
Green Bay Fabrication Innovation & Growth
Green Bay based fabrication shop fosters innovative growth, showcasing a blend of traditional metalworking and cutting-edge techniques. This exploration delves into the strategies behind success for these shops, examining everything from market trends to innovative fabrication methods, and highlighting the crucial role of technology and community engagement in their journey.
From understanding the specific needs of the Green Bay market to exploring the potential of sustainable practices, this deep dive into the world of fabrication shops provides a comprehensive view of the factors that contribute to both short-term and long-term success. We’ll also touch on financial considerations and growth strategies to paint a clear picture of what it takes to thrive in this dynamic industry.
Introduction to Green Bay Fabrication Shop
A Green Bay-based fabrication shop is a business specializing in the creation of custom metal and other materials. These shops typically serve a diverse range of clients, from local businesses to national corporations, providing a range of services that involve design, fabrication, and assembly. These shops play a crucial role in the local economy, often contributing to the development of various industries.These shops are characterized by their ability to transform raw materials into intricate and durable products.
They often work with metals like steel, aluminum, and copper, as well as other materials like wood, plastics, and composites. They may also provide specialized services like welding, cutting, forming, and finishing. The skilled workforce in these shops is essential to the success of the enterprise, and a high degree of craftsmanship is generally expected.
Typical Services Offered
Green Bay fabrication shops typically offer a range of services tailored to their clientele. These services often include, but are not limited to, metal fabrication, custom design and engineering, fabrication and assembly of equipment and parts, and specialized finishing processes. The scope of work can be varied, from simple repairs and modifications to complex, large-scale projects.
Business Environment in Green Bay
The business environment in Green Bay, Wisconsin, is a key factor in the success of a fabrication shop. The presence of various industries, including manufacturing, agriculture, and construction, creates a demand for the services of such shops. Green Bay’s proximity to other Midwest markets and its well-established supply chains also provide access to resources and labor. The area’s reputation for strong community ties can be a valuable asset, potentially leading to a robust network of clients and suppliers.
Examples of Successful Fabrication Shops in Similar Locations
Several successful fabrication shops in similar locations across the Midwest and the United States provide valuable insights into the strengths of such enterprises. Their success is often attributable to a combination of factors, including a strong reputation for quality, specialized expertise, a capable workforce, and effective marketing strategies. The ability to adapt to changing market demands and client needs is also critical.
Table of Successful Fabrication Shops
Shop Name | Location | Speciality | Year Founded |
---|---|---|---|
Midwest Metal Works | Milwaukee, WI | Custom metal fabrication, specializing in agricultural equipment | 1985 |
Precision Engineering Solutions | Madison, WI | High-precision machining and metal fabrication | 2005 |
Superior Fabrication Inc. | Chicago, IL | Industrial equipment fabrication and repair | 1992 |
Northwoods Welding & Fabrication | Wausau, WI | Welding, metal fabrication, custom metalwork | 2010 |
Innovative Growth Strategies
A fabrication shop’s ability to adapt and innovate is key to its long-term success. Staying competitive requires a proactive approach to embracing new technologies, materials, and processes. This involves more than just incremental improvements; it demands a culture that values experimentation, learning, and the development of unique solutions.
This approach fosters a dynamic environment where employees feel empowered to contribute ideas and develop new skills. By analyzing best practices from other industries, we can identify opportunities for innovation and apply them effectively within the fabrication sector. This can lead to the development of cutting-edge products and services, ultimately driving growth and profitability.
Product Development Approaches
Modern fabrication shops must adapt their product development strategies to stay competitive. This includes a focus on new materials and technologies. For example, using 3D printing for prototyping or advanced composites for stronger, lighter parts, are both examples of innovative approaches to product development.
Innovative Fabrication Techniques, Green bay based fabrication shop fosters innovative growth
Exploring new fabrication techniques and processes is crucial for a fabrication shop’s continued success. This includes exploring methods like laser cutting, waterjet cutting, robotic welding, and advanced machining techniques. Staying informed about emerging technologies and trends in manufacturing will be critical to future growth.
- Additive Manufacturing (3D Printing): 3D printing offers the ability to create complex geometries and customized parts rapidly, reducing lead times and improving design flexibility. Examples include creating custom jigs and fixtures or producing intricate prototypes for testing.
