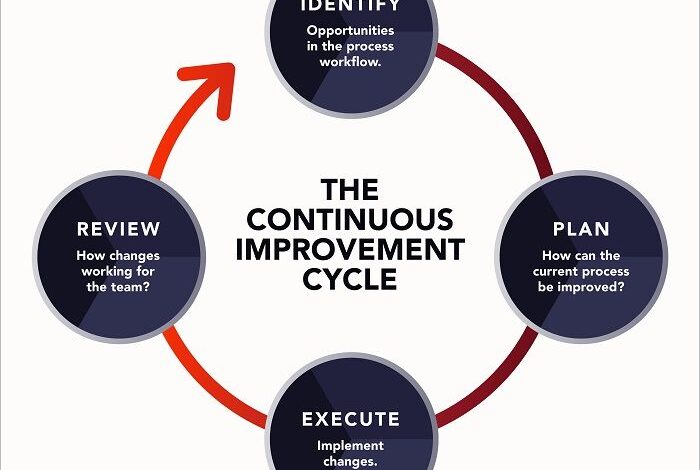
Continuous Improvement Details Matter
Continuous improvement because details matter is a cornerstone of success in any field. It’s not just about big leaps, but about meticulously refining processes through small, incremental changes. From manufacturing to customer service, understanding and addressing the minutiae can unlock significant improvements in efficiency, quality, and overall satisfaction. This exploration dives into the why and how of this powerful approach.
This blog post delves into the core principles of continuous improvement, highlighting the critical role of details. We’ll examine methodologies like Lean and Six Sigma, explore practical applications across various industries, and discuss the essential tools and strategies for cultivating a detail-oriented culture within any organization. Get ready to uncover how paying attention to the small stuff can lead to remarkable results.
Defining Continuous Improvement
Continuous improvement is a systematic approach to enhance processes, products, and services over time. It’s not a one-time fix, but rather a journey of incremental enhancements, driven by a commitment to learning and adaptation. This iterative process focuses on identifying areas for improvement and implementing small, sustainable changes that lead to significant long-term benefits. This philosophy is crucial for organizations aiming for sustained success in a dynamic environment.This continuous improvement journey involves a proactive mindset, constantly seeking ways to optimize operations and deliver better outcomes.
It’s about embracing change as an opportunity for growth and building a culture of improvement within the organization.
Continuous improvement is all about the little things, the details that often get overlooked. A great example of this principle in action is the Stevens Points Breast Care Center receiving redesignation, showcasing how meticulous attention to quality can lead to positive outcomes for patients. This recognition highlights how focusing on the details, from procedures to patient care, ultimately drives excellence in healthcare, reinforcing the importance of continuous improvement.
Stevens Points Breast Care Center receives redesignation is a testament to the power of paying close attention to the details.
Core Principles of Continuous Improvement
The core principles of continuous improvement are fundamental to its success. They provide a framework for identifying areas for improvement and implementing solutions. A key element is the focus on small, incremental changes. Large-scale transformations, while potentially impactful, often encounter resistance and can be more difficult to implement and maintain. Small, incremental improvements are easier to manage and sustain, fostering a culture of continuous improvement over time.
Continuous Improvement Methodologies
Several methodologies support the continuous improvement process. These methodologies provide structured frameworks for implementing and sustaining continuous improvement efforts. Understanding the nuances of each approach is vital to selecting the best fit for specific needs and circumstances.
- Lean: This methodology emphasizes eliminating waste and maximizing value in processes. It focuses on streamlining workflows, reducing bottlenecks, and improving efficiency through tools like Value Stream Mapping and 5S. Lean principles are widely applicable in manufacturing, but also applicable in other industries such as customer service and software development.
- Six Sigma: This data-driven approach focuses on reducing defects and variation in processes. It uses statistical tools and methodologies to identify and eliminate defects, ultimately improving quality and reducing costs. Six Sigma methodologies are particularly effective in manufacturing and service industries where high quality is paramount.
