application of modern trends and the potential of AI and machine learning.
Opportunities in the Automotive Industry
The automotive industry is experiencing a paradigm shift from traditional manufacturing to a more integrated and data-driven approach. Modern manufacturing trends, including Industry 4.0 principles and automation, are crucial in improving efficiency, reducing costs, and enhancing product quality. The rise of electric vehicles (EVs) and autonomous driving systems further underscores the need for advanced manufacturing techniques.
- Enhanced Production Efficiency: Implementing lean manufacturing principles and automation, such as robotic arms and automated guided vehicles (AGVs), can significantly boost production efficiency, reducing lead times and minimizing waste. Examples include Tesla’s use of automated assembly lines and Toyota’s Kanban system.
- Improved Product Quality: Advanced sensors and data analytics allow for real-time monitoring of production processes, enabling proactive identification and correction of defects. This translates to higher product quality and reduced warranty costs.
- Cost Reduction: By streamlining processes and optimizing resource utilization, manufacturers can reduce material waste, labor costs, and energy consumption. This is crucial in the competitive automotive market.
- Increased Customization: AI and machine learning can personalize vehicle designs and features based on customer preferences. This caters to a growing demand for tailored products.
Opportunities in the Aerospace Industry
The aerospace industry demands high precision, reliability, and safety in manufacturing. Modern manufacturing trends like additive manufacturing (3D printing) and digital twin technologies can revolutionize production methods and reduce costs.
- Reduced Manufacturing Time: 3D printing enables rapid prototyping and customized part production, shortening development cycles and allowing for faster iteration on designs.
- Improved Component Quality: Advanced inspection technologies and AI-powered quality control systems enhance the accuracy and reliability of manufactured components.
- Cost Reduction: Optimized material usage and streamlined production processes lead to lower manufacturing costs, a critical factor in a highly competitive market.
- Enhanced Design and Development: Digital twins provide virtual representations of aircraft, allowing for detailed simulations and testing of designs, leading to improved performance and reduced development costs.
Opportunities in the Electronics Industry
The electronics industry relies heavily on precision and speed in manufacturing. Modern manufacturing trends like automation and advanced materials are key to staying competitive.
- Increased Production Speed: Automated assembly lines and advanced robotics allow for higher production volumes and faster turnaround times, crucial in the fast-paced electronics market.
- Improved Product Reliability: AI-powered predictive maintenance systems can identify potential equipment failures before they occur, leading to improved reliability and reduced downtime.
- Miniaturization and Innovation: Advanced materials and manufacturing techniques enable the development of increasingly smaller and more complex electronic devices, driving innovation.
- Customization and Personalization: AI and machine learning can enable the customization of electronic products based on individual user needs, fostering innovation.
Comparison and Contrast of Sector Challenges and Opportunities
While all sectors benefit from modern manufacturing trends, they face distinct challenges. The automotive industry struggles with the complexity of integrating new technologies, while the aerospace industry faces regulatory hurdles. The electronics sector faces competition from emerging markets and the need for continuous innovation.
Sector | Trend | ROI | Challenges |
---|---|---|---|
Automotive | Autonomous driving systems | High (potentially transformative) | Integration complexity, regulatory hurdles |
Aerospace | Additive manufacturing | Medium to High (cost savings in long term) | Regulatory compliance, material science |
Electronics | AI-powered quality control | High (improved quality, reduced defects) | Competition from emerging markets, rapid technological advancements |
Challenges and Mitigation Strategies
Embarking on a journey toward modern manufacturing necessitates careful consideration of the hurdles that often accompany innovation. While the opportunities are vast, challenges related to workforce adaptation, infrastructure investment, and initial capital outlay require proactive mitigation strategies. These challenges are not insurmountable, and successful adoption hinges on a comprehensive approach that leverages existing resources and fosters collaborative partnerships.Addressing these challenges is crucial for realizing the full potential of modern manufacturing practices.
