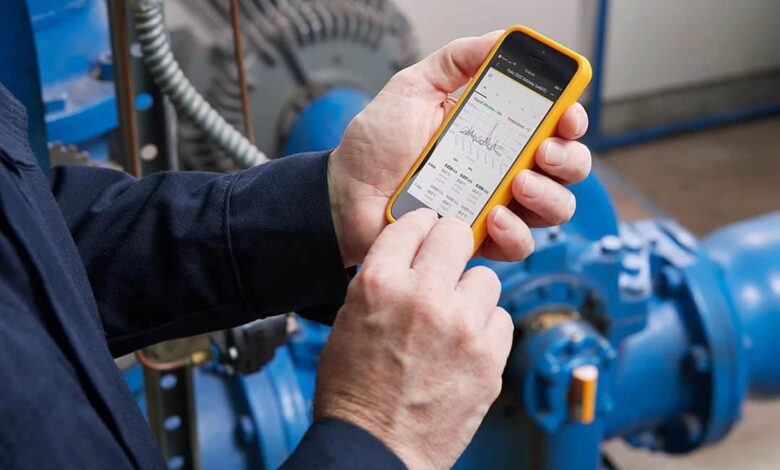
Condition Monitoring Safety & Efficiency Focus
Condition monitoring focuses on safety efficiency by proactively identifying potential equipment failures. This approach dramatically reduces downtime and improves overall operational efficiency across various industries. It’s about more than just maintenance; it’s about understanding the “health” of your machinery and proactively addressing issues before they escalate into costly breakdowns or safety hazards.
By analyzing data from sensors and other monitoring tools, condition monitoring allows for predictive maintenance, minimizing unexpected shutdowns and maximizing operational uptime. This approach directly translates into improved safety procedures and substantial cost savings. From energy production to manufacturing, the principles of condition monitoring are crucial for optimizing performance and ensuring a safe working environment.
Introduction to Condition Monitoring
Condition monitoring is a proactive approach to maintaining equipment and systems by continuously assessing their health and performance. Instead of waiting for failures to occur, condition monitoring identifies potential issues early, enabling preventative maintenance and minimizing downtime. This approach significantly improves safety and efficiency across various industries.Condition monitoring leverages a range of techniques to gather data about equipment’s operating parameters, such as vibration, temperature, sound, and pressure.
Analyzing this data helps predict potential failures and schedule maintenance before costly breakdowns or safety incidents occur.
Condition Monitoring Techniques
Condition monitoring encompasses various techniques, each with its strengths and weaknesses. These techniques provide insights into equipment health, enabling timely interventions.
- Vibration Analysis: This technique analyzes the vibrations of machinery components to detect anomalies that indicate wear, misalignment, or other potential issues. Vibration analysis is a valuable tool for detecting early warning signs of impending failures in rotating equipment, like pumps, motors, and gears. Abnormal vibrations can indicate bearing damage, imbalance, or looseness, allowing for proactive maintenance.
- Thermography: Thermography uses infrared cameras to identify variations in surface temperature. This method is particularly useful for detecting overheating, which can indicate electrical faults, lubrication problems, or other issues. High temperatures in specific areas can signal a problem requiring immediate attention. For example, a significantly hotter bearing might suggest inadequate lubrication, potentially leading to catastrophic failure if not addressed.
- Acoustic Emission: Acoustic emission monitoring listens for subtle sounds produced by material deformation. This technique helps detect cracks, stress corrosion, or other structural damage, often in early stages. Monitoring acoustic emission is crucial in industries like oil and gas or nuclear power, where structural integrity is paramount.
- Oil Analysis: This method involves analyzing the condition of lubricants used in machinery. Changes in oil parameters like viscosity, acidity, or particle count can indicate wear, contamination, or other issues. Oil analysis allows for early detection of problems in critical components like gears, bearings, and pumps. For example, an unusually high concentration of metal particles in the oil could signify impending bearing failure.
Applications of Condition Monitoring Across Industries
Condition monitoring finds widespread use across various industries, enhancing safety and efficiency.
- Manufacturing: Condition monitoring helps maintain production lines, preventing equipment failures that halt manufacturing processes. Monitoring equipment in manufacturing plants helps maintain high output, minimizing downtime and improving overall productivity.
- Power Generation: In power plants, condition monitoring is essential for ensuring the reliability and safety of turbines, generators, and other critical equipment. Predictive maintenance, facilitated by condition monitoring, can prevent unexpected outages and improve the efficiency of power generation.