- Kaizen: This Japanese philosophy translates to “continuous improvement.” It emphasizes small, incremental changes implemented on a regular basis. It involves involving all employees in the improvement process, fostering a culture of continuous learning and problem-solving. Kaizen events are often used to facilitate rapid improvement initiatives.
Comparison of Continuous Improvement Approaches
Different methodologies have varying strengths and weaknesses. The optimal choice depends on the specific context and goals of the organization.
Methodology | Strengths | Weaknesses |
---|---|---|
Lean | Focuses on eliminating waste, streamlining processes, and improving efficiency. | May not be suitable for complex or highly regulated industries. |
Six Sigma | Data-driven approach, focus on quality and reducing defects, statistical tools are powerful. | Can be resource-intensive and may require significant training. |
Kaizen | Involves all employees, promotes a culture of continuous improvement, focuses on small, incremental changes. | Requires strong leadership and commitment from all levels of the organization. |
Implementing Continuous Improvement
A simple framework for implementing continuous improvement within a team or organization involves these key steps:
- Define Goals: Clearly articulate the objectives and desired outcomes of the continuous improvement initiative. This involves understanding the current state of the process, identifying problems, and determining the desired future state.
- Identify Areas for Improvement: Analyze the current processes to pinpoint areas where improvements are needed. Use data and feedback to understand current issues and challenges.
- Develop Solutions: Brainstorm and evaluate potential solutions to address identified problems. Encourage collaboration and input from all team members.
- Implement Solutions: Put the chosen solutions into action, making small, incremental changes. Monitor progress closely and adjust the plan as needed.
- Measure and Evaluate: Track the results of the implemented solutions. Gather data to assess the impact of the changes. Use data to inform future improvement efforts.
- Sustain Improvements: Continuously monitor and refine the process to maintain the achieved improvements. Regular reviews and adjustments are crucial to sustain progress.
The Importance of Details

Continuous improvement isn’t just about sweeping changes; it’s about meticulously refining processes, one detail at a time. Ignoring the seemingly insignificant elements can lead to costly errors and hinder overall progress. A focus on details allows for a deeper understanding of the system, identifying potential bottlenecks and inefficiencies, ultimately leading to a more robust and effective operation.Paying close attention to the nuances of a process allows for proactive problem-solving, reducing the likelihood of unforeseen issues and costly rework later on.
By acknowledging and addressing minor details, we build a foundation for sustainable improvement.
Crucial Role of Details in Continuous Improvement
Focusing on details is paramount for achieving successful continuous improvement. Small, seemingly inconsequential aspects of a process can have a disproportionately large impact on overall efficiency and effectiveness. For instance, a slightly miscalibrated machine tool can lead to a substantial loss of precision in manufacturing, resulting in costly repairs and delays.
Impact of Minor Details on Efficiency and Effectiveness
Minor details, if overlooked, can have significant repercussions on a process’s overall efficiency and effectiveness. A poorly designed form, for example, can lead to data entry errors, slowing down the entire workflow. A small change in a software program’s interface, if not thoroughly tested, can result in unexpected errors that bring down the entire system.
Examples of Problems Arising from Neglecting Details
Neglecting details can lead to a variety of significant problems in a process. A common example is a manufacturing line where a seemingly minor issue with the conveyor belt’s alignment causes product damage and increased downtime. In customer service, failing to document customer feedback on a particular product feature can lead to missed opportunities for improvement and potentially cause dissatisfaction.
These are just a few examples of how seemingly minor details can cascade into larger, more complex issues.
Obstacles to Detail-Oriented Work Environments
Several obstacles can hinder a detail-oriented work environment. A pressure to meet immediate deadlines, a lack of proper training on the importance of meticulousness, and a lack of recognition for thorough work can all contribute to a culture that undervalues attention to detail. Moreover, a lack of standardized procedures and insufficient communication channels can also create difficulties in consistently maintaining attention to detail.
