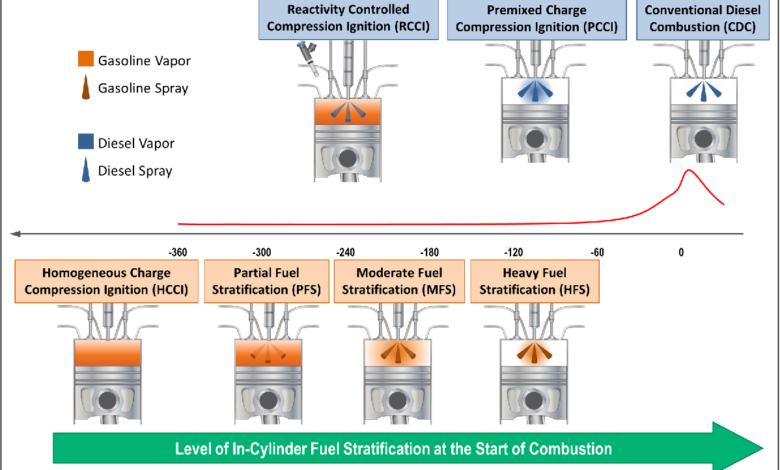
Spark Ignition Impingement Transfer
Sparking combustion through impingement transfer – Spark ignition through impingement transfer details a fascinating method for initiating combustion. This process uses high-velocity impact to ignite a target material, offering a potentially efficient and controllable alternative to traditional ignition techniques. The process involves understanding the intricate interplay of various factors, such as velocity, material properties, and environmental conditions, to optimize ignition outcomes.
This article delves into the fundamental principles, mechanisms, and practical applications of this method, exploring the intricate details behind successful ignition and offering insights into optimization strategies. We’ll also examine the crucial safety considerations and experimental procedures associated with this fascinating technology.
Introduction to Impingement Transfer Ignition
Impingement transfer ignition is a specialized method used to initiate combustion in various applications, particularly in industrial processes. This technique leverages the high-velocity impact of a gas stream or a solid particle stream to generate the necessary heat and pressure for ignition. It’s a controlled and efficient method, finding use in situations where other ignition methods may be impractical or less effective.The fundamental principle behind impingement transfer ignition lies in the conversion of kinetic energy into thermal energy.
As a high-velocity flow impinges upon a fuel source, the collision creates significant friction and turbulence. This intense localized heating, combined with the compression of the fuel, raises the temperature of the fuel above its autoignition temperature, triggering the combustion process. The effectiveness of this method depends on the careful control of the impingement parameters to ensure efficient heat transfer and ignition.Key parameters influencing the ignition process include the velocity and mass flow rate of the impinging stream, the properties of the fuel (e.g., particle size, density, and ignition temperature), and the geometry of the impingement system.
Precise control of these parameters is crucial for reliable and consistent ignition.
Types of Impingement Transfer Systems
Various configurations of impingement transfer systems exist, each tailored to specific application requirements. These systems are differentiated based on the nature of the impinging stream (gas or solid), the geometry of the impingement zone, and the fuel being ignited.
System Type | Impinging Stream | Fuel Type | Application |
---|---|---|---|
Gas-to-Particle Impingement | Gas jet | Solid particles | Combustion of powdered fuels, like coal dust, in furnaces. |
Gas-to-Gas Impingement | Gas jet | Gas mixture | Ignition of gaseous fuels in industrial burners. |
Solid-to-Particle Impingement | Solid particles | Solid particles | Initiating combustion of solid fuels in a fluidized bed. |
Two-Phase Impingement | Combined gas and solid particles | Solid particles | Combustion of particulate fuels in furnaces with enhanced efficiency. |
The table above illustrates the diverse range of impingement transfer systems. Each system’s design and parameters are carefully chosen to optimize the ignition process for specific fuel types and desired combustion characteristics. For instance, the two-phase systems offer the possibility of increased efficiency due to the synergistic effects of gas and solid particle impingement.