- Oil and Gas: Condition monitoring is crucial for the safety and efficiency of oil and gas exploration and production equipment. This industry relies heavily on detecting early signs of equipment damage, minimizing risks and maximizing production.
- Transportation: In transportation systems, condition monitoring helps ensure the safe and efficient operation of vehicles, trains, and aircraft. Predictive maintenance of engines, brakes, and other critical components enhances safety and reduces operational costs.
Real-World Examples of Condition Monitoring
Condition monitoring is not just theoretical; it’s a practical application in many industries.
- Example 1: A manufacturing plant implemented vibration analysis on its conveyor belts. Early detection of anomalies allowed for preventative maintenance, reducing downtime by 15% and preventing potential safety hazards.
- Example 2: A power plant utilizes thermography to monitor the temperature of its steam turbines. Early identification of overheating issues prevented a catastrophic failure, avoiding significant damage and costly repairs.
Advantages and Disadvantages of Condition Monitoring Methods
Method | Advantages | Disadvantages |
---|---|---|
Vibration Analysis | Early detection of mechanical issues, relatively inexpensive, widely available | Requires skilled personnel for interpretation, may not detect all issues, susceptible to environmental factors |
Thermography | Rapid detection of overheating, non-intrusive, visual | Limited in detecting internal issues, requires specific training, can be affected by ambient conditions |
Acoustic Emission | Early detection of structural damage, provides detailed information | Interpretation can be complex, costly equipment, requires skilled personnel |
Oil Analysis | Early detection of wear, contamination, and lubrication problems, useful for assessing the health of components | Requires laboratory analysis, may not detect all issues immediately, interpretation can be complex |
Safety Aspects of Condition Monitoring
Condition monitoring isn’t just about maximizing equipment uptime; it’s a crucial safety measure. By proactively identifying potential equipment failures, we can mitigate risks and prevent catastrophic incidents. This proactive approach allows for preventative maintenance, reducing the likelihood of unexpected breakdowns and associated hazards. A strong safety culture, integrated with condition monitoring, creates a safer working environment for all personnel.Predictive maintenance, a key component of condition monitoring, plays a vital role in reducing downtime and safety hazards.
By analyzing data from sensors and other monitoring systems, we can anticipate equipment failures before they occur. This foresight allows for timely maintenance, preventing sudden breakdowns that could lead to accidents or injuries.
Preventing Equipment Failures and Associated Risks
Condition monitoring enables the early detection of subtle changes in equipment performance. These changes, often imperceptible to the naked eye, can signal impending failures. By monitoring vibration levels, temperature fluctuations, or acoustic emissions, condition monitoring systems can identify anomalies that could lead to equipment breakdowns. These early warnings allow for timely maintenance, preventing potentially hazardous situations. For instance, detecting a rising vibration level in a rotating machine can prevent a catastrophic bearing failure, preventing the machine from spinning out of control, a risk that could lead to injury or environmental damage.
Role of Predictive Maintenance in Reducing Downtime and Safety Hazards
Predictive maintenance, enabled by condition monitoring, minimizes downtime by scheduling maintenance when equipment is most likely to require it. This strategy prevents unscheduled downtime, which can create safety risks. If a piece of equipment is prone to sudden failure, condition monitoring allows maintenance to be performed when the equipment is stationary, reducing the risk of personnel injury during the maintenance process.
Consider a pump system. Condition monitoring can predict when a pump seal might fail. This prediction allows maintenance to be scheduled during a planned shutdown, avoiding potential leakage and safety hazards associated with a sudden pump failure.
Early Detection of Potential Problems Enhancing Safety Procedures
Early detection of potential problems, facilitated by condition monitoring, allows for the implementation of enhanced safety procedures. When a condition monitoring system flags a potential issue, it triggers an alert, allowing for proactive safety measures. This could include isolating the equipment, warning personnel of the hazard, or scheduling maintenance. For example, a chemical processing plant monitoring pressure fluctuations in a storage tank can identify a leak before it escalates into a major safety incident.
This early detection allows for prompt action, minimizing the risk of an uncontrolled release.
Safety Incidents Preventable Through Condition Monitoring
Numerous safety incidents could have been avoided through proactive condition monitoring. A paper mill experiencing a sudden drive shaft failure, for instance, could have been prevented by a condition monitoring system detecting the early warning signs of impending failure. Similarly, a train derailment caused by a faulty wheel bearing could have been averted by regular condition monitoring. These examples demonstrate the significant role condition monitoring plays in preventing safety incidents.