Methods for Fostering a Detail-Oriented Culture
Cultivating a culture that values and prioritizes details requires a multifaceted approach. Implement detailed training programs emphasizing the significance of accuracy and precision in all tasks. Establish clear guidelines and standards for work procedures, ensuring consistency across the organization. Implement systems for immediate feedback and recognition of high-quality work, fostering a culture of accountability. Promote open communication channels and encourage a collaborative approach to problem-solving, where team members feel comfortable raising concerns about minor details.
Regular review and adjustment of established processes based on real-time feedback and data analysis will help reinforce the importance of details. Create a culture that encourages asking questions and exploring alternatives.
Practical Applications: Continuous Improvement Because Details Matter
Continuous improvement isn’t just a theoretical concept; it’s a powerful tool for achieving tangible results across various industries. By focusing on the details, organizations can identify areas for optimization, boost efficiency, and ultimately, enhance the overall customer experience. The key lies in a systematic approach to process evaluation, identifying pain points, and implementing targeted solutions.Implementing continuous improvement initiatives requires a proactive mindset, coupled with a willingness to adapt and learn.
This means embracing change, encouraging open communication, and fostering a culture of accountability. The value proposition is undeniable: reduced costs, increased productivity, improved quality, and delighted customers.
Examples of Continuous Improvement Initiatives
Various industries have successfully leveraged continuous improvement initiatives, demonstrating the profound impact of meticulous attention to detail. For instance, a manufacturing company might implement a system for tracking defects at each stage of production. This detailed approach can identify recurring issues and facilitate corrective actions, ultimately reducing waste and improving output. Similarly, in customer service, analyzing customer feedback and identifying common complaints allows companies to fine-tune their processes and deliver a superior experience.
Case Studies of Process Optimization
Numerous case studies showcase the significant impact of meticulous detail-oriented work on process optimization. One example involves a software development team that meticulously tracked bug reports, analyzing patterns and implementing preventative measures. This led to a substantial decrease in post-release bugs and significantly improved customer satisfaction. Another instance comes from a retail store that analyzed sales data by product category and time of day.
Continuous improvement, because the details truly matter, is crucial for any business. A focus on the small things, like ensuring your brand is genuinely representing your values, is key to long-term success. This authenticity is essential to brand building, as consumers can easily sniff out inauthenticity. By understanding that, you can build a more robust and trustworthy brand.
Authenticity is essential to brand building. Ultimately, a commitment to meticulous details fuels a brand’s integrity, fostering trust and loyalty, which leads to sustained growth.
This enabled them to optimize inventory management, reduce waste, and improve profitability.
Impact on Customer Satisfaction
Continuous improvement initiatives, driven by attention to detail, can significantly enhance customer satisfaction. Consider a customer service department that meticulously tracks response times to customer inquiries. By identifying bottlenecks and streamlining workflows, they can reduce response times, leading to improved customer satisfaction scores and a more positive brand image. This translates to increased customer loyalty and advocacy.
Impact on Deliverables and Services
The quality of deliverables and services is directly correlated with attention to detail. A meticulous approach to project planning, execution, and quality control ensures the final product meets the desired standards. This applies to everything from manufacturing a product to providing customer support. For instance, a construction company that meticulously adheres to building codes and safety regulations delivers higher quality buildings and safeguards the workforce.
Similarly, a software company that prioritizes code quality and testing ensures that their software functions reliably and meets user expectations.
Continuous improvement is all about the details, and that’s true across the board. From optimizing everyday processes to designing the next generation of energy solutions, attention to the minutiae is key. This is especially evident in the future of sustainable energy, where innovative thinkers are exploring alternative materials to build more efficient and environmentally friendly systems, like those discussed in the future of sustainable energy looks to alternative materials.
Ultimately, whether it’s a new solar panel or a better widget, it all comes back to the power of paying attention to the details.