- Advanced Composites: Incorporating advanced composite materials can enhance product strength and reduce weight. This is particularly useful in aerospace, automotive, and construction applications.
- Precision Machining Techniques: Employing advanced machining techniques like CNC machining with specialized tools and materials can increase the precision and accuracy of fabricated parts.
- Laser Cutting and Waterjet Cutting: These technologies provide high precision cutting capabilities for various materials. These methods are well-suited for intricate designs and complex shapes.
Employee Training and Development for Innovation
A skilled and adaptable workforce is essential for a fabrication shop’s innovation. Training programs focused on new technologies and processes are crucial for employee development. This can include hands-on workshops, online courses, and mentorship programs that encourage creativity and problem-solving.
Comparison with Other Industries
Analyzing innovative approaches in other industries can provide valuable insights for fabrication shops. The automotive industry, for example, often uses simulation software and virtual prototyping to optimize designs. Adopting similar methodologies can improve the efficiency and effectiveness of fabrication processes.
Potential Innovative Fabrication Techniques or Processes
Several innovative fabrication techniques are emerging and show potential for significant improvement in the fabrication industry. These include the use of advanced sensors for real-time quality control, automation for more complex processes, and data analytics for process optimization. The integration of these technologies will enhance efficiency and product quality.
- Automated Quality Control: Implementing automated quality control systems using sensors and AI to monitor the fabrication process in real-time.
- Data-Driven Process Optimization: Utilizing data analytics to identify inefficiencies in fabrication processes and implement solutions for improvement.
- Advanced Simulation Techniques: Integrating advanced simulation software for design optimization and process planning, allowing for more accurate predictions and efficient prototyping.
Fabrication Methods Comparison
Fabrication Method | Advantages | Disadvantages |
---|---|---|
CNC Machining | High precision, repeatability, versatility, suitable for complex geometries | Can be expensive, limited material types |
Laser Cutting | High speed, precision cutting, suitable for various materials, intricate designs | Can be expensive, limited material thickness |
Waterjet Cutting | High precision, versatile, can cut various materials, high speed | Can be expensive, limited material thickness |
Robotic Welding | High speed, precision, repeatability, reduces human error, suitable for large-scale production | High initial investment, requires specialized programming and maintenance |
Market Analysis and Customer Base
Understanding your target audience and the current market landscape is crucial for a fabrication shop’s success. This analysis helps tailor marketing strategies, identify growth opportunities, and ultimately, attract more clients. A deep dive into the fabrication industry’s trends and competitive landscape will inform decisions regarding product development, pricing, and customer service.A successful fabrication shop in Green Bay needs a keen understanding of its local market.
Knowing who your ideal customers are, what their needs are, and how to effectively communicate your value proposition is paramount. The market is not monolithic; segmentation is key to crafting targeted campaigns that resonate with specific customer groups.
Target Customer Base
The target customer base for a Green Bay fabrication shop encompasses a wide range of industries, from construction and manufacturing to agriculture and even local businesses needing custom metalwork. Identifying specific niches within these broader sectors is essential. For example, a construction-focused segment might require specialized equipment and faster turnaround times than a farm equipment segment. Understanding the unique demands of each niche allows for tailoring of services and marketing materials.
Current Market Trends in Fabrication
The fabrication industry is constantly evolving, driven by advancements in materials, technology, and customer expectations. Current trends include a greater emphasis on sustainability, with customers seeking environmentally friendly materials and processes. Precision and speed are also high priorities, leading to an increased demand for automated and digital fabrication techniques. The use of 3D printing and CNC machining is becoming more prevalent, allowing for more complex and intricate designs.
Successful Marketing Campaigns for Fabrication Shops
Successful marketing campaigns for fabrication shops often leverage a combination of digital and traditional strategies. Online presence, including a user-friendly website with detailed product portfolios and client testimonials, is vital. Social media platforms can be effective for showcasing projects, engaging with potential clients, and building a brand reputation. Networking events, trade shows, and local partnerships can provide opportunities for direct interaction with potential customers.