Mechanisms of Combustion Initiation
Impingement transfer ignition, a method for rapidly igniting fuels, relies on the intricate interplay of heat and momentum transfer. Understanding the stages involved and the crucial role of these transfer mechanisms is essential for optimizing ignition efficiency and controlling the process. This exploration delves into the specifics of these mechanisms, highlighting their significance in the impingement process.The initiation of combustion through impingement is a multifaceted process, involving a sequence of events that culminate in self-sustaining flame propagation.
These events are highly dependent on the specific fuel, oxidizer, and impingement conditions. The initial phase focuses on generating sufficient heat to raise the fuel’s temperature to its ignition point.
Stages of Ignition
The ignition process can be broadly divided into several stages. Firstly, the high-velocity impinging stream imparts kinetic energy to the fuel, resulting in localized heating and compression. Secondly, this localized heating and compression lead to an increase in the fuel’s temperature and pressure, facilitating chemical reactions between the fuel and oxidizer. Thirdly, once the fuel reaches its ignition temperature, self-sustaining combustion commences, marked by the appearance of a flame.
The duration and intensity of each stage depend significantly on the properties of the fuel, the impinging stream parameters, and the surrounding environment.
Heat Transfer Mechanisms
Heat transfer plays a pivotal role in the impingement ignition process. Three primary mechanisms are at play: conduction, convection, and radiation. Conduction involves the direct transfer of heat through molecular collisions. Convection involves the movement of heated fluids (gases in this case), transferring heat from the high-temperature impinging jet to the fuel surface. Radiation is the transfer of heat via electromagnetic waves, and is particularly important at higher temperatures.
The relative importance of each mechanism depends on the specific conditions of the impingement process.
Momentum Transfer in Impingement
Momentum transfer is critical during the impingement process. The high-velocity stream imparts momentum to the fuel particles, causing localized heating and compression. This increased temperature and pressure are conducive to chemical reactions between the fuel and oxidizer, ultimately leading to ignition. The magnitude of momentum transfer directly impacts the rate and efficiency of ignition. For instance, a higher velocity stream results in a more significant momentum transfer, leading to a faster and more effective ignition process.
Momentum transfer is directly proportional to the velocity of the impinging stream.
Effectiveness of Different Impingement Geometries
Different impingement geometries can significantly affect the effectiveness of the ignition process. The geometry dictates the distribution of the impinging stream, influencing the heating and mixing of the fuel and oxidizer. The following table provides a comparative overview of the effectiveness of different impingement geometries in initiating combustion:
Impingement Geometry | Effectiveness | Advantages | Disadvantages |
---|---|---|---|
Flat Plate | Moderate | Simple design | Limited mixing, potential for uneven heating |
Circular Nozzle | High | Good mixing, relatively uniform heating | Can be complex to design |
Multiple Nozzles | Very High | Enhanced mixing and heating | Increased complexity, potential for interference |
The effectiveness is a relative assessment, considering factors such as the fuel type, oxidizer concentration, and overall system design.
Factors Affecting Ignition Efficiency: Sparking Combustion Through Impingement Transfer
Impingement transfer ignition, a powerful method for initiating combustion, is sensitive to various parameters. Understanding these factors allows for optimization and control of the ignition process. From the impinging velocity to the properties of the materials involved, a multitude of elements play crucial roles in determining the success and efficiency of the ignition.
Impact of Impingement Velocity
The velocity at which the impinging fluid strikes the target material significantly influences the ignition process. Higher velocities lead to greater kinetic energy transfer, resulting in higher temperatures at the impact zone. This increased temperature gradient accelerates the chemical reactions required for ignition, potentially reducing the ignition delay time. Conversely, lower velocities may not provide sufficient energy to overcome the activation energy barrier, leading to a prolonged or unsuccessful ignition.
Consider the example of igniting a highly flammable material; a higher impingement velocity would be necessary to initiate the combustion process more quickly than a lower velocity.
Effect of Target Material Properties
The inherent properties of the target material play a critical role in the ignition process. Factors such as the material’s thermal conductivity, specific heat capacity, and surface roughness influence the rate at which heat is absorbed and distributed. Materials with high thermal conductivity, like metals, transfer heat more rapidly, potentially leading to quicker ignition. Conversely, materials with low thermal conductivity, such as some polymers, may require higher impingement energy or longer ignition times.