Comparison of Safety Protocols in Industries Using Condition Monitoring
Industry | Safety Protocol 1 | Safety Protocol 2 | Safety Protocol 3 | Comparison |
---|---|---|---|---|
Oil & Gas | Regular vibration analysis of pumps | Automated leak detection systems | Remote monitoring of wellhead pressure | Oil & Gas industries prioritize equipment integrity. Protocols often involve a combination of approaches, emphasizing safety during critical operations. |
Manufacturing | Predictive maintenance on critical machinery | Real-time monitoring of temperature and pressure | Automated safety shutdown systems | Manufacturing industries utilize condition monitoring for preventive maintenance, minimizing downtime and risk of equipment failure. |
Power Generation | Continuous monitoring of turbine vibrations | Predictive maintenance of generators | Automated shutdown systems in case of overloads | Power generation relies on condition monitoring to maintain equipment reliability and safety. |
This table illustrates how condition monitoring protocols are adapted to the specific safety concerns of different industries.
Efficiency Improvements through Condition Monitoring
Condition monitoring isn’t just about preventing breakdowns; it’s a powerful tool for boosting overall operational efficiency. By proactively identifying potential issues, businesses can optimize resource allocation, minimize downtime, and enhance operational processes. This approach leads to significant cost savings and increased productivity.Condition monitoring empowers companies to move beyond reactive maintenance, allowing for a proactive and strategic approach to asset management.
This translates into improved equipment lifespan, reduced repair costs, and ultimately, a more profitable operation.
Condition monitoring is all about boosting safety and efficiency. It’s crucial for everything from industrial processes to, say, the health of our waterways. Organizations like sustaining our waters the fox wolf watershed alliance are working hard to protect our precious water sources, which directly impacts the overall safety and efficiency of our systems. Ultimately, strong condition monitoring practices lead to a more secure and productive environment for everyone.
Optimized Resource Allocation
Condition monitoring enables a more precise allocation of resources. By identifying the true health of equipment, businesses can prioritize maintenance tasks and allocate personnel and parts effectively. This targeted approach reduces unnecessary expenditure on preventative maintenance for healthy equipment while ensuring crucial maintenance is completed on potentially failing assets.
Minimized Equipment Downtime
Predictive maintenance is a cornerstone of condition monitoring. By anticipating potential failures, businesses can schedule maintenance during planned downtime, minimizing unexpected disruptions to production. This proactive approach minimizes lost production time, a significant contributor to operational efficiency. For example, a power plant using vibration analysis to detect early signs of bearing wear can schedule maintenance during scheduled outages, avoiding costly unscheduled shutdowns.
Enhanced Operational Efficiency
Proactive maintenance, a key outcome of condition monitoring, directly enhances operational efficiency. Regular inspections and analysis, coupled with timely maintenance, ensure equipment operates at peak performance, leading to higher output and lower operating costs. This efficiency is further amplified by reducing the need for costly emergency repairs.
Examples of Increased Productivity
Numerous industries have seen significant gains in productivity through condition monitoring. A manufacturing facility using sensor data to monitor machine performance can identify and resolve minor issues before they escalate, preventing costly production delays. In the aviation industry, aircraft engine health monitoring allows for timely maintenance, minimizing the risk of unexpected engine failures and ensuring consistent flight schedules.
Condition monitoring, focusing on safety and efficiency, is crucial for any operation. Transparency in business practices is also becoming increasingly important, and understanding legislation like the Corporate Transparency Act, which aims to improve corporate accountability and potentially affect various stakeholders, what is the corporate transparency act and who it will impact , is key for navigating this new landscape.
Ultimately, both transparency and effective condition monitoring contribute to a safer and more efficient workplace environment.
Cost-Benefit Analysis of Condition Monitoring Programs
| Cost Category | Description | Estimated Cost | Potential Savings | ROI (Estimated) ||—|—|—|—|—|| Initial Investment | Implementation costs (sensors, software, training) | $50,000 – $150,000 | $20,000 – $80,000 per year | 2-5 years || Ongoing Costs | Maintenance contracts, sensor replacements, personnel training | $10,000 – $30,000 per year | $30,000 – $100,000 per year | 1-3 years || Reduced Downtime Costs | Cost of lost production, emergency repairs | $50,000 – $200,000 per year | $100,000 – $500,000 per year | 1-2 years || Reduced Maintenance Costs | Reduced frequency of repairs, optimized parts usage | $15,000 – $50,000 per year | $25,000 – $75,000 per year | 1-2 years || Improved Productivity | Increased output, reduced waste | Varies significantly by industry | $50,000 – $250,000 per year | 1-3 years | Note: The figures in the table are estimates and can vary greatly depending on the specific industry, the size of the operation, and the complexity of the monitoring program.
