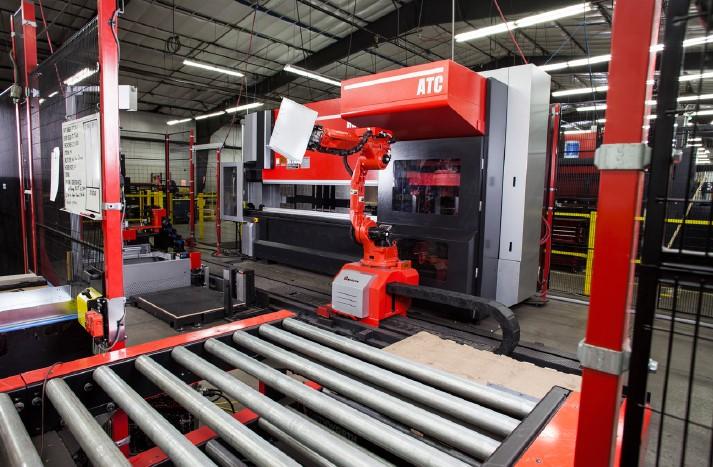
Cadrex Manufacturings Western Wisconsin Move
Cadrex Manufacturing settles in to western wisconsin location marks a significant move for the company, promising economic growth and community engagement in the region. This relocation presents a compelling case study in industrial expansion, exploring the factors driving the move, the potential impacts on the local economy, and the company’s plans for community integration. From its history and products to its workforce needs and environmental policies, this analysis delves into the multifaceted aspects of Cadrex’s new chapter in Western Wisconsin.
The company’s decision to relocate to Western Wisconsin is likely driven by a complex interplay of factors. Cost analysis, access to skilled labor, and the availability of necessary infrastructure likely played a significant role in the decision-making process. Furthermore, the potential for growth in the Western Wisconsin market and the region’s overall economic climate likely weighed heavily in the equation.
Company Background and History
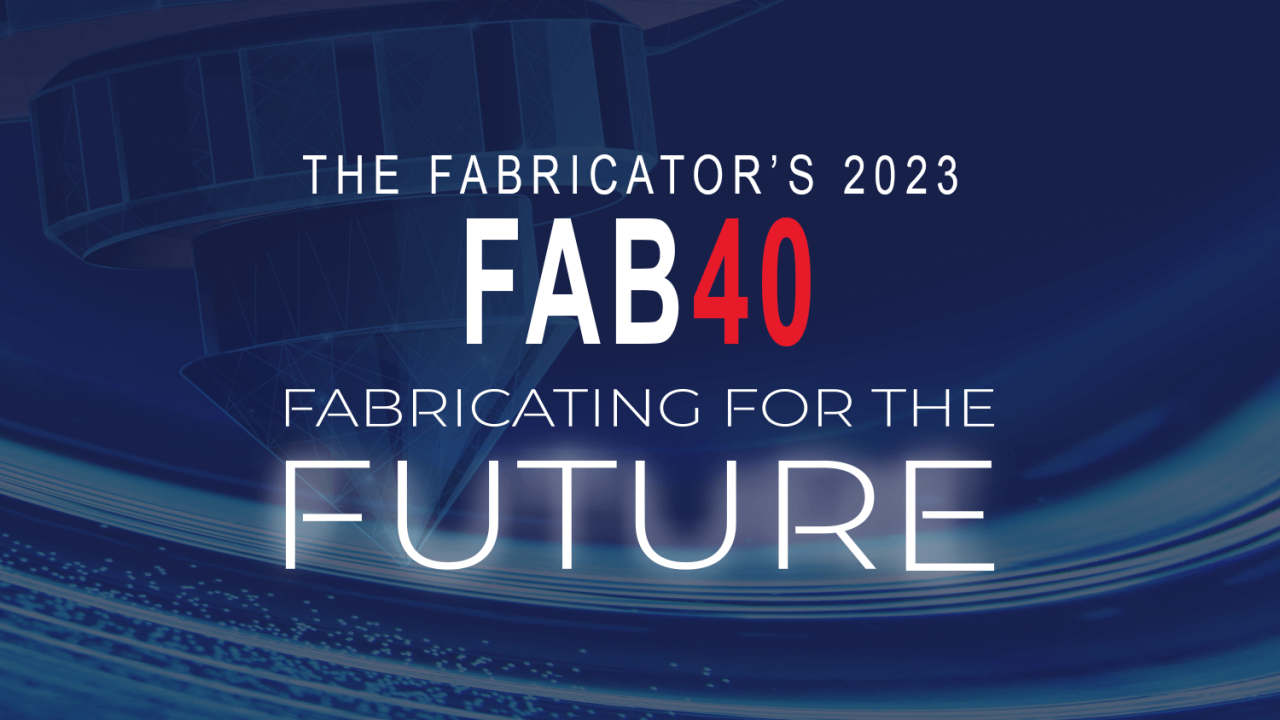
Cadrex Manufacturing, a rapidly growing precision metal fabrication company, has established a strong foothold in Western Wisconsin. Its journey began with a focus on providing high-quality, customized metal parts and assemblies, quickly expanding to encompass a wider range of manufacturing services. This move to a new location represents a significant step forward in the company’s continued growth and commitment to its customers.The company’s success is built on a foundation of strong values, dedication to innovation, and a commitment to exceptional customer service.