That Green Bay fabrication shop is really pushing the boundaries of innovation, and it’s clear they’re onto something special. But to truly thrive, a company needs to connect with its audience on a deeper level. Like, authenticity is essential to brand building, a key ingredient in creating a lasting impact here’s why. Ultimately, this focus on genuine values will be what propels their innovative growth even further.
A well-executed referral program can also significantly expand your customer base. Examples include highlighting case studies and showcasing project successes.
Strategies for Attracting New Clients in the Area
Attracting new clients in Green Bay requires a multi-pronged approach. Local business partnerships, especially with construction firms and contractors, are crucial for building relationships and securing consistent work. Participation in local events and trade shows, where potential customers can directly interact with the shop, can also yield promising results. Offering competitive pricing, fast turnaround times, and excellent customer service are essential for standing out in the marketplace.
Demonstrating expertise in a specific niche, like agricultural fabrication or heavy-duty construction, can make the shop a clear choice for particular needs.
Segmenting the Market for a Fabrication Shop
Segmentation allows for a more focused and effective approach to marketing and service delivery. By dividing the market into distinct groups based on shared characteristics, a fabrication shop can tailor its offerings to meet the unique needs of each segment. This targeted approach improves efficiency and allows for better resource allocation. The table below illustrates a possible segmentation strategy.
Market Segment | Characteristics | Key Needs |
---|---|---|
Construction | Large-scale projects, demanding fast turnaround times, need for heavy-duty materials | Reliability, speed, high-quality materials |
Agriculture | Custom designs, durable materials, potentially seasonal demand | Durability, customizability, reliability in harsh conditions |
Manufacturing | Precise components, high volumes, potentially ongoing relationships | Accuracy, efficiency, long-term partnership |
Local Businesses | Custom metalwork, smaller projects, diverse applications | Unique designs, responsiveness, personalized service |
Operational Excellence and Efficiency
Operational excellence isn’t just about maximizing output; it’s about optimizing the entire process. A fabrication shop that prioritizes operational efficiency gains a competitive edge by reducing waste, streamlining workflows, and improving quality. This, in turn, fosters a culture of innovation, allowing the shop to adapt quickly to changing market demands and customer needs. By consistently improving processes, a fabrication shop can drive innovation and ensure long-term success.Operational efficiency directly impacts innovation.
Green Bay’s fabrication scene is buzzing with innovation. Local shops are pushing boundaries, and this growth is a testament to the region’s skilled workforce. Meanwhile, Oshkosh is also experiencing a surge in development, with exciting projects like oshkosh eyes new development near fox river happening near the Fox River. This demonstrates a broader trend of economic activity in the area, further supporting the continued success of Green Bay’s innovative fabrication shops.
A leaner, more efficient operation frees up resources and time, enabling the shop to explore new technologies, materials, and processes. This focus on optimization can lead to the development of innovative solutions and products tailored to specific customer requirements. A smooth workflow translates into a more agile and adaptable business, ready to embrace new ideas and implement them effectively.
Lean Manufacturing Principles
Lean manufacturing principles are essential for streamlining operations in a fabrication shop. These principles focus on eliminating waste, optimizing processes, and improving quality. Key elements include:
- Waste Reduction: Identifying and eliminating waste in all forms (transportation, inventory, motion, waiting, overproduction, overprocessing, defects) is crucial for efficiency. Examples in fabrication shops include reducing material handling steps, minimizing unnecessary inventory, and optimizing machine setup times. By streamlining the production flow and removing unnecessary steps, the shop can decrease the time spent on non-value-added activities, ultimately boosting productivity.
That Green Bay fabrication shop, pushing boundaries with innovative designs, is a prime example of entrepreneurial success. Thinking about the future, it’s crucial to understand the process of selling a business, and five tips for selling a business can offer valuable insights. Ultimately, this kind of forward-thinking approach in Green Bay is exactly what fuels economic growth and innovation.
- Continuous Improvement: Regularly evaluating and improving processes through data analysis and feedback loops is vital for maintaining efficiency. This can include analyzing production data, gathering employee feedback, and identifying areas for optimization. A fabrication shop that embraces continuous improvement can proactively address inefficiencies and bottlenecks, resulting in better quality products and faster turnaround times.