Data Analysis and Interpretation in Condition Monitoring
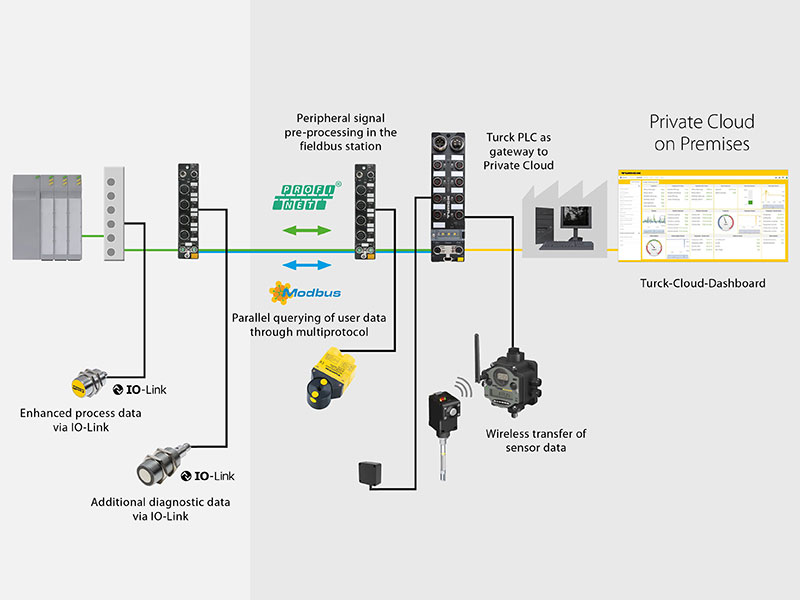
Condition monitoring systems generate vast amounts of data. Simply collecting this data isn’t enough; the real value lies in extracting meaningful insights from it. Effective data analysis allows us to understand equipment health, predict potential failures, and optimize maintenance strategies. This process involves a range of techniques and considerations, from sensor selection to data visualization and trend identification.The ability to interpret this data accurately is crucial for proactive maintenance.
By identifying subtle changes and patterns, we can anticipate equipment issues before they escalate into costly breakdowns. A well-structured analysis process is fundamental to achieving the full potential of condition monitoring.
Methods for Collecting and Analyzing Condition Monitoring Data
Data collection in condition monitoring often involves various sensors, ranging from vibration sensors to temperature sensors. Each sensor type provides specific data points that contribute to a holistic understanding of the equipment’s health. Sophisticated data acquisition systems record and process this data, enabling real-time monitoring and historical analysis. These systems need to be meticulously calibrated and maintained to ensure accuracy.Advanced analytical techniques, including statistical process control (SPC) and machine learning algorithms, are crucial for identifying anomalies and predicting potential failures.
These methods help sift through the massive datasets generated by condition monitoring systems to pinpoint significant patterns and trends.
Use of Sensors and Data Acquisition Systems
Sensors are the eyes and ears of a condition monitoring system. Different types of sensors measure various parameters, such as vibration, temperature, pressure, and acoustic emissions. The choice of sensors depends on the specific equipment and the type of information needed. For example, vibration sensors are excellent for detecting mechanical issues, while temperature sensors are vital for monitoring thermal stress.Data acquisition systems (DAQ) are the crucial link between sensors and the analysis process.
They collect, process, and transmit the data from various sensors. These systems must be carefully chosen and configured to ensure compatibility with the sensors and the data analysis tools used. Robust DAQ systems are essential for reliable data collection and accurate interpretation.
Significance of Data Visualization in Interpreting Condition Monitoring Data
Data visualization plays a vital role in understanding condition monitoring data. Visual representations, such as graphs, charts, and dashboards, transform complex data into easily digestible information. Visualizations help in identifying patterns, trends, and anomalies that might be missed in raw data tables. Effective visualization techniques are crucial for conveying insights effectively to operators and maintenance personnel.For instance, a plot showing vibration levels over time can clearly reveal unusual patterns that could indicate a developing bearing problem.
Interactive dashboards allow real-time monitoring and quick identification of critical parameters.
Data Analysis Techniques Applied to Condition Monitoring
The following table summarizes common data analysis techniques used in condition monitoring.