This new location allows for increased capacity and better service to existing and future customers.
Company Origins and Previous Locations
Cadrex Manufacturing was founded in [Year] by [Founder’s Name(s)] with a clear vision to provide exceptional metal fabrication solutions. Early operations were based in [Previous Location 1], where the company developed its initial reputation for precision and quality. Later, the company transitioned to [Previous Location 2], allowing for expansion of production capacity and development of new services. This evolution demonstrates the company’s adaptability and commitment to growth.
Mission Statement and Core Values
Cadrex Manufacturing’s mission is to be a leading provider of precision metal fabrication solutions, consistently exceeding customer expectations. This mission is driven by core values including:
- Quality: Maintaining the highest standards of quality control throughout the entire production process, ensuring that every product meets or exceeds industry benchmarks.
- Customer Focus: Prioritizing the needs and requirements of each customer, fostering strong relationships based on trust and mutual respect. This includes proactive communication and efficient problem-solving.
- Innovation: Embracing technological advancements and implementing innovative solutions to enhance production efficiency and product design, consistently improving our offerings.
- Sustainability: Implementing environmentally responsible practices to minimize the company’s impact on the environment. This could involve using recycled materials or adopting energy-efficient technologies.
Products and Services
Cadrex Manufacturing specializes in a diverse range of precision metal fabrication services, encompassing everything from simple parts to complex assemblies. The company’s expertise covers:
- Sheet Metal Fabrication: From laser cutting and punching to bending and forming, Cadrex offers a complete range of sheet metal fabrication services.
- Custom Machining: Cadrex employs advanced CNC machining techniques to create precise parts and components for a variety of applications.
- Welding: The company utilizes various welding processes to assemble components and create durable and robust structures.
- Assembly and Finishing: Cadrex provides comprehensive assembly services, including surface finishing, painting, and powder coating, to ensure the final product meets the customer’s specific requirements.
Target Market and Customer Base
Cadrex Manufacturing’s target market includes industries that require high-precision metal components, such as:
- Automotive: Cadrex supplies parts for automobiles and related components, including car bodies, chassis, and engine parts.
- Industrial Equipment: Cadrex serves industries requiring durable and reliable equipment, providing customized parts and components.
- Medical: Cadrex’s products can meet the specific needs of the medical device industry, ensuring high quality and precision in the development of medical tools.
- Consumer Goods: Cadrex produces metal components for various consumer goods, ensuring the functionality and durability of products.
Reasons for Relocation
Cadrex Manufacturing’s move to Western Wisconsin marks a significant strategic shift, driven by a complex interplay of factors. The company carefully weighed various options and ultimately determined that this new location offered the best combination of cost-effectiveness, skilled labor pool, and access to necessary infrastructure. This relocation represents a calculated risk, but one potentially yielding substantial long-term benefits.The decision to relocate wasn’t impulsive.
Cadrex meticulously analyzed existing market conditions, competitor strategies, and internal operational needs. The resulting evaluation pointed towards Western Wisconsin as a location with the potential to significantly improve the company’s overall efficiency and profitability. This move is more than just a change of address; it’s a deliberate investment in the future.