- Value Stream Mapping: Visualizing the entire value stream (from raw materials to finished product) helps identify bottlenecks and areas for improvement. By mapping the process flow, fabrication shops can pinpoint steps that add no value and identify opportunities for optimization. For instance, a fabrication shop could discover that a particular part of the process involves unnecessary handling, leading to rework or delays.
Value stream mapping would expose this inefficiency and enable the shop to streamline the process.
Quality Control in Fabrication
Maintaining high quality in fabrication processes is paramount. A robust quality control system ensures consistency, minimizes defects, and ultimately satisfies customer expectations. This involves:
- Implementing rigorous inspection procedures: Regular inspections at various stages of the fabrication process are essential to identify and correct defects early on. This could involve visual inspections, dimensional measurements, or material testing. Early defect detection prevents costly rework and ensures products meet the required specifications.
- Utilizing quality control tools: Statistical process control (SPC) charts and other tools can help monitor and analyze process variations, allowing for proactive identification and correction of issues. By tracking key metrics, fabrication shops can identify patterns and trends that indicate potential problems before they escalate. For instance, using SPC charts to track the thickness of sheet metal parts can reveal inconsistencies that would otherwise go unnoticed.
- Employing trained personnel: Investing in training for personnel involved in quality control ensures they have the necessary skills and knowledge to identify and address quality issues effectively. This approach ensures that the fabrication shop’s workforce is capable of maintaining high standards of quality and consistency in all aspects of their work.
Supply Chain Optimization
Optimizing the fabrication shop’s supply chain is critical for efficiency and cost savings. This includes:
- Supplier Relationship Management: Developing strong relationships with reliable suppliers ensures a consistent flow of quality materials and timely delivery. This may include negotiating better pricing or securing exclusive deals, fostering a collaborative environment with suppliers.
- Inventory Management: Efficient inventory management minimizes storage costs and reduces the risk of obsolescence. This involves forecasting demand accurately, managing material levels, and implementing just-in-time inventory systems.
- Logistics Optimization: Streamlining transportation and delivery processes can reduce lead times and shipping costs. This could involve using optimized routes, leveraging technology for real-time tracking, and negotiating favorable shipping rates.
Manufacturing Process Comparison
The choice of manufacturing process significantly impacts a fabrication shop’s efficiency and cost-effectiveness. The following table compares common processes:
Manufacturing Process | Description | Advantages | Disadvantages |
---|---|---|---|
Laser Cutting | Precise cutting of materials using a laser beam. | High precision, minimal material waste, fast cutting speed. | High initial investment in laser equipment, potentially limited material types. |
Plasma Cutting | Cutting materials using a high-velocity jet of ionized gas. | High cutting speed, capable of cutting thicker materials. | Higher potential for material distortion, requires skilled operators. |
CNC Machining | Automated machining of parts using computer-controlled machines. | High precision, complex part production. | High initial investment, limited flexibility for non-standard parts. |
Welding | Joining metal parts using heat and pressure. | Strong and durable joints, suitable for various metal types. | Potential for weld defects, requires skilled welders. |
Technology Integration and Modernization

Staying competitive in the fabrication industry demands embracing technological advancements. Integrating these innovations into existing workflows not only boosts efficiency but also unlocks new possibilities for creativity and precision. This shift allows for quicker turnaround times, improved accuracy, and a greater capacity to handle complex projects.Modern fabrication shops are recognizing the crucial role technology plays in shaping their future.
By proactively integrating various technological tools and strategies, these shops can significantly enhance their operational efficiency, reduce errors, and improve overall output.
Software and Tools for Fabrication
Modern fabrication shops rely on a variety of software and tools to streamline their processes and improve quality control. CAD (Computer-Aided Design) software is essential for creating detailed 2D and 3D models of components. CAM (Computer-Aided Manufacturing) software translates these designs into instructions for CNC (Computer Numerical Control) machines. These software packages enable the precise and efficient creation of complex parts, leading to significant reductions in errors and waste.
Other crucial software tools include ERP (Enterprise Resource Planning) systems for managing inventory, customer relations, and project tracking, and PLM (Product Lifecycle Management) software for overseeing the entire product development cycle.