Technique | Description | Application |
---|---|---|
Statistical Process Control (SPC) | Used to monitor process variations and identify deviations from expected norms. | Identifying trends in vibration levels, temperature fluctuations, or pressure variations. |
Machine Learning (ML) | Algorithms learn from historical data to predict future outcomes and identify patterns. | Predicting equipment failures based on historical maintenance records and sensor data. |
Time Series Analysis | Focuses on analyzing data points collected over time to identify trends and patterns. | Monitoring equipment performance over time, identifying degradation, and predicting potential failures. |
Fault Detection and Diagnosis | Techniques used to identify the specific cause of a fault. | Pinpointing the root cause of a malfunctioning component. |
Interpreting Trends and Patterns in Condition Monitoring Data
Identifying trends and patterns in condition monitoring data is crucial for proactive maintenance. For example, a gradual increase in vibration levels over time might indicate a bearing nearing failure. Detecting such patterns early allows for timely maintenance interventions, preventing costly breakdowns.Careful observation of these trends, along with the use of predictive maintenance models, allows for more informed decisions about maintenance scheduling.
Understanding the specific patterns associated with different equipment issues is vital for effective interpretation. For instance, a sudden spike in temperature readings might indicate a localized overheating issue.
Condition monitoring, focusing on safety and efficiency, is crucial for any operation. Thinking about selling your business? Knowing the five key steps to successfully selling your business can help, especially if your current processes lack that efficiency. Five tips for selling a business are often overlooked, but incorporating them into your strategy can boost your final sales price.
Ultimately, robust condition monitoring ensures operational safety and boosts overall efficiency, crucial factors for any successful business, whether you’re selling it or not.
Integration of Condition Monitoring into Existing Systems
Integrating condition monitoring into existing industrial control systems is crucial for proactive maintenance and optimized performance. This seamless integration allows for real-time data analysis, enabling predictive maintenance strategies that minimize downtime and maximize equipment lifespan. By embedding condition monitoring tools within existing workflows, companies can significantly reduce operational costs and improve overall efficiency.
Methods for Integration
Condition monitoring integration can be achieved through various methods, each with its own strengths and limitations. Direct integration involves connecting condition monitoring sensors directly to the existing control system’s network. This method offers real-time data transmission and analysis, allowing for immediate responses to developing issues. Alternatively, data acquisition systems can be used to collect data from disparate sources and format it for analysis by the control system.
This approach is beneficial for systems with already established data collection pipelines. Lastly, cloud-based platforms offer a flexible and scalable approach, facilitating integration with various existing systems and providing access to sophisticated analytics tools.
Steps for Integration into Existing Workflows
A structured approach to integrating condition monitoring tools into existing workflows is essential for successful implementation. First, a thorough assessment of the current systems and processes is crucial. Identifying existing data sources, control systems, and communication protocols is paramount. Next, selecting appropriate condition monitoring tools that align with the assessed needs and existing infrastructure is critical. The tools should be compatible with the existing systems and offer the necessary data collection, analysis, and reporting capabilities.
Third, establishing clear data flow paths between the condition monitoring tools and the control system is essential. This involves defining data formats, communication protocols, and data storage locations. Finally, thorough testing and validation of the integrated system is vital to ensure proper functionality and data accuracy. The integration should be tested under various operating conditions to identify and address potential issues before deployment.
Software for Data Collection, Analysis, and Reporting
Numerous software solutions are available for data collection, analysis, and reporting in condition monitoring. Some popular choices include IBM Maximo, SAP Plant Maintenance, and specialized condition monitoring platforms from companies like Predictive Maintenance Solutions. These platforms typically offer features like sensor data acquisition, real-time monitoring dashboards, predictive analytics tools, and automated reporting mechanisms. For instance, IBM Maximo allows for integration with various industrial equipment and offers a comprehensive suite of maintenance management tools, including condition monitoring capabilities.
Such software solutions facilitate data visualization, trend analysis, and report generation for efficient decision-making.
Comparison of Software Solutions, Condition monitoring focuses on safety efficiency
Different software solutions cater to varying needs and budgets. IBM Maximo, for example, provides a robust platform suitable for large-scale industrial environments with extensive maintenance needs. SAP Plant Maintenance offers a comprehensive solution for companies with a strong SAP ecosystem. Specialized condition monitoring platforms, on the other hand, may offer more focused and specialized functionalities for particular industries or equipment types.
A key consideration in choosing a solution is the compatibility with existing infrastructure and the specific requirements for data analysis and reporting.
Compatibility of Condition Monitoring Tools
Condition Monitoring Tool | Operating Systems | Platforms |
---|---|---|
IBM Maximo | Windows, Linux | Various industrial control systems |
SAP Plant Maintenance | Windows | SAP-based systems |
Predictive Maintenance Solutions | Windows, Linux, Cloud-based | Various industrial control systems |
Other Specialized Tools | Variable (depending on vendor) | Specific equipment types |
This table provides a general overview of operating system and platform compatibility. Specific compatibility details should be verified with the vendor of the condition monitoring tool and the relevant industrial control system.