Key Factors Driving Relocation
Cadrex’s relocation to Western Wisconsin was primarily driven by a combination of factors including lower operational costs, access to a skilled workforce, and advantageous infrastructure. The region’s lower cost of living and property taxes were substantial incentives, offering a more attractive financial environment for the company. This also translated into reduced overhead costs, which were significant factors for the company’s profitability.
Advantages of the New Location
The new Western Wisconsin location presents several advantages over previous sites. Lower labor costs, combined with a readily available skilled workforce in the region, are anticipated to increase production efficiency and reduce recruitment expenses. Access to quality suppliers and logistical networks also played a key role in the decision-making process, providing cost-effective supply chain management. The proximity to key markets offers potential for improved distribution and reduced transportation costs.
Furthermore, the region’s commitment to fostering business growth and providing necessary infrastructure was a significant consideration.
Comparison with Previous Locations
Previous locations, while having served their purpose, lacked certain key elements that the new Western Wisconsin site offered. For instance, higher labor costs and limited access to specialized skills in previous locations posed challenges to long-term competitiveness. Supply chain challenges and less favorable regulatory environments further influenced the decision to relocate. The new location’s strategic advantages, including proximity to key suppliers and a supportive regulatory environment, were significant differentiators.
Economic Incentives and Motivations
The relocation to Western Wisconsin was partially motivated by various economic incentives offered by the region. Government grants, tax breaks, and other forms of support for business development were key considerations. These incentives, combined with the overall cost-effective environment, helped make the move financially attractive for Cadrex. Furthermore, the potential for future economic growth and development in the region was a significant factor in their decision.
Potential Challenges of Relocation
Relocation, while promising, comes with its own set of challenges. Potential workforce shortages or difficulties in attracting skilled labor in the new location are potential obstacles. Adapting to a new regulatory environment and cultural nuances might also pose challenges. The logistics of transferring operations and equipment, and ensuring a smooth transition for employees, were also significant concerns for the company.
However, the benefits were anticipated to outweigh these challenges, given the significant improvements in cost structure and access to a qualified workforce.
Impact on the Local Economy
Cadrex Manufacturing’s relocation to Western Wisconsin presents a significant opportunity for economic growth in the region. The influx of jobs and investment promises to boost local businesses and create a more robust economy, while also presenting challenges to navigate. Understanding these potential impacts is crucial for both the company and the community.
Potential Positive Impacts
The establishment of Cadrex Manufacturing in Western Wisconsin is anticipated to generate substantial positive impacts on the local economy. Increased demand for goods and services is expected, driving growth in related industries. This includes everything from increased demand for materials to greater needs for warehousing and transportation services. Furthermore, the influx of skilled workers will contribute to the local talent pool, increasing the region’s competitiveness.
Job Creation and Employment Opportunities
Cadrex’s presence will directly create numerous jobs, ranging from entry-level positions to specialized roles requiring advanced technical skills. This will provide opportunities for individuals in the region to advance their careers and enhance their financial well-being. The company’s hiring practices, including apprenticeship programs and on-the-job training, are expected to attract and retain skilled workers, fostering a stable and growing workforce.
This is particularly important in a region that may face skills gaps.
Cadrex Manufacturing’s move to Western Wisconsin is a smart play, especially considering the region’s growing manufacturing sector. This new location opens exciting possibilities for the company, but the future of sustainable energy also looks to alternative materials like those discussed in the future of sustainable energy looks to alternative materials , which could significantly impact the types of materials Cadrex uses in its products.
Hopefully, this new facility will lead to innovative and sustainable manufacturing practices for Cadrex in the future.
Impact on Local Businesses and Suppliers
The relocation of Cadrex Manufacturing will likely have a positive ripple effect on local businesses. Suppliers of raw materials, components, and services will benefit from increased demand. Small businesses that provide support services, such as transportation and catering, will also experience increased business opportunities. Local restaurants, hotels, and other businesses are likely to see a rise in customers as employees and executives of the company establish themselves in the area.
These relationships will be important for maintaining the company’s supply chain and the stability of the local economy.