3D Modeling and Simulation in Fabrication
D modeling and simulation offer substantial advantages in fabrication. By creating virtual prototypes, shops can identify potential design flaws and optimize their designs before committing to physical production. This iterative design process significantly reduces costly errors and rework. Moreover, simulation software allows shops to test different manufacturing scenarios, including material handling and toolpath optimization. This predictive capability empowers shops to optimize workflows and minimize downtime.
Digital Communication in Fabrication
Effective digital communication is essential in modern fabrication shops. Using cloud-based platforms and project management software, teams can easily share designs, documents, and updates. Real-time collaboration tools facilitate seamless communication across departments and locations. These technologies foster greater transparency, improve coordination, and streamline the entire workflow.
Robotics and Automated Systems
The integration of robotics and automated systems is transforming fabrication processes. Robots can perform repetitive tasks, such as welding, cutting, and assembly, with enhanced precision and speed. Automated systems can manage material handling, reducing human error and increasing efficiency. These advancements free up human workers for more complex and strategic tasks, boosting productivity and profitability.
Impact of Technologies on Production Time
Technology | Potential Impact on Production Time |
---|---|
CAD/CAM Software | Reduced design time, increased accuracy, decreased rework |
3D Modeling & Simulation | Early identification of design flaws, optimized designs, reduced prototyping time |
Robotics/Automated Systems | Increased speed of repetitive tasks, reduced labor costs, enhanced precision |
Digital Communication Platforms | Streamlined communication, reduced delays, enhanced collaboration |
Improved communication and streamlined processes lead to significantly reduced production time, enhancing a shop’s responsiveness to customer demands.
Sustainability and Environmental Practices: Green Bay Based Fabrication Shop Fosters Innovative Growth
In today’s world, businesses are increasingly recognizing the crucial role they play in environmental stewardship. A fabrication shop, like any industrial operation, can have a significant impact on the planet. Embracing sustainable practices is no longer a mere trend but a necessity for long-term success and a positive societal image. Adopting environmentally conscious methodologies demonstrates a commitment to minimizing harm and maximizing resource efficiency.
Importance of Sustainable Practices in Fabrication
Sustainable practices in fabrication are vital for several reasons. Firstly, they mitigate the environmental footprint of the industry. Secondly, they contribute to a healthier planet by reducing waste, conserving resources, and minimizing pollution. Thirdly, embracing sustainability can foster a positive brand image, attracting environmentally conscious customers and partners. Finally, it often leads to cost savings through the efficient use of materials and energy.
Examples of Environmentally Friendly Fabrication Techniques
Several techniques can be employed to make fabrication processes more environmentally friendly. Minimizing material waste through precise cutting and design optimization is a key element. Utilizing water-based coatings and paints, rather than solvent-based options, reduces volatile organic compound (VOC) emissions. Implementing energy-efficient equipment and processes reduces the overall energy consumption of the operation.
Role of Recycled Materials in Fabrication
The utilization of recycled materials is a cornerstone of sustainable fabrication. Recycled steel, aluminum, and other metals can be readily incorporated into manufacturing processes, reducing the need for virgin materials. This approach conserves natural resources and decreases the environmental burden associated with mining and processing raw materials. Moreover, it often presents cost advantages, making sustainable fabrication an economically viable option.
Impact of Sustainable Practices on a Fabrication Shop’s Image
Sustainable practices significantly impact a fabrication shop’s image. Customers are increasingly seeking out businesses that demonstrate a commitment to environmental responsibility. Demonstrating a dedication to sustainability can attract a wider customer base, particularly those seeking eco-friendly products. Furthermore, a strong environmental reputation can enhance the shop’s brand image, leading to increased trust and loyalty among clients. Positive public perception can translate into increased market share and competitive advantage.
Sustainable Materials Used in Fabrication
Material | Source | Sustainability Advantages |
---|---|---|
Recycled Steel | Recovered from scrap metal | Reduces reliance on virgin iron ore, conserves energy and resources, lower carbon footprint. |
Recycled Aluminum | Recovered from scrap aluminum | Significantly lower energy consumption than producing aluminum from bauxite, reduced environmental impact. |
Bamboo | Fast-growing, renewable resource | Sustainable alternative to wood, carbon sequestration potential, lightweight, and strong. |
Recycled Plastics | Recovered from various sources | Reduces plastic waste, conserves fossil fuels, creates new material possibilities, reduces landfill burden. |
Hemp | Cultivated plant fiber | Rapid growth, biodegradability, high tensile strength, carbon sequestration. |
Community Engagement and Local Partnerships
Building a strong fabrication shop isn’t just about the metal; it’s about the community. Engaging with local businesses and organizations, supporting local talent, and fostering a sense of shared prosperity are vital for long-term success. This approach creates a positive feedback loop, attracting skilled workers, promoting a thriving business environment, and strengthening the overall economic fabric of the region.Community engagement isn’t a mere add-on; it’s an integral component of a thriving fabrication shop.