A holistic strategy that combines workforce development, financial incentives, and strategic infrastructure planning is essential to navigate the transition smoothly. This approach not only mitigates the challenges but also maximizes the benefits of modern manufacturing technologies.
Workforce Retraining and Skill Gaps, Opportunities abound in modern manufacturing
Successfully implementing modern manufacturing practices requires a workforce equipped with the necessary skills. Traditional manufacturing skills often do not directly translate to the demands of advanced technologies like robotics, automation, and data analytics. Addressing this skill gap demands comprehensive retraining programs tailored to specific industry needs. These programs should cover not only technical skills but also soft skills like problem-solving, teamwork, and adaptability.
Infrastructure Upgrades
Modern manufacturing often requires significant infrastructure upgrades, including new machinery, improved facilities, and enhanced connectivity. The upfront investment can be substantial, posing a barrier for smaller or medium-sized enterprises. Government incentives and financial support can play a critical role in making these upgrades more accessible. Public-private partnerships can also leverage resources and expertise to facilitate the modernization process.
Initial Investment Costs
The initial investment required for modern manufacturing equipment, software, and training can be a significant obstacle, particularly for smaller businesses. Innovative financing options, such as government grants, low-interest loans, and leasing programs, can alleviate the financial burden. Furthermore, partnerships with technology providers can offer flexible payment plans and phased implementation strategies, enabling businesses to adapt their investment to their specific financial capacity.
Workforce Development Programs
Comprehensive workforce development programs are crucial for equipping employees with the skills needed for modern manufacturing. These programs should include hands-on training in new technologies, apprenticeships, and ongoing professional development opportunities. Successful programs often partner with local universities and community colleges to provide targeted training and certifications in areas like robotics, automation, and data analysis. For example, the success of the German dual vocational training system demonstrates the effectiveness of industry-university partnerships in fostering skilled workers.
Government Incentives and Financing Options
Government incentives and financial support programs can play a vital role in easing the transition to modern manufacturing. Tax credits, grants, and low-interest loans can help businesses cover the costs of new equipment, training, and infrastructure upgrades. These incentives can be particularly beneficial for smaller businesses that may lack the financial resources to undertake large-scale investments. Furthermore, streamlined application processes and clear guidelines can make these incentives more accessible.
Industry Partnerships
Collaborative efforts between industry leaders, manufacturers, and government agencies can create a supportive ecosystem for modern manufacturing. Partnerships can facilitate knowledge sharing, best practices, and resource allocation to support the transition. These partnerships can leverage the expertise of industry veterans and the latest technological advancements to foster a supportive network for businesses seeking to adopt modern practices. Industry-led initiatives can create shared training resources and promote a common understanding of the required skills and technologies.
Addressing the Skill Gap
Addressing the skill gap in modern manufacturing requires a multifaceted approach that encompasses both immediate and long-term strategies. Upskilling existing employees through targeted training programs and attracting new talent with competitive wages and benefits are essential components. Encouraging STEM education at the secondary and post-secondary levels will cultivate a future workforce with the technical skills necessary for modern manufacturing.
Moreover, fostering a culture of continuous learning and adaptation within the workforce is crucial for long-term success.
Future of Manufacturing
The future of manufacturing is poised for dramatic transformation, driven by technological advancements, evolving consumer demands, and a growing emphasis on sustainability. This dynamic landscape presents both significant challenges and exciting opportunities for growth and innovation. The convergence of digital technologies, advanced materials, and personalized production is reshaping traditional manufacturing models, creating new avenues for efficiency, customization, and environmental responsibility.The evolving landscape of modern manufacturing is characterized by a rapid pace of technological change.
This evolution necessitates a proactive approach to adapt and capitalize on emerging trends, ensuring a competitive advantage in the marketplace. Foresight and strategic planning are crucial for navigating the uncertainties and maximizing the opportunities presented by the future of manufacturing.