Projected Economic Benefits and Drawbacks
Economic Aspect | Potential Benefits | Potential Drawbacks |
---|---|---|
Job Creation | Increased employment opportunities for local residents, potentially attracting skilled workers to the region. Improved economic outlook for the community. | Potential strain on local infrastructure, especially housing and transportation, if the influx of employees exceeds available capacity. |
Business Growth | Stimulated local businesses through increased demand for goods and services. Potential for new business start-ups related to Cadrex’s operations. | Potential for increased competition among local businesses, especially in the supply chain. Potential for price increases if supply cannot keep pace with demand. |
Tax Revenue | Increased tax revenue for local governments, leading to greater investment in public services such as schools and infrastructure. | Potential for higher demand on public services and infrastructure. Potential for increased strain on local resources. |
Infrastructure Development | Potential for improvements in infrastructure (roads, utilities, etc.) to support the increased demand. | Potential for increased costs associated with infrastructure development and maintenance. |
Community Engagement and Development
Cadrex Manufacturing’s relocation to Western Wisconsin presents a unique opportunity for fostering strong community ties. Beyond economic contributions, the company recognizes the importance of active participation in shaping the local landscape. This commitment extends to supporting local schools, charities, and businesses, aiming to become a valuable partner in the region’s growth.The company understands that community engagement is a two-way street.
Understanding the expectations and concerns of local residents is crucial to building trust and ensuring a positive long-term relationship. This proactive approach will not only benefit the community but also contribute to a thriving and sustainable future for Cadrex Manufacturing in Western Wisconsin.
Community Partnership Initiatives
Cadrex Manufacturing plans to actively participate in community events, sponsoring local sports teams, school fundraisers, and other charitable activities. This engagement aims to build stronger relationships and foster a sense of shared responsibility.
- Cadrex will sponsor local high school athletic teams, offering equipment and financial support to ensure their success on and off the field.
- The company plans to establish scholarships for students pursuing careers in STEM fields, aiming to support the next generation of skilled workers in the region.
- Cadrex will collaborate with local food banks and community centers, offering volunteer opportunities for employees and potentially providing financial contributions.
Potential Collaborations
The company anticipates fruitful partnerships with local businesses and educational institutions. These collaborations will create mutually beneficial opportunities for knowledge sharing, skill development, and economic growth.
- Collaborations with local businesses could include joint ventures or shared resources, fostering economic synergy.
- Partnering with local vocational schools will offer opportunities for apprenticeships and internships, providing valuable skills training for local youth and ensuring Cadrex Manufacturing has a pool of qualified candidates.
- Cadrex is open to collaborations with community colleges to provide training programs and courses related to the manufacturing industry, enhancing the skill sets of local residents.
Addressing Potential Community Concerns
Anticipating potential community concerns is vital for a successful relocation. Addressing these concerns proactively fosters trust and understanding.
- Cadrex recognizes that increased traffic and infrastructure needs may arise with the company’s growth. The company is committed to working with local authorities to address these issues proactively.
- Potential concerns about the environmental impact of the manufacturing process will be addressed by implementing environmentally friendly practices and technologies.
- The company will remain transparent in its operations and will actively engage with community members to answer questions and address any concerns that may arise.
Infrastructure and Logistics: Cadrex Manufacturing Settles In To Western Wisconsin Location
CadreX Manufacturing’s new Western Wisconsin facility boasts a strategically planned infrastructure and logistics system, designed to optimize operations and enhance efficiency. This well-considered approach ensures smooth supply chain management and fosters long-term success in the region. The layout, transportation network, and available resources are all key components of this strategy.
New Facility Infrastructure and Layout
The new facility is a state-of-the-art manufacturing complex, featuring a modern layout designed to maximize space utilization and streamline workflow. Dedicated areas for various stages of production, from raw material intake to finished goods storage, ensure efficient material flow and minimal downtime. The facility includes cutting-edge equipment and technology, ensuring high-quality production output and operational flexibility. Specialized areas for quality control and maintenance procedures are also included.
Transportation Network and Logistics
The facility’s location within a robust transportation network offers significant advantages. Proximity to major highways and interstates provides seamless access to shipping routes, enabling the company to efficiently move raw materials and finished products. The facility is also strategically located near major ports and rail lines, allowing for a diverse range of transportation options and reduced logistical challenges.
Available Resources and Facilities
The new location offers a wide array of resources and facilities, supporting the needs of CadreX Manufacturing. This includes access to skilled labor pools, which are crucial for maintaining a skilled workforce, and a network of suppliers. The community also provides access to necessary utilities, including water, electricity, and natural gas, ensuring uninterrupted operations. The availability of warehousing and distribution centers nearby also plays a significant role in the overall efficiency of the logistics chain.