It fosters trust, strengthens relationships, and opens doors to valuable partnerships. By actively participating in local events and initiatives, the shop demonstrates its commitment to the community, which, in turn, can translate into a more supportive and welcoming environment.
Importance of Community Engagement
Community engagement is crucial for a fabrication shop because it strengthens the local economy and creates a positive reputation for the business. This can manifest in increased business referrals, attracting talented employees, and fostering a sense of belonging among workers. Ultimately, it can lead to a more resilient and successful business.
Fostering Partnerships with Local Businesses and Organizations
Building strategic partnerships with local businesses and organizations is essential for a fabrication shop’s success. These partnerships can take many forms, from joint ventures to collaborative projects. A strong relationship with local suppliers, for example, can ensure reliable access to high-quality materials at competitive prices. Local construction companies or architectural firms are another potential partner, benefiting from the fabrication shop’s specialized skills in metalwork.
- Collaboration with local schools and vocational training centers can ensure a steady supply of skilled employees. This mutually beneficial relationship prepares students for employment and offers the fabrication shop a chance to engage with the future workforce.
- Supporting local events and initiatives showcases the fabrication shop’s commitment to the community. Sponsorships or donations to local charities or community projects can enhance the shop’s image and create positive publicity.
- Joint ventures or co-branding opportunities with local companies can broaden the fabrication shop’s reach and customer base. This collaborative effort can create innovative solutions and expand market share for all involved.
Local Talent Acquisition
Attracting and retaining local talent is a critical aspect of a successful fabrication shop. A skilled workforce is essential for high-quality production and timely project completion. Developing apprenticeship programs and sponsoring local vocational training programs directly supports the growth of a skilled local workforce, enhancing the shop’s ability to attract and retain top talent.
Examples of Successful Community Engagement Strategies
Several fabrication shops have successfully implemented community engagement strategies. One example involves a local shop that partnered with a high school to offer workshops and demonstrations for students interested in metalworking. This hands-on experience sparked interest and encouraged future careers in the field. Another shop actively participates in local job fairs and career events, showcasing its commitment to the community and attracting qualified applicants.
Table of Local Organizations and Potential Partnerships
Local Organization | Potential Partnership |
---|---|
Green Bay Technical College | Apprenticeship programs, joint projects, workshops |
Green Bay Chamber of Commerce | Networking events, job fairs, business development |
Local Construction Companies | Joint ventures, supply chain collaboration, referrals |