Case Studies of Condition Monitoring Successes
Condition monitoring is more than just a buzzword; it’s a powerful tool that’s transforming industries. Real-world case studies demonstrate how proactive maintenance, enabled by condition monitoring, leads to significant improvements in safety and efficiency. These examples highlight the tangible benefits of investing in this technology.Implementing a robust condition monitoring program isn’t a one-size-fits-all approach. The successful implementation of condition monitoring depends heavily on the specific needs and context of each industry and organization.
Case studies reveal the crucial steps, the challenges encountered, and the lessons learned. This allows us to analyze the best practices and tailor condition monitoring strategies to achieve maximum impact.
A Manufacturing Company’s Journey to Predictive Maintenance
This case study focuses on a mid-sized manufacturing company that transitioned from reactive to predictive maintenance. They experienced frequent breakdowns of critical machinery, leading to production downtime and costly repairs. By implementing vibration analysis and thermography, the company could detect subtle signs of equipment degradation well before major failures occurred.The implementation involved installing sensors on key equipment, collecting data, and analyzing trends.
The data analysis revealed patterns indicating potential failures. This allowed the company to schedule maintenance proactively, minimizing downtime and avoiding costly repairs. The result was a 20% reduction in unplanned downtime and a 15% decrease in maintenance costs.
Improving Efficiency in the Oil and Gas Industry
Condition monitoring has revolutionized efficiency in the oil and gas industry. This case study highlights how real-time monitoring of rotating equipment, such as pumps and compressors, improved efficiency in an oil refinery. The integration of advanced sensors, such as acoustic emission sensors, allowed for early detection of anomalies in the equipment.By monitoring vibrations, temperature, and pressure, the company could identify potential failures and schedule maintenance promptly.
This resulted in a 5% increase in production output and a 10% reduction in energy consumption. Furthermore, predictive maintenance enabled a 20% decrease in unplanned downtime.
Safety Improvements in a Power Plant
This case study showcases how condition monitoring enhanced safety in a power plant. The plant had a history of equipment failures leading to potential safety hazards. Using sophisticated sensors and advanced analytics, the plant implemented a condition monitoring system to monitor critical equipment, including turbines and generators.The system was designed to detect anomalies and provide real-time alerts. This early detection allowed the plant to take corrective action before equipment failures occurred, eliminating the risk of safety incidents.
The implementation resulted in a 30% reduction in the number of near misses and a significant improvement in the overall safety culture.
Summary of Case Studies
Case Study | Industry | Improvement in Safety | Improvement in Efficiency |
---|---|---|---|
Manufacturing Company | Manufacturing | Reduced unplanned downtime by 20% | Reduced maintenance costs by 15% |
Oil and Gas Refinery | Oil & Gas | N/A | Increased production by 5%, reduced energy consumption by 10% |
Power Plant | Power Generation | Reduced near misses by 30% | N/A |
These case studies demonstrate the multifaceted benefits of implementing a robust condition monitoring system. The quantified improvements highlight the significant return on investment associated with these programs. Proactive maintenance translates into cost savings, improved safety, and enhanced operational efficiency.
Future Trends in Condition Monitoring
Condition monitoring is rapidly evolving, driven by advancements in technology. This shift is propelling the field toward a future characterized by increased automation, predictive capabilities, and seamless integration with other systems. The focus is moving beyond simply detecting faults to proactively preventing them, leading to significant improvements in safety, efficiency, and overall operational performance.Emerging technologies are revolutionizing how we approach condition monitoring.
From AI-powered diagnostics to IoT-enabled real-time data collection, the future holds exciting possibilities for optimizing maintenance strategies and minimizing downtime. These advancements are not just theoretical; they are already impacting industries worldwide, demonstrating the transformative power of proactive maintenance.
Emerging Technologies and Their Impact
The integration of cutting-edge technologies is reshaping condition monitoring. This includes sophisticated sensor networks, powerful data analytics tools, and advanced machine learning algorithms. These tools enable a more comprehensive understanding of equipment health, allowing for earlier detection of potential issues and optimized maintenance scheduling.
Artificial Intelligence and Machine Learning in Condition Monitoring
AI and machine learning are revolutionizing condition monitoring by enabling predictive maintenance. Algorithms are trained on vast datasets of historical equipment performance data, enabling the identification of subtle patterns indicative of impending failures. This allows for proactive interventions, preventing costly breakdowns and improving overall operational efficiency. For example, AI models can analyze vibration data from machinery to predict potential bearing failures, enabling maintenance teams to intervene before the equipment fails.