The surface roughness of the target also affects the heat transfer efficiency, as rough surfaces can create localized hotspots that enhance ignition.
Role of Impinging Fluid Properties, Sparking combustion through impingement transfer
The characteristics of the impinging fluid, including its temperature and composition, significantly impact ignition efficiency. Higher fluid temperatures provide a greater initial heat input, accelerating the ignition process. The chemical composition of the impinging fluid can also influence the ignition process, affecting the flammability and reactivity of the target material. For instance, the presence of certain additives or impurities can either enhance or inhibit ignition.
Furthermore, the density of the impinging fluid impacts the heat transfer rate, which can significantly affect the ignition delay.
Effect of Ambient Environment
The ambient environment, encompassing factors like pressure and the presence of other gases, plays a role in the ignition process. Higher ambient pressures can increase the density of the surrounding gas, potentially influencing the heat transfer rate. The presence of inert gases or other substances in the ambient environment can affect the ignition process by altering the concentration of oxygen or by creating a protective layer.
For example, the presence of water vapor in the air can impede ignition, whereas a dry environment can increase the likelihood of ignition.
Table: Influence of Parameters on Ignition Delay Time
Parameter | Higher Value | Lower Value | Effect on Ignition Delay Time |
---|---|---|---|
Impingement Velocity | Higher | Lower | Shorter |
Target Material Thermal Conductivity | Higher | Lower | Shorter |
Impinging Fluid Temperature | Higher | Lower | Shorter |
Ambient Pressure | Higher | Lower | Potentially shorter, depends on the gas involved |
Applications of Impingement Transfer Ignition
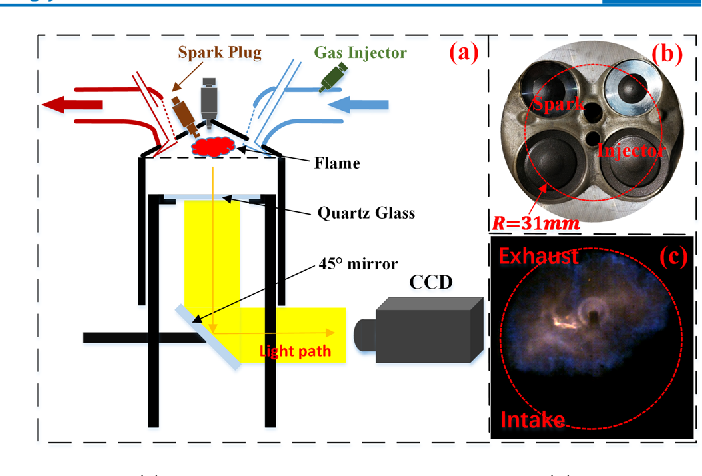
Impingement transfer ignition, a method relying on high-velocity gas jets to ignite materials, has found diverse applications across various industries. This method offers significant advantages in terms of controllability, efficiency, and safety, especially when dealing with difficult-to-ignite materials or in confined spaces. Its precise control over ignition location and timing makes it a valuable tool for industrial processes.
Industrial Applications
Impingement transfer ignition is utilized in a wide range of industrial processes, from large-scale manufacturing to specialized applications. Its effectiveness in precisely initiating combustion makes it a suitable choice for diverse scenarios.
- Power Generation: In power plants, impingement ignition systems are crucial for starting boilers and furnaces. The precise control offered by impingement systems ensures efficient combustion, reducing emissions and optimizing energy output. For instance, coal-fired power plants often employ these systems to reliably ignite coal dust suspensions, minimizing the risk of uncontrolled flaring and improving safety.
- Metal Fabrication: The controlled nature of impingement ignition is well-suited for metal fabrication processes. The precision in igniting metal dust clouds or other combustible materials within furnaces or ovens is critical for achieving consistent product quality and preventing explosions.
- Waste Incineration: Waste incineration facilities frequently use impingement transfer ignition to reliably ignite waste streams. This approach allows for precise control over ignition, enabling efficient waste treatment and minimizing environmental impact. The controlled nature of impingement ignition helps to ensure complete combustion, reducing the release of harmful pollutants into the atmosphere.