Table of Improvement Areas and Examples
Improvement Area | Specific Example | Impact |
---|---|---|
Manufacturing | Implementing a 5S methodology (Sort, Set in order, Shine, Standardize, Sustain) in the production line, and tracking the reduction in defects per unit | Increased output, reduced waste, enhanced product quality, and improved safety |
Customer Service | Improving response times to customer inquiries by implementing a CRM system with automated responses for common questions | Increased customer satisfaction, improved brand image, and reduced customer service costs |
Software Development | Using a version control system and implementing rigorous testing procedures at every stage of development | Reduced bugs in released software, improved code quality, and increased customer satisfaction |
Methods and Tools for Detail-Oriented Improvement
Continuous improvement isn’t just about big picture changes; it’s also about meticulously examining the smaller, often overlooked details. Effective continuous improvement strategies recognize that seemingly minor elements can significantly impact overall performance. This meticulous approach requires a suite of specific methods and tools, which will be explored in this section.These methods and tools, from visual aids to data analysis techniques, help us to identify bottlenecks, understand root causes, and implement targeted solutions for optimized performance.
By dissecting processes and understanding the interplay of factors, we can achieve significant gains.
Identifying Improvement Areas with Flowcharts and Process Maps
Flowcharts and process maps are visual representations of workflows. They provide a clear picture of each step, highlighting potential bottlenecks and inefficiencies. By visually mapping out the process, we can readily identify areas where steps might be redundant, overly complex, or where bottlenecks exist. This visualization facilitates better understanding of the process and allows us to pinpoint the exact locations of possible improvements.
Analyzing Data for Trends and Patterns
Statistical process control (SPC) is a powerful tool for identifying patterns and trends in data. SPC charts, like control charts, help track key metrics over time, allowing us to visualize variations and potential anomalies. By examining these charts, we can detect patterns and trends that may indicate underlying problems or inefficiencies in the process.
- Control charts are graphical representations of process data over time. They visually display the variation of a process, allowing for the identification of special causes of variation that might indicate problems or areas for improvement.
- Histograms visually represent the distribution of data, helping us understand the frequency of different values and potential issues with the data.
- Pareto charts prioritize problems based on their impact, allowing us to focus on the most critical areas for improvement first.
Uncovering Root Causes
Root cause analysis (RCA) is a structured approach to identify the underlying reasons for problems. RCA goes beyond simply addressing symptoms and aims to understand the core causes that lead to issues, allowing us to implement long-lasting solutions. Several techniques can be employed for RCA, such as the 5 Whys method, the Fishbone Diagram (Ishikawa Diagram), or Fault Tree Analysis.
Evaluating Processes and Procedures
A well-designed checklist for evaluating processes and procedures can systematically identify potential areas for improvement. The checklist should include questions about efficiency, effectiveness, safety, and compliance. It should also encompass potential environmental considerations, ethical concerns, and any other applicable standards.
- For instance, if a checklist identifies a repeated error in data entry, this could suggest a need for better training or revised forms. This checklist should be tailored to the specific process being evaluated.