Internet of Things (IoT) in Enhancing Condition Monitoring Capabilities
The Internet of Things (IoT) is playing a crucial role in enhancing condition monitoring. A network of interconnected sensors embedded within equipment collects real-time data on various parameters, such as temperature, pressure, and vibration. This constant stream of data allows for continuous monitoring and facilitates rapid identification of anomalies. The real-time data provided by the IoT enables proactive maintenance scheduling, reducing downtime and maximizing equipment lifespan.
Future Transformation of Condition Monitoring
This table Artikels how various emerging technologies will transform condition monitoring in the future.
Technology | Transformation in Condition Monitoring |
---|---|
AI/Machine Learning | Predictive maintenance, proactive intervention, early fault detection, optimized maintenance scheduling. |
IoT | Real-time data collection, continuous monitoring, improved data analysis, enhanced decision-making. |
Big Data Analytics | Pattern recognition, advanced diagnostics, comprehensive insights, data-driven optimization. |
Cloud Computing | Centralized data storage, enhanced accessibility, improved collaboration, scalability and cost-effectiveness. |
Edge Computing | Reduced latency, faster data processing, enhanced real-time insights, improved decision-making near the source of the data. |
Condition Monitoring for Specific Equipment Types
Condition monitoring is not a one-size-fits-all solution. Different equipment types, from rotating machinery to power generation systems, require tailored monitoring strategies. Understanding the unique characteristics and potential failure modes of each piece of equipment is crucial for effective preventative maintenance and optimized operational efficiency. This section delves into the specific condition monitoring strategies for various equipment types, offering practical examples and insights into the field.
Condition Monitoring for Rotating Machinery (Pumps and Compressors)
Rotating machinery, such as pumps and compressors, are critical components in many industrial processes. Predictive maintenance strategies for these types of equipment often focus on vibration analysis, acoustic emission, and oil analysis. Vibration analysis monitors the frequency and amplitude of vibrations, detecting anomalies that could signal impending bearing failures or imbalances. Acoustic emission monitoring detects subtle sounds produced during material fatigue or crack propagation.
Oil analysis examines the condition of lubricating oils for contaminants, wear particles, and other indicators of component deterioration. Early detection of these issues can prevent costly breakdowns and downtime. For instance, in a pump system, detecting a subtle increase in vibration levels can alert maintenance personnel to a potential bearing failure, allowing for timely replacement and preventing a complete pump failure.
Similar strategies apply to compressors, where monitoring pressure fluctuations and acoustic emissions can predict potential issues like valve wear or piston damage.
Condition Monitoring for Industrial Machinery (Motors and Gearboxes)
Motors and gearboxes are essential components in many industrial processes. Condition monitoring for these systems often involves temperature monitoring, vibration analysis, and motor current signature analysis (MCSA). Temperature monitoring helps detect overheating, a sign of potential winding insulation degradation or bearing failures. Vibration analysis is used to identify imbalances or misalignments in the motor and gearbox components. MCSA detects subtle changes in the motor’s current signature, offering early warnings of issues like rotor bar damage or winding problems.
Monitoring these parameters helps predict equipment failures, preventing downtime and potential catastrophic damage. For instance, an increase in the temperature of a motor’s windings might indicate a winding insulation failure, allowing for timely replacement and preventing a complete motor failure.
Condition Monitoring in the Energy Sector (Power Generation Equipment)
The energy sector relies heavily on large-scale power generation equipment like turbines and generators. Condition monitoring plays a crucial role in ensuring reliability and safety. Strategies commonly employed include vibration analysis, infrared thermography, and oil analysis. Vibration analysis helps detect imbalances, misalignments, and bearing wear in rotating equipment. Infrared thermography identifies hot spots on electrical components, indicating potential insulation failures or overheating.
Oil analysis examines the condition of lubricating oils for contaminants and wear particles, offering insights into the health of critical components. By proactively monitoring these parameters, the energy sector can minimize downtime and maximize the lifespan of their power generation equipment. For example, detecting an increase in vibration in a turbine’s shaft can alert operators to potential bearing issues, allowing for preventative maintenance and preventing a major plant outage.
Condition Monitoring in the Manufacturing Sector (Specific Machinery)
Within the manufacturing sector, different machinery types require different monitoring strategies. Condition monitoring for specific machines, such as injection molding machines, CNC machining centers, and metal cutting tools, may involve monitoring parameters like pressure, temperature, and tool wear. For injection molding machines, monitoring the pressure and temperature of the molding process can identify potential issues with the mold or the plastic being processed.