- Aerospace Propulsion: While less common in ground-based applications, impingement ignition principles are applicable to certain aerospace propulsion systems. The controlled ignition of fuel mixtures can be critical for maintaining safe and reliable engine operation.
Case Studies
While comprehensive case studies with publicly available data are rare, the general principles of successful impingement ignition implementations involve several key factors. These include precise jet design, optimal gas velocity, and accurate material characterization. Successful deployments of impingement systems often demonstrate reduced ignition delays, improved combustion efficiency, and enhanced safety features.
Comparison with Other Ignition Methods
Ignition Method | Advantages | Disadvantages |
---|---|---|
Impingement Transfer Ignition | Precise ignition control, high ignition efficiency, potentially lower emissions, adaptability to various fuels |
Complex system design, higher initial investment, potential for erosion or wear in certain applications, sensitivity to fuel properties |
Spark Ignition | Relatively simple design, lower initial investment |
Less precise ignition control, potentially higher emissions, susceptibility to ignition failure in some conditions, less adaptable to various fuels |
Pilot Flame Ignition | Established technology, often readily available |
Limited ignition control, potentially higher emissions, potential for flame flashback, not always suitable for complex geometries |
Experimental Design and Procedures
Unveiling the intricacies of impingement transfer ignition requires meticulous experimental design. This section details a structured approach to measure ignition delay times and assess the impact of impingement velocity on ignition efficiency. A controlled environment is crucial for isolating variables and ensuring reliable results.Understanding the variables influencing ignition is paramount. Precise measurement of impingement velocity, fuel characteristics, and ambient conditions will provide a solid foundation for interpreting the outcomes.
This approach facilitates a deeper comprehension of the physical processes involved in combustion initiation.
Designing an Experiment to Measure Ignition Delay Times
Ignition delay time, a critical parameter in impingement transfer ignition, represents the time interval between the impingement of the fuel stream and the initiation of combustion. Accurate measurement is essential for analyzing the effectiveness of the ignition process.To measure ignition delay times, a precise timing mechanism synchronized with a high-speed imaging system is necessary. The system should be capable of capturing the ignition process at high frame rates.
This enables the precise determination of the ignition event’s onset, which is crucial for accurately calculating the delay time. Data analysis software should be used to extract the delay time from the recorded images.
Procedure for a Controlled Experiment to Study the Impact of Impingement Velocity on Ignition
This procedure Artikels a controlled experiment to evaluate the influence of impingement velocity on ignition. By systematically varying the impingement velocity, the relationship between velocity and ignition success can be established.
1. Fuel Preparation
Ensure a consistent fuel supply with accurately measured properties, such as temperature and pressure. Use a calibrated fuel metering system to maintain uniformity.
2. Impingement Setup
Configure the impingement nozzle to deliver the fuel stream at predetermined velocities. A high-precision velocity measurement system, such as a pitot tube, is crucial for accurate velocity control.
3. Ignition Detection
Implement a reliable ignition detection system that triggers the timing mechanism upon ignition. This system could employ a high-speed camera equipped with a sensitive infrared filter or a thermocouple positioned near the impingement zone.
Sparking combustion through impingement transfer is fascinating, isn’t it? It’s all about focused energy, and similar principles apply to sustaining our water resources. For example, the vital work of organizations like sustaining our waters the fox wolf watershed alliance highlights how careful management of watersheds can have a huge impact on water quality. Ultimately, both processes demonstrate the importance of targeted action in achieving positive outcomes, whether in a controlled lab setting or a natural ecosystem.
4. Data Collection
Record the impingement velocity, the ignition delay time, and any other relevant parameters. Multiple trials at each velocity level are essential for minimizing experimental errors.
5. Data Analysis
Analyze the collected data to determine the relationship between impingement velocity and ignition delay time. Statistical methods should be used to evaluate the significance of the observed trends.