Future Trends in Modern Manufacturing
Emerging technologies are reshaping manufacturing processes, from design to production and distribution. 3D printing, for example, is enabling rapid prototyping and customized production, reducing lead times and lowering costs. Advanced materials, like carbon fiber composites and bio-based polymers, are finding applications across various sectors, improving performance and reducing environmental impact. Personalized manufacturing is gaining momentum, allowing companies to tailor products to individual customer needs and preferences.
Impact of Sustainable Manufacturing Practices
Sustainable manufacturing practices are becoming increasingly critical. Companies are adopting strategies to reduce their environmental footprint, from optimizing energy consumption and waste reduction to utilizing recycled materials and implementing circular economy models. These initiatives are not only environmentally responsible but also contribute to cost savings and enhance brand reputation. Examples of sustainable manufacturing include the use of renewable energy sources in production facilities, the development of closed-loop systems for material recovery, and the design of products with extended lifespans and recyclability.
Impact of Global Supply Chain Disruptions
Global supply chain disruptions have highlighted the vulnerability of traditional manufacturing models. These disruptions have emphasized the need for resilience and diversification. Companies are actively exploring strategies to reduce reliance on single sources, establish more geographically dispersed supply chains, and develop alternative sourcing options. This shift towards resilience fosters a more adaptable and sustainable manufacturing ecosystem.
Importance of Ethical Considerations
Ethical considerations are paramount in the future of manufacturing. Companies are increasingly scrutinized for their labor practices, supply chain transparency, and social responsibility. Fair labor standards, responsible sourcing, and ethical treatment of workers are essential elements of a sustainable and equitable manufacturing system. The implementation of ethical guidelines ensures that production processes are not only efficient but also contribute to a just and equitable society.
Specific Examples of Opportunities: Opportunities Abound In Modern Manufacturing
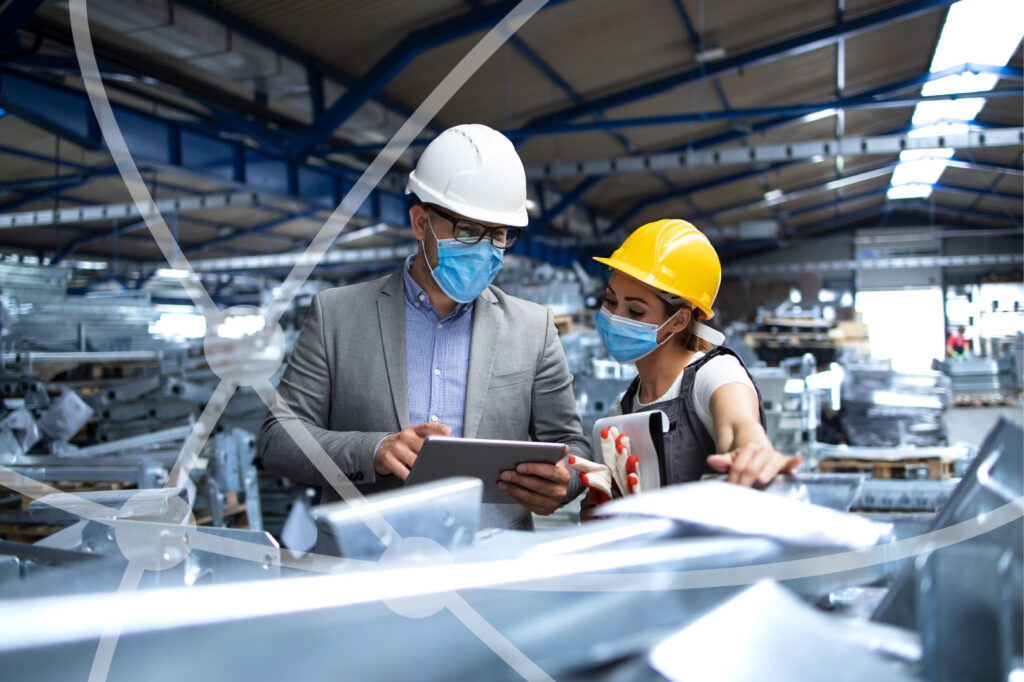
Modern manufacturing is undergoing a rapid transformation, driven by technological advancements and a growing emphasis on efficiency and sustainability. Companies are leveraging innovative techniques to optimize processes, reduce costs, and enhance product quality. This shift presents significant opportunities for businesses to gain a competitive edge and thrive in the evolving landscape.Successfully implementing modern manufacturing techniques requires a strategic approach, embracing automation, data analytics, and continuous improvement methodologies.