In CNC machining centers, monitoring tool wear and vibrations can predict tool breakage or machine malfunctions. For metal cutting tools, monitoring vibration and acoustic emission can detect early signs of tool failure or material defects. Predictive maintenance based on condition monitoring can help manufacturers optimize production, minimize downtime, and enhance the quality of their products. For instance, in a metal stamping press, monitoring the vibration and sound patterns during operation can help detect early signs of tool wear, allowing for timely replacement and preventing costly breakdowns.
Comparison of Condition Monitoring Techniques for Different Equipment Types
Equipment Type | Vibration Analysis | Temperature Monitoring | Oil Analysis | Acoustic Emission | Other Techniques |
---|---|---|---|---|---|
Rotating Machinery (Pumps, Compressors) | High | Medium | High | Medium | Flow Monitoring |
Motors and Gearboxes | High | High | Medium | Low | MCSA |
Power Generation Equipment (Turbines, Generators) | High | High | High | Medium | Gas Analysis |
Manufacturing Machinery (Injection Molding, CNC) | Medium | Medium | Medium | Low | Pressure Monitoring |
This table provides a high-level overview of the suitability of different condition monitoring techniques for various equipment types. The specific techniques and their application will vary based on the equipment’s design, operating conditions, and potential failure modes.
Final Summary: Condition Monitoring Focuses On Safety Efficiency
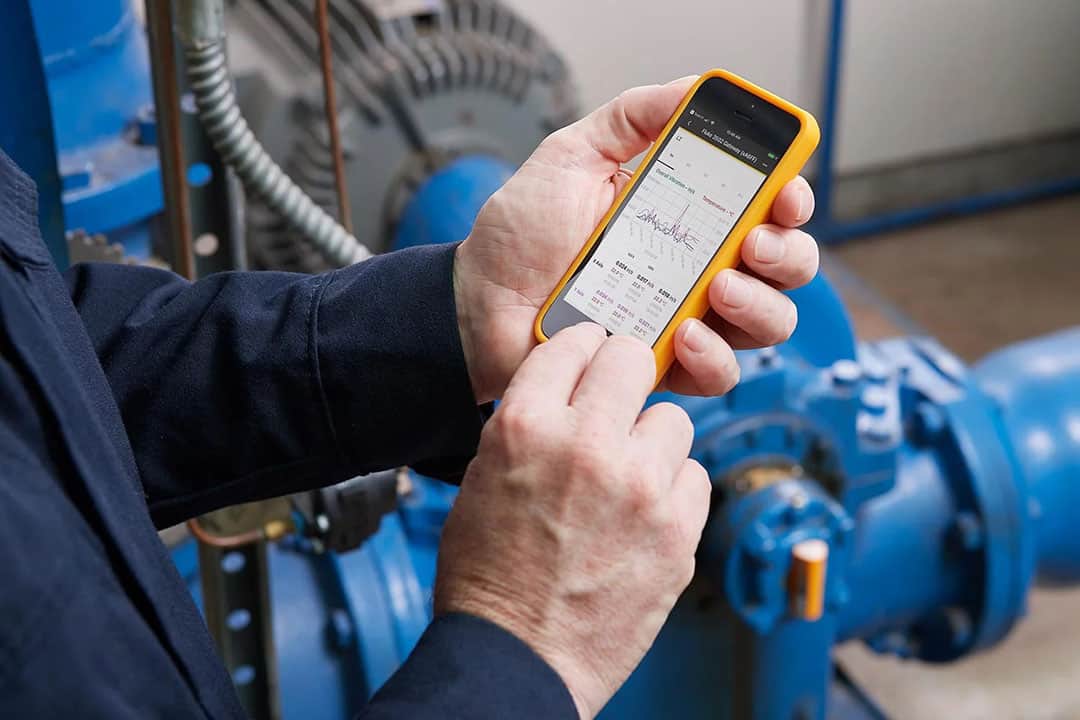
In conclusion, condition monitoring is a multifaceted approach to improving safety and efficiency in various industries. By integrating data analysis, predictive maintenance, and proactive strategies, organizations can optimize resource allocation, reduce downtime, and create a safer work environment. The future of condition monitoring looks bright, with emerging technologies like AI and IoT poised to further enhance its capabilities.
This comprehensive guide has provided a deep dive into the topic, offering valuable insights for anyone looking to implement condition monitoring in their operations.