Example Checklist for Process Evaluation
Process Step | Criteria | Rating | Action Required |
---|---|---|---|
Data Entry | Accuracy of data | Fair | Implement training on data entry procedures. |
Data Validation | Time taken for validation | Poor | Optimize validation procedures and streamline the process. |
Report Generation | Clarity of report | Good | Maintain current procedures. |
Cultivating a Culture of Detail
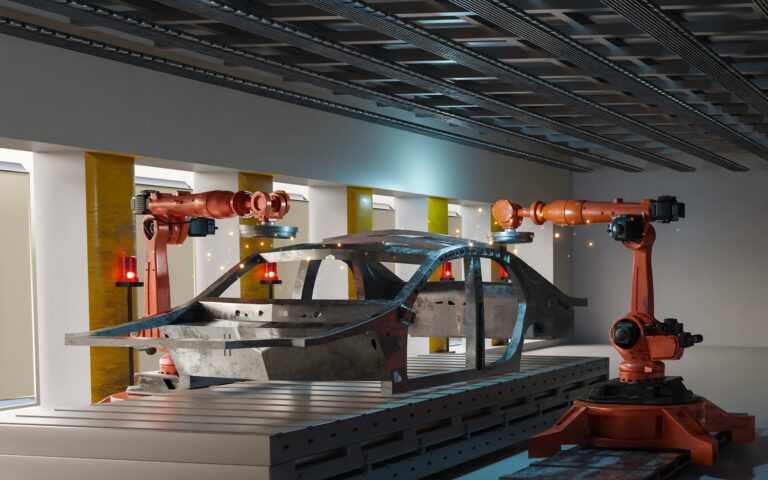
Cultivating a culture of detail is not just about implementing meticulous processes; it’s about fostering a mindset where every employee understands and embraces the importance of precision. This involves creating an environment where attention to detail isn’t viewed as a burden, but as a crucial component of success. It’s about empowering individuals to actively seek out and address potential issues, leading to a continuous cycle of improvement.A strong culture of detail is built on shared values and a commitment to excellence.
Employees need to understand that even seemingly minor details can significantly impact the overall quality and efficiency of work. This understanding needs to be ingrained through consistent reinforcement and practical application.
Detail Strategies for Cultivating a Culture, Continuous improvement because details matter
Strategies for cultivating a culture that values continuous improvement and attention to detail involve several key elements. Firstly, clear communication of the importance of detail is paramount. This must extend beyond theoretical discussions to practical examples of how detail leads to tangible improvements. Secondly, providing employees with the necessary resources and training to perform their duties with precision is critical.
This includes access to appropriate tools, technology, and knowledge.
Fostering a Learning Environment
A learning environment where employees feel comfortable sharing ideas and suggestions is essential. Open communication channels are crucial for encouraging input from all levels of the organization. This can be achieved through regular team meetings, suggestion boxes, or online forums. Anonymity can sometimes encourage honest feedback, which can be particularly helpful when dealing with sensitive issues. Leaders must actively listen to these suggestions and acknowledge the contributions of those who share them.
Effective Communication Methods
Effective communication methods for sharing details and insights across teams are vital. Regular progress reports, visual dashboards, and project management tools can facilitate clear and consistent communication. Training in active listening and constructive feedback is also essential. Meetings shouldn’t just be about delivering information; they should be platforms for discussion, questions, and clarification. Using visual aids, such as flowcharts or diagrams, can enhance understanding and facilitate the dissemination of complex details.
The Role of Leadership
Leadership plays a critical role in promoting attention to detail and continuous improvement. Leaders must embody the values of precision and meticulousness in their own actions and decisions. They must also create a safe space for employees to voice concerns and suggestions, without fear of retribution. Leaders who champion continuous improvement and actively listen to feedback are instrumental in fostering a detailed-oriented culture.
Examples of Leadership Behaviors
The table below illustrates leadership behaviors that support continuous improvement:
Leadership Behavior | Description | Impact |
---|---|---|
Active Listening | Pay close attention to what others say, acknowledging and understanding their perspectives. | Increased collaboration, effective problem-solving, and improved understanding of team dynamics. |
Encouraging Feedback | Actively solicit and value feedback from all team members, creating a culture of open communication. | Increased innovation, improved decision-making, and a stronger sense of team ownership. |
Demonstrating Precision | Setting a high standard of detail and precision in their own work, serving as a role model for the team. | Improved quality of work, increased efficiency, and a stronger commitment to accuracy. |
Providing Resources | Ensuring employees have access to the tools, training, and information they need to perform their jobs accurately. | Increased productivity, higher quality output, and a more efficient workflow. |
Challenges and Solutions
Embarking on a continuous improvement journey, especially one emphasizing meticulous detail, often encounters unexpected hurdles. Resistance to change, difficulties in analysis, and maintaining momentum are common challenges. Overcoming these obstacles is crucial for the success of any detail-oriented improvement initiative. This section explores strategies to address these issues, fostering a culture of meticulousness and sustained improvement.