Companies that adapt to these trends are poised to reap substantial rewards in terms of increased profitability, enhanced product quality, and improved worker safety.
Companies Successfully Implementing Modern Manufacturing Techniques
Many companies have successfully adopted modern manufacturing techniques, leading to significant improvements in their operations. These implementations have resulted in cost savings, increased efficiency, and enhanced product quality. This showcases the tangible benefits of adopting these methodologies.
- Tesla’s Gigafactories: Tesla’s Gigafactories exemplify the integration of automation and advanced manufacturing technologies. Automated assembly lines, robotics, and sophisticated supply chain management systems have enabled Tesla to scale production while maintaining high-quality standards. The use of predictive maintenance and real-time data analysis allows for proactive problem-solving, minimizing downtime and optimizing resource allocation. This results in significant cost savings and improved delivery times.
These factories are a prime example of how automation can significantly increase efficiency and productivity.
- Toyota’s Lean Manufacturing System: Toyota’s long-standing commitment to lean manufacturing principles has consistently resulted in cost reductions and increased efficiency. Their emphasis on waste reduction, continuous improvement, and worker empowerment has fostered a culture of innovation and adaptability. This has led to reduced production times, minimized inventory levels, and improved product quality. Their focus on standardized processes and quality control ensures consistency and reliability in the manufacturing process.
- 3M’s Innovation Hubs: 3M’s decentralized innovation hubs promote a culture of experimentation and collaboration, fostering the development of new products and processes. This approach is aligned with modern manufacturing principles, facilitating rapid prototyping, flexible production, and a streamlined product lifecycle. This allows for a more agile response to changing market demands and customer needs, leading to the development of innovative products that meet specific needs.
Data Analytics for Identifying and Capitalizing on Opportunities
Data analytics plays a critical role in optimizing modern manufacturing operations. By leveraging data from various sources, companies can gain insights into production processes, identify bottlenecks, and optimize resource allocation. This allows for a proactive approach to problem-solving and enhanced decision-making.
- Predictive Maintenance: Companies are using data analytics to predict equipment failures before they occur, enabling proactive maintenance and minimizing downtime. This approach allows for efficient resource allocation and minimizes production disruptions, leading to increased efficiency and reduced costs. Data analysis allows for a better understanding of equipment performance trends, identifying potential issues before they escalate and require costly repairs.
- Demand Forecasting: Data analysis allows for accurate demand forecasting, enabling companies to optimize inventory levels and production schedules. This reduces waste, improves customer satisfaction, and optimizes resource utilization. By analyzing historical data and current market trends, companies can make informed decisions about inventory management, production planning, and resource allocation, resulting in cost savings and improved efficiency.
- Process Optimization: Data analytics provides insights into various production processes, allowing companies to identify bottlenecks, inefficiencies, and areas for improvement. This leads to optimized workflows and reduced production times. Through data analysis, companies can pinpoint specific areas of the manufacturing process that are causing delays or inefficiencies, enabling them to develop targeted solutions for optimization.
Automation for Optimizing Production Processes and Enhancing Worker Safety
Automation is revolutionizing modern manufacturing, enhancing production efficiency and worker safety. Robots and automated systems are taking over repetitive tasks, freeing up human workers for more complex and strategic roles. This leads to increased output, reduced errors, and improved overall productivity.