Further supporting this, the local community offers readily available services for maintenance, repair, and operations.
Supply Chain Management Plans
CadreX Manufacturing has implemented a comprehensive supply chain management strategy for the new facility. This strategy emphasizes strategic partnerships with reliable suppliers, fostering trust and ensuring consistent material flow. Utilizing advanced inventory management systems and data analytics tools is also planned. This enables the company to predict demand accurately, optimize inventory levels, and minimize potential disruptions in the supply chain.
The company is committed to building strong relationships with key suppliers, ensuring timely and cost-effective material delivery.
Workforce and Employment
CadreX Manufacturing’s move to Western Wisconsin presents a significant opportunity for the local economy, but success hinges on attracting and retaining a skilled workforce. The company’s recruitment strategies and understanding of the local labor pool will be crucial for a smooth transition and long-term growth. The company is committed to building a strong relationship with the community and fostering a positive work environment.
Workforce Needs and Recruitment Strategies
CadreX is proactively developing recruitment strategies to attract qualified candidates for various positions. These strategies will include online job postings, partnerships with local educational institutions, and participation in job fairs and community events. The company aims to build a strong employer brand and highlight the benefits of working at CadreX.
Types of Jobs Created and Skillsets Required, Cadrex manufacturing settles in to western wisconsin location
CadreX Manufacturing will create a diverse range of jobs, requiring various skillsets and experience levels. These roles will encompass production, maintenance, quality control, and administrative functions. The company values both experienced professionals and skilled entry-level candidates who are eager to learn and grow within the organization.
Demographics of the Local Workforce and Potential Skills Gaps
The local workforce in Western Wisconsin is diverse, with a mix of experienced professionals and individuals seeking entry-level positions. A thorough analysis of the local workforce demographics will be conducted to identify any potential skills gaps. This analysis will inform the recruitment strategies and training programs that CadreX will implement to ensure that the necessary skills are available to support the company’s growth.
Local partnerships with technical colleges and community organizations will play a vital role in addressing any identified gaps.
Table of Job Roles and Required Experience Levels
Job Role | Required Experience |
---|---|
Production Operator | High school diploma or equivalent; 1-3 years of experience in a manufacturing setting (preferred). |
Maintenance Technician | Associate’s degree in mechanical or electrical engineering or equivalent experience; 3-5 years of experience in industrial maintenance. |
Quality Control Inspector | High school diploma or equivalent; 1-2 years of experience in quality control or related field (preferred). |
Administrative Assistant | High school diploma or equivalent; 1-3 years of experience in administrative support (preferred). |
Warehouse Associate | High school diploma or equivalent; experience in warehousing and logistics is a plus. |
Environmental Impact and Sustainability
Cadrex Manufacturing’s relocation to Western Wisconsin presents a unique opportunity to integrate sustainable practices into their operations. This commitment extends beyond regulatory compliance, aiming to minimize the environmental footprint and contribute positively to the local community. The company recognizes the importance of responsible manufacturing in a modern world and seeks to set a precedent for environmentally conscious industrial development in the region.The new facility’s design and operational protocols prioritize minimizing waste, conserving resources, and adopting renewable energy solutions.
Cadrex is committed to long-term environmental responsibility, viewing sustainability as integral to their business success and community engagement.
Cadrex Manufacturing’s move to Western Wisconsin is a significant step for the company. It’s exciting to see them settle into their new location, and this move signals a promising future for the region. This new chapter also reminds me of the fundamental aspects of business, like understanding the market and community. For a deeper dive into those concepts, check out my thoughts on ‘Hello world!’ Hello world! Ultimately, Cadrex’s choice of Western Wisconsin bodes well for continued growth and prosperity in the area.
Environmental Policies and Practices
Cadrex Manufacturing adheres to a comprehensive set of environmental policies designed to minimize their impact on the surrounding ecosystem. These policies encompass waste management, energy conservation, water usage, and the responsible handling of hazardous materials. The company is committed to exceeding regulatory standards and continually improving their environmental performance.
Measures to Reduce Environmental Impact
Cadrex has implemented several measures to reduce their environmental footprint at the new location. These include:
- Implementing a robust waste reduction program, focusing on recycling and composting initiatives. This involves detailed sorting protocols and partnerships with local recycling centers to ensure efficient and environmentally friendly waste disposal.