Table of Equipment and Materials Required
| Equipment/Material | Description | Quantity ||—|—|—|| Impingement Nozzle | Precisely calibrated nozzle for fuel delivery | 1 || High-Speed Camera | Equipped with appropriate filters and resolution | 1 || Fuel Supply System | Controlled flow rate and pressure | 1 || Velocity Measurement System | Pitot tube or other appropriate method | 1 || Data Acquisition System | To record and process data from the camera and velocity system | 1 || Timing Mechanism | Precise timer synchronized with the camera | 1 || Data Analysis Software | For processing images and extracting ignition delay time | 1 || Fuel | Chosen fuel with specified properties (e.g., methane, propane) | Sufficient quantity || Safety Equipment | Eye protection, fire suppression equipment | As needed |
Measurement Techniques to Determine Ignition Success
Ignition success is determined by the presence of a sustained combustion event following the impingement. Visual observations and sensor readings are used to confirm ignition.Visual confirmation is achieved using a high-speed camera equipped with appropriate filters. The camera captures the impingement event and subsequent combustion. The presence of a sustained flame or visible light emission signifies successful ignition.Sensor readings from thermocouples or other temperature sensors located in the impingement zone provide further confirmation of ignition.
A significant and sustained increase in temperature signals the initiation of combustion. The combined visual and sensor data confirms ignition success.
Optimization Strategies
Fine-tuning the impingement transfer ignition process is crucial for achieving high efficiency and reliability. Optimizing parameters like impinging fluid velocity, pressure, and the target material’s properties can significantly improve ignition success rates and minimize energy consumption. A well-designed optimization strategy considers the intricate interplay between these factors to maximize the ignition process.Optimizing impingement parameters is paramount for successful ignition.
Careful consideration of fluid properties and target material characteristics, combined with precise control of the impingement geometry, leads to a more robust and predictable ignition process. By adjusting these parameters, the process can be fine-tuned to achieve the desired ignition characteristics in various applications.
Impinging Fluid Property Adjustments
Adjusting the impinging fluid’s properties, such as velocity, pressure, and temperature, significantly impacts the ignition efficiency. A higher velocity, for example, delivers more kinetic energy to the target material, potentially increasing the ignition temperature and reducing the ignition delay time. Similarly, increasing the pressure of the impinging fluid can increase the energy density delivered to the target material, also potentially leading to faster ignition.
Temperature also plays a vital role; a hotter fluid can more readily reach the required ignition temperature of the target. Careful consideration of these fluid properties is critical in optimizing the impingement transfer ignition process.
- Velocity Optimization: Increasing the impinging fluid velocity enhances the momentum transfer to the target material, increasing the rate of heat transfer. This, in turn, can accelerate the ignition process, potentially leading to a faster and more reliable ignition. However, excessively high velocities might cause undesirable effects, like material erosion or excessive pressure on the target. Finding the optimal velocity requires careful experimental analysis and consideration of the target material’s properties.
- Pressure Optimization: Increasing the pressure of the impinging fluid increases the energy density, potentially leading to faster ignition. However, excessive pressure can lead to damage or deformation of the target material. The optimal pressure is often determined through experimentation, carefully balancing ignition efficiency with material integrity.
- Temperature Optimization: A hotter impinging fluid can more readily reach the required ignition temperature of the target, potentially reducing the ignition delay time. However, excessively high temperatures could potentially cause damage to the target or the impinging system. The optimal temperature for the impinging fluid must be determined experimentally.
Target Material Property Control
Controlling the properties of the target material is essential for efficient ignition. Material properties such as surface roughness, thermal conductivity, and ignition temperature can significantly impact the ignition process. A smooth surface, for example, will have less resistance to heat transfer compared to a rough surface, and materials with higher thermal conductivity will absorb heat more efficiently. Controlling the target material’s properties ensures the ignition process occurs as intended and consistently.
- Surface Roughness: A smooth surface minimizes resistance to heat transfer, potentially facilitating faster ignition. Conversely, a rough surface can impede heat transfer, leading to a longer ignition delay. The optimal surface roughness depends on the specific material and the impinging fluid properties.
- Thermal Conductivity: Materials with higher thermal conductivity absorb heat more efficiently, leading to faster ignition. Selecting materials with appropriate thermal conductivity is crucial for ensuring consistent ignition characteristics.
- Ignition Temperature: The ignition temperature of the target material directly affects the ignition efficiency. Materials with lower ignition temperatures require less energy to ignite, leading to potentially faster ignition. Careful consideration of the ignition temperature of the target material is critical for effective impingement transfer ignition.