- Robotic Process Automation (RPA): RPA automates repetitive tasks in various stages of the manufacturing process, such as data entry, order processing, and quality control. This allows human workers to focus on higher-value activities, improving productivity and accuracy. This results in reduced errors, increased efficiency, and enhanced worker safety.
- Automated Guided Vehicles (AGVs): AGVs streamline material handling, transporting materials between different production stages. This minimizes manual handling, reduces the risk of errors, and improves the overall flow of the manufacturing process. AGVs can efficiently and safely transport materials, minimizing human interaction with potentially hazardous materials and processes.
- Cobots (Collaborative Robots): Cobots work alongside human workers, performing tasks such as assembly, packaging, and material handling. This improves worker safety by reducing exposure to hazardous materials or repetitive movements. This creates a more efficient and safer workspace, increasing productivity while minimizing potential risks to human workers.
Case Studies of Successful Companies in Modern Manufacturing
Company | Strategy | Impact | Metrics |
---|---|---|---|
Tesla | Automation, data analytics, advanced manufacturing | Increased production efficiency, reduced costs, improved product quality | Increased production volume, reduced manufacturing time, improved customer satisfaction |
Toyota | Lean manufacturing, continuous improvement | Reduced waste, increased efficiency, improved product quality | Reduced inventory levels, minimized production time, improved customer satisfaction |
3M | Innovation hubs, flexible production | Rapid product development, agile response to market demands | Increased product innovation, improved market share, faster time to market |
Global Perspectives on Opportunities
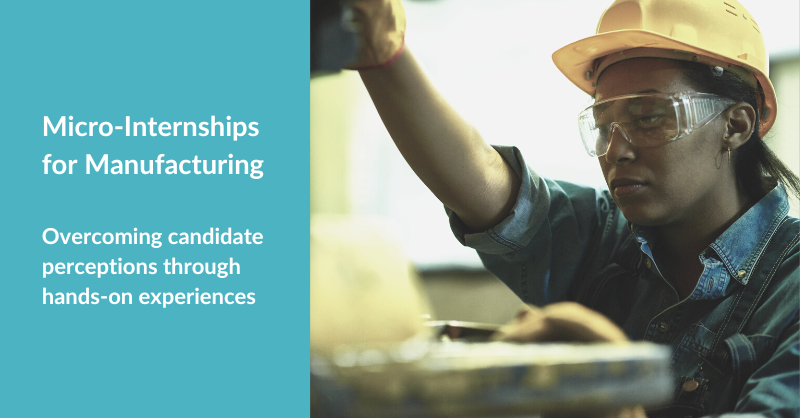
The global landscape of modern manufacturing presents a complex interplay of opportunities and challenges. Understanding how different nations approach manufacturing, the impact of global trade agreements, and the competitive pressures at play is crucial for businesses seeking to succeed in this dynamic environment. This exploration delves into the nuances of the global manufacturing ecosystem, highlighting key factors influencing opportunities and potential pitfalls.The global manufacturing landscape is no longer defined by national borders.
Companies must navigate a complex web of regulations, trade policies, and cultural differences to capitalize on global opportunities. This includes understanding the varying levels of technological advancement, labor costs, and infrastructure in different countries. The interplay of these factors directly impacts manufacturing strategies and the competitive positioning of businesses.
Influence of Global Markets and Regulations
Global markets present both immense potential and significant hurdles for modern manufacturers. Varying consumer preferences, cultural norms, and technological adoption rates across different regions necessitate tailored product development and marketing strategies. Regulations concerning environmental standards, labor practices, and product safety also significantly impact manufacturing operations. Compliance with these regulations can be a substantial cost consideration, and differences in standards across nations can create complex logistical challenges.
Different Approaches to Modern Manufacturing
Different countries exhibit diverse approaches to modern manufacturing, reflecting varying priorities and economic structures. Some nations emphasize automation and advanced technologies, while others prioritize cost-effective labor models. This leads to a spectrum of manufacturing capabilities and specializations. The implications for businesses include strategic decisions about where to source materials, manufacture products, and market them globally. For example, countries with strong research and development capabilities might excel in high-tech manufacturing, while countries with abundant low-cost labor might be well-suited for labor-intensive production.