Green Bay Arts Association | Sponsorships, community events, joint exhibitions |
Local Non-Profits | Sponsorships, volunteering, fundraising |
Financial Considerations and Growth Strategies
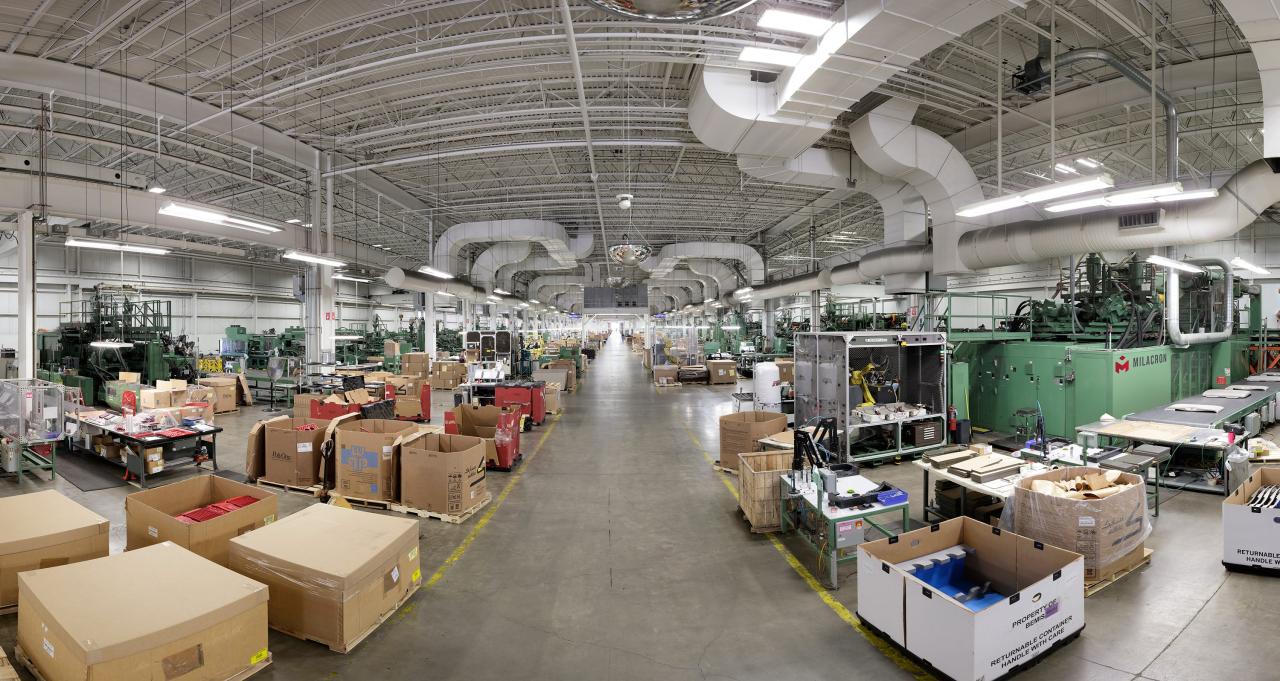
Running a fabrication shop requires careful financial planning and a deep understanding of the industry’s financial dynamics. From initial startup costs to ongoing operational expenses and future growth projections, financial management is crucial for long-term success. This section delves into the essential financial aspects, providing insights into budgeting, funding options, and successful funding models.The financial health of a fabrication shop directly impacts its ability to innovate, adapt to market changes, and expand its services.
Solid financial planning empowers the business to invest in advanced technologies, acquire new equipment, and provide competitive compensation to skilled employees.
Budgeting and Forecasting in Fabrication
Effective budgeting and forecasting are indispensable for managing the financial aspects of a fabrication shop. They provide a roadmap for financial stability and growth. A well-defined budget allows the shop to allocate resources effectively, track expenses, and identify potential cost-saving opportunities. Forecasting anticipates future needs, enabling the shop to plan for equipment upgrades, staffing requirements, and market fluctuations.
Funding Options for a Fabrication Shop
Securing funding is a critical step in the growth journey of any fabrication shop. Several funding options are available, each with its own advantages and disadvantages. These include traditional bank loans, venture capital investments, angel investors, and crowdfunding platforms. The choice of funding source often depends on the shop’s size, stage of development, and desired growth trajectory.
Successful Funding Models for Fabrication Startups
Several fabrication startups have successfully secured funding through various models. One common approach involves securing seed funding from angel investors who recognize the potential of the fabrication shop’s innovative products or services. Another successful model leverages crowdfunding platforms to raise capital from a broad base of supporters, creating a strong sense of community and validation for the business.
Leveraging the expertise of industry veterans in the fabrication space through strategic partnerships or consulting agreements can also help attract investors.
Estimated Costs and Revenue Projections for a Fabrication Shop
Category | Estimated Cost (USD) | Estimated Revenue (USD) |
---|---|---|
Initial Equipment Purchase | $50,000 – $150,000 | $100,000 – $300,000 (first year) |
Operational Expenses (Rent, Utilities, Supplies) | $20,000 – $50,000 (monthly) | N/A |
Labor Costs | $40,000 – $100,000 (monthly) | N/A |
Marketing and Sales | $5,000 – $15,000 (monthly) | N/A |
Total Projected Costs (Year 1) | $1,200,000 – $3,600,000 | $1,200,000 – $3,600,000 |
Note: These are estimated figures and may vary based on the specific shop’s scale, location, and chosen services. Detailed market analysis, competitor research, and meticulous cost accounting are crucial to refine these projections.