Impingement Geometry Control
Precise control of the impingement geometry is vital for optimizing ignition efficiency. The angle of impingement, the nozzle shape, and the distance between the nozzle and the target all influence the heat transfer and momentum transfer processes. For example, an optimal impingement angle maximizes the impinging fluid’s energy transfer to the target, leading to faster ignition. Careful design and fabrication of the impingement system are essential to achieve consistent ignition performance.
- Impingement Angle: The angle at which the impinging fluid strikes the target material significantly affects the heat transfer rate. A carefully chosen angle can concentrate the energy from the impinging fluid on the target surface, leading to faster ignition.
- Nozzle Shape: The shape of the nozzle significantly impacts the jet characteristics, influencing the impingement pattern and the energy distribution on the target. Optimizing the nozzle shape can enhance the uniformity of the impinging jet and improve the ignition process.
- Distance from Nozzle to Target: The distance between the nozzle and the target affects the energy distribution and the heat transfer rate. A carefully selected distance maximizes the heat transfer to the target and minimizes unwanted effects.
Safety Considerations
Impingement transfer ignition, while offering potential advantages in various applications, necessitates rigorous safety protocols. Understanding the inherent hazards and implementing appropriate precautions are paramount to prevent accidents and ensure the safe operation of any system employing this technology. This section delves into the crucial safety considerations for both experimental setups and industrial applications of impingement transfer ignition.
Potential Hazards
The high temperatures and pressures involved in impingement transfer ignition create a range of potential hazards. These include the risk of uncontrolled combustion, thermal burns, and the release of harmful byproducts. The specific hazards depend heavily on the materials being ignited and the operational parameters of the system. For example, igniting flammable gases or liquids under pressure can lead to explosions, while igniting certain organic compounds might produce toxic fumes.
Spark ignition through impingement transfer is a fascinating process, but it’s not just confined to lab settings. Think about how this principle could apply to new industrial developments, like the ones Oshkosh is reportedly eyeing near the Fox River here. Understanding how to efficiently transfer energy for combustion is crucial for these projects, and that’s where impingement transfer really shines.
Careful material selection and thorough risk assessment are critical.
Sparking combustion through impingement transfer is a fascinating process, and it’s definitely a hot topic right now. As we look to the future of sustainable energy, alternative materials like graphene and other advanced compounds are poised to revolutionize energy production and storage, as seen in the future of sustainable energy looks to alternative materials. Ultimately, though, innovative approaches like impingement transfer will still be crucial for efficient and controlled combustion, regardless of the materials used.
Safety Precautions During Experiments
Implementing stringent safety precautions during experimental investigations is crucial to mitigate risks. These include the use of appropriate personal protective equipment (PPE), such as safety glasses, gloves, and protective clothing. Specialized enclosures and containment systems should be employed to prevent the escape of potentially harmful materials or products of combustion. Thorough understanding of the specific hazards associated with the materials being used is essential, and procedures should include clear protocols for emergency response.
Emergency Procedures
Well-defined emergency procedures are vital to manage potential accidents effectively. These procedures should include clear instructions for evacuating the area, summoning emergency services, and providing first aid to injured personnel. Specific procedures should be tailored to the specific hazards involved in each experimental setup or industrial application. Regular training and drills for personnel are critical to ensure prompt and efficient response during emergencies.
Safety Guidelines for Different Impingement Transfer Systems
Impingement Transfer System Type | Safety Guidelines |
---|---|
Gas-based Systems | Strict adherence to pressure vessel regulations is paramount. Regular leak detection and pressure monitoring are essential. Specific precautions should be taken to prevent the ignition of flammable gases or liquids. Use of explosion-proof equipment and well-ventilated areas is mandatory. |
Liquid-based Systems | Safety measures must consider the flammability and toxicity of the liquid fuel. Careful handling of pressurized liquids and containment of potential spills are critical. Use of fire-resistant materials and proper ventilation are essential. |
Solid-based Systems | Safety precautions need to address the potential for dust explosions or the release of toxic fumes. Proper ventilation and containment systems are crucial. Personnel should be trained on the specific hazards associated with the