Role of International Trade Agreements and Collaborations
International trade agreements and collaborations play a vital role in shaping global manufacturing opportunities. Agreements like the Comprehensive and Progressive Agreement for Trans-Pacific Partnership (CPTPP) and the Regional Comprehensive Economic Partnership (RCEP) aim to reduce trade barriers and foster economic integration. These agreements create pathways for companies to access new markets and source materials more efficiently. Joint ventures and partnerships between companies from different countries can lead to the sharing of knowledge, technology, and resources, resulting in increased competitiveness and innovation.
Impact of Global Competition on Modern Manufacturing
Global competition significantly impacts modern manufacturing. Businesses must adapt to evolving market demands, technological advancements, and the emergence of new competitors. This requires continuous innovation, cost optimization, and a focus on quality and efficiency. Companies must also consider the potential impact of geopolitical events, such as trade disputes and supply chain disruptions. An example of this dynamic is the increasing prevalence of reshoring and nearshoring initiatives as companies seek to reduce reliance on geographically distant suppliers and mitigate supply chain vulnerabilities.
Comprehensive Overview of the Global Manufacturing Landscape
The global manufacturing landscape is characterized by a diverse range of manufacturing capabilities and specializations across countries. Understanding this diversity is critical for businesses seeking to participate in global markets. Key factors influencing the landscape include technological advancements, labor costs, infrastructure, and government regulations. A global manufacturer should carefully assess these factors and their implications for supply chains, production costs, and market access.
For instance, China’s significant manufacturing base has been a driver of global supply chains, while countries like Germany remain prominent in high-tech manufacturing.
Outcome Summary
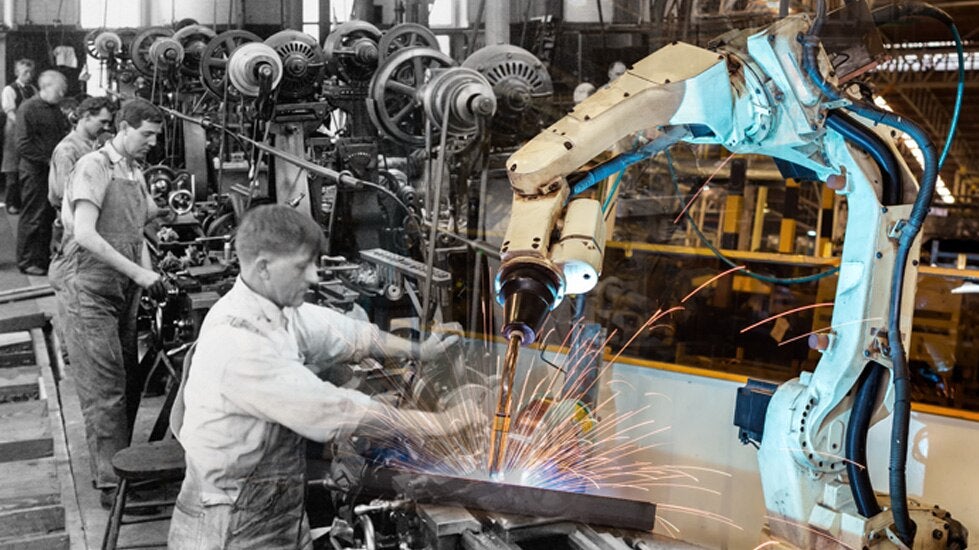
In conclusion, modern manufacturing presents a wealth of opportunities for growth and innovation. While challenges like workforce retraining and infrastructure upgrades exist, the potential rewards – from increased efficiency to enhanced product quality – are substantial. By embracing new technologies, developing robust strategies, and prioritizing ethical considerations, companies can navigate the complexities of the modern manufacturing landscape and position themselves for future success.
The future of manufacturing is bright, and these opportunities are waiting to be seized.