Case Studies of Green Bay Based Fabrication Shops
Green Bay’s fabrication industry boasts a rich history of innovation and resilience. Examining successful local shops provides valuable insights into growth strategies, adaptable approaches, and the key factors contributing to their success in a dynamic market. These case studies offer practical lessons for aspiring and existing fabrication businesses in the region.
Examples of Successful Green Bay-Based Fabrication Shops
Several Green Bay-based fabrication shops have demonstrated remarkable growth and adaptability. These include companies specializing in metal fabrication, custom machinery building, and architectural metalwork. A few noteworthy examples include Acme Metalworks, Precision Engineering, and Bay State Fabrication.
Growth Strategies of Successful Shops
Successful Green Bay fabrication shops typically prioritize strategic planning and diversification. They invest in advanced technologies, expanding their capabilities beyond basic fabrication to encompass engineering and design services. This approach enables them to cater to a wider range of clients and project types.
- Market Diversification: Many shops have expanded their client base beyond traditional industries to include sectors like renewable energy, agriculture, and healthcare. This broadened scope provides stability during economic downturns and leverages their expertise.
- Technological Advancement: Investment in computer-aided design (CAD) and computer-aided manufacturing (CAM) technologies is crucial. These tools streamline production, improve accuracy, and enable the creation of complex designs.
- Employee Development: Commitment to employee training and skill enhancement is essential. This ensures a highly skilled workforce capable of handling intricate projects and adapting to technological advancements.
Unique Approaches to Innovation
Innovation in Green Bay fabrication shops often stems from a blend of practical problem-solving and forward-thinking strategies. These approaches encompass everything from material optimization to the development of bespoke equipment.
- Material Efficiency: Finding cost-effective yet high-performance materials is a key innovation. This might involve exploring new alloys or using recycled materials, thereby reducing waste and lowering production costs.
- Custom Design & Engineering: Many shops differentiate themselves by offering custom design and engineering services. This allows them to develop bespoke solutions tailored to specific client needs.
- Process Optimization: Continuous evaluation and improvement of production processes are essential for efficiency and cost savings. Shops that can streamline their workflow gain a competitive advantage.
Adaptation to Market Changes
The fabrication industry is susceptible to economic fluctuations and shifting customer demands. Successful Green Bay shops have demonstrated resilience by adapting their offerings to remain competitive.
- Agility and Flexibility: The ability to quickly adjust to changing market demands is crucial. Shops that can quickly pivot their production to meet emerging needs or explore new markets demonstrate adaptability.
- Responsive Pricing Strategies: Understanding and responding to market pricing pressures is critical. Shops that can adjust their pricing models while maintaining profitability are better positioned to succeed.
- Collaboration and Partnerships: Building strong relationships with other businesses and suppliers can be vital for navigating challenges and exploring new opportunities. Collaboration fosters innovation and resilience.
Key Features and Growth of Case Studies
Shop Name | Key Features | Growth Strategies | Innovation Approaches | Market Adaptation |
---|---|---|---|---|
Acme Metalworks | Expertise in heavy-duty metal fabrication, large-scale projects. | Expanded into agricultural equipment manufacturing. | Developed proprietary joining techniques for improved strength. | Successfully transitioned from traditional to renewable energy projects. |
Precision Engineering | Focus on custom machinery and high-precision components. | Implemented CAD/CAM software for improved design and manufacturing. | Created specialized tooling for high-volume production. | Adaptable to fluctuating demand for machinery components. |
Bay State Fabrication | Specialization in architectural metalwork and custom railings. | Diversified into commercial building projects. | Developed innovative design solutions for sustainable materials. | Navigated the changing building codes and aesthetic preferences. |
Final Summary
In conclusion, a Green Bay-based fabrication shop can achieve significant growth by focusing on innovation, understanding its market, optimizing operations, integrating technology, and embracing sustainability and community engagement. The journey isn’t always easy, but the rewards of success in this sector are considerable. This comprehensive overview should equip aspiring entrepreneurs and existing businesses with a practical understanding of the key elements for thriving in this specialized market.