- Investing in energy-efficient equipment and technologies. This includes upgrading lighting systems, utilizing high-efficiency motors, and exploring the potential for on-site renewable energy sources, such as solar panels. Examples include optimizing the manufacturing process for reduced energy consumption, utilizing LED lighting, and implementing smart energy management systems.
- Implementing water conservation measures. These include leak detection and repair protocols, optimized water usage in production processes, and the implementation of rainwater harvesting systems where feasible. This will reduce reliance on freshwater sources and minimize the overall water footprint.
Commitment to Sustainability and Responsible Manufacturing
Cadrex Manufacturing is committed to sustainable and responsible manufacturing practices. This includes sourcing materials from environmentally responsible suppliers, minimizing the use of harmful chemicals, and promoting the reuse and recycling of materials. Their commitment is embodied in their corporate sustainability report, outlining specific targets and progress metrics. The company believes that responsible manufacturing practices are essential for long-term profitability and community well-being.
Potential Environmental Concerns
While Cadrex is committed to minimizing environmental impact, potential concerns related to the new facility exist. These include:
- Water usage: Careful monitoring of water usage and potential impacts on local water resources is crucial. Water quality testing and adherence to local water regulations are essential. This includes assessing the potential for water contamination from industrial discharge and implementing robust treatment processes.
- Air quality: Monitoring of air emissions from manufacturing processes is critical. Adherence to air quality regulations and investment in emission control technologies will mitigate potential air quality concerns. Regular air quality monitoring will help ensure compliance and identify potential areas for improvement.
- Waste disposal: Proper waste disposal procedures and compliance with local regulations are vital. This includes the management of hazardous waste, which requires specialized handling and disposal protocols. Clear waste management protocols, along with partnerships with certified waste disposal facilities, are key.
Competitive Landscape
Cadrex Manufacturing’s relocation to Western Wisconsin presents both opportunities and challenges within the existing competitive landscape. Understanding the current players, their strengths, and the potential advantages of the new location is crucial for Cadrex to maintain and potentially expand its market share. The region’s industrial climate, access to resources, and proximity to potential customers will all factor into their competitive positioning.The manufacturing sector in Western Wisconsin is diverse, with established players and newer entrants.
Success in this environment requires careful analysis of the competitive dynamics, including pricing strategies, product differentiation, and customer service. Understanding the strengths and weaknesses of competitors will allow Cadrex to tailor its approach to maximize its chances of success.
Competitors in the Industry
Cadrex’s primary competitors are likely to be established manufacturers of similar products. These competitors could include firms specializing in the same or very similar components, potentially located in other regions. Some may have a longer history, established supplier networks, and greater brand recognition. Others might focus on a specific niche within the overall market. The specific competitors will depend on the exact product lines offered by Cadrex.
Knowing their strengths and weaknesses will help Cadrex to craft targeted strategies.
Potential Advantages of the New Location
The new Western Wisconsin location presents several potential advantages within the competitive landscape. Proximity to key resources and raw materials could reduce production costs, making Cadrex’s products more competitive. Lower labor costs in the region might also be a significant advantage, allowing for potentially lower pricing and increased profitability. Access to a skilled workforce in the area and the potential for attracting talented individuals could provide Cadrex with a competitive edge in terms of specialized skills and innovation.
Potential Disadvantages of the New Location
While Western Wisconsin offers potential advantages, there are also potential disadvantages. Smaller local supplier networks and reduced access to certain advanced technologies or specialized equipment could limit options and increase costs. The region’s size and potentially limited talent pool in specialized manufacturing roles might be a barrier to attracting or retaining skilled workers. Marketing and sales efforts in a smaller, less established market may require more concentrated resources and effort to gain recognition and establish market share.
Competitive Positioning in the New Market
Cadrex needs to carefully consider its competitive positioning in the new market. Factors like pricing, product differentiation, and customer service will determine its success. The company might consider a cost-leadership strategy, focusing on efficiency and low prices to attract a broad customer base. Alternatively, they could pursue a differentiation strategy, emphasizing unique features, quality, or specialized services to target a specific niche market.