Resistance to Change and Fostering Buy-In
Implementing continuous improvement initiatives that prioritize details frequently faces resistance from employees accustomed to established procedures. This resistance can stem from fear of the unknown, perceived loss of control, or a lack of understanding regarding the benefits of the changes. Strategies to overcome this resistance center on clear communication, participation, and demonstrating the value proposition.
- Open Communication: Transparent communication about the reasons behind the changes, the anticipated benefits, and the specific roles of each team member is essential. This should include regular updates and opportunities for questions and feedback.
- Employee Involvement: Involving employees in the design and implementation phases fosters a sense of ownership and buy-in. Allowing them to contribute their ideas and experience makes the transition smoother and more effective.
- Demonstrating Value: Highlighting concrete examples of how similar detail-oriented improvements have benefited other organizations or teams can effectively showcase the advantages. Quantifiable results and positive impacts on efficiency or quality are persuasive.
Obstacles to Detailed Analysis and Problem-Solving
Detailed analysis requires a specific skill set and often demands time and resources. Time constraints, a lack of training, or inadequate resources can impede thorough analysis and effective problem-solving.
- Lack of Training: Providing comprehensive training on analytical methodologies, data interpretation, and problem-solving techniques empowers teams to approach issues with precision and depth. This can involve workshops, mentorship programs, or online resources.
- Resource Constraints: Adequate resources, including access to necessary tools and software, are critical. Lack of access to data, computing power, or specialized tools can significantly hinder the analysis process. Seeking funding for necessary resources can be a key step.
- Time Constraints: Dedicated time for detailed analysis is essential. Short deadlines or conflicting priorities can lead to superficial analyses. Prioritizing detailed analysis in the schedule and establishing clear timelines can help overcome this obstacle.
Managing and Motivating Teams
Effective management and motivation are crucial for sustained engagement and productivity during the implementation of continuous improvement initiatives.
- Team Empowerment: Empowering teams to take ownership of the improvement process fosters a sense of responsibility and motivation. Clear roles and responsibilities, as well as autonomy to implement solutions, are crucial.
- Recognition and Rewards: Recognizing and rewarding individuals and teams for their contributions to the improvement process fosters a positive work environment and reinforces the value of meticulous work. This can range from public acknowledgement to tangible rewards.
- Regular Check-ins and Support: Regular check-ins and support from management help address any challenges or concerns promptly. This creates a supportive environment where team members feel heard and understood.
Maintaining Consistency
Maintaining consistent focus on details throughout the improvement process is critical. A lack of consistency can lead to setbacks and undermine the overall effectiveness of the initiative.
- Establishing Clear Metrics: Defining clear, measurable metrics helps track progress and identify areas needing further attention. Regular monitoring of these metrics helps maintain the focus on detail.
- Continuous Training and Development: Ongoing training and development programs keep teams updated on the latest methodologies and tools, ensuring a consistent approach to detail-oriented improvements. This could involve refresher courses, workshops, or access to relevant literature.
- Creating a Culture of Continuous Improvement: Integrating continuous improvement into the company culture ensures a consistent commitment to detail at all levels. This includes emphasizing the importance of detail in daily tasks and projects, creating a culture of learning and improvement.
Summary

In conclusion, continuous improvement because details matter is a powerful engine for growth and optimization. By focusing on small, incremental changes and meticulously attending to every detail, organizations can achieve significant improvements in efficiency, quality, and customer satisfaction. This approach transcends industries, empowering teams and individuals to consistently refine their processes and achieve greater success. The key takeaway?
Don’t underestimate the power of the details.