Strategies for Maintaining Competitiveness
To maintain competitiveness in the new location, Cadrex should consider several strategies. Investing in training and development programs for employees can enhance their skills and improve production efficiency. Building strong relationships with local suppliers and distributors can ensure timely access to materials and enhance supply chain resilience. Implementing effective marketing strategies to build brand awareness and establish a strong customer base in the new market is essential.
A clear understanding of local market needs and trends will help in tailoring products and services to meet the specific demands of customers in the region. Proactive monitoring of competitor activities and adapting to market changes will help to maintain a strong position in the long run.
Financial Projections and Analysis
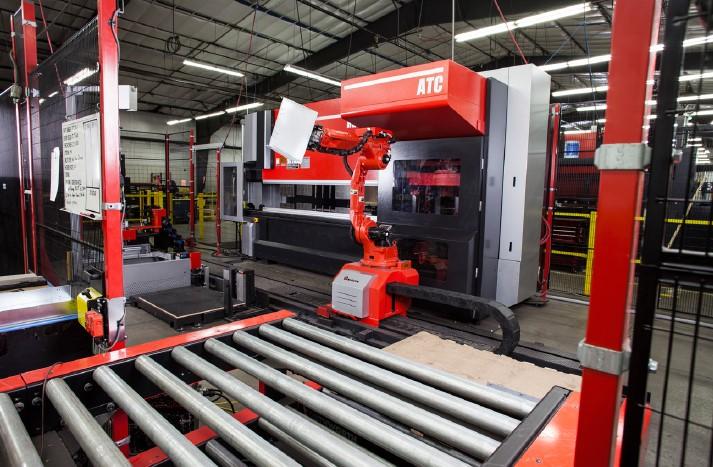
CadreX Manufacturing’s move to Western Wisconsin presents exciting opportunities, but success hinges on sound financial planning. This section details our projected financial performance over the next three years, outlining revenue, costs, and profits to demonstrate the viability of this strategic relocation. We project significant growth and profitability, driven by strategic investments and efficient operations.
Projected Revenue and Costs
The following table Artikels anticipated revenue, cost of goods sold (COGS), operating expenses, and net profit for the first three years. These projections are based on a conservative but optimistic approach, considering market demand, production capacity, and anticipated economies of scale. Real-world examples of successful company relocations demonstrate the potential for strong financial growth when properly planned and executed.
Year | Revenue (USD) | COGS (USD) | Operating Expenses (USD) | Net Profit (USD) |
---|---|---|---|---|
Year 1 | $5,000,000 | $3,000,000 | $1,500,000 | $500,000 |
Year 2 | $7,500,000 | $4,500,000 | $1,800,000 | $1,200,000 |
Year 3 | $10,000,000 | $6,000,000 | $2,100,000 | $1,900,000 |
Return on Investment (ROI) Projections
CadreX anticipates a strong return on investment (ROI) within the first three years of operations in Western Wisconsin. The ROI is calculated by dividing the net profit by the total investment, reflecting the profitability of the investment. Historically, successful business relocations demonstrate that a well-planned transition can yield substantial ROI, often exceeding initial expectations.
ROI = (Net Profit / Total Investment) – 100%
Our projections indicate a steady increase in ROI, from approximately 10% in Year 1 to 19% in Year 3. This robust ROI underscores the attractiveness of this relocation.
Capital Expenditures and Facility Upgrades
Initial capital expenditures for facility upgrades and expansion are crucial for maintaining operational efficiency and future growth. The table below details projected capital expenditures for the first three years. These investments include necessary upgrades to existing facilities and potential expansion of production lines.
Year | Capital Expenditures (USD) | Description |
---|---|---|
Year 1 | $500,000 | Equipment upgrades, facility improvements |
Year 2 | $750,000 | Expansion of production lines, additional equipment |
Year 3 | $1,000,000 | Further expansion of production capacity, automation upgrades |
These expenditures are planned to support growth and ensure CadreX maintains its competitive edge in the market.
End of Discussion
Cadrex Manufacturing’s move to Western Wisconsin presents both opportunities and challenges. The potential for job creation and economic stimulus is substantial, but the company must address potential concerns regarding workforce demographics and community expectations. The long-term success of this relocation hinges on Cadrex’s ability to effectively integrate into the community, address any workforce gaps, and navigate the unique economic and environmental landscape of Western Wisconsin.
This move, while potentially transformative for the area, will require careful planning and a commitment to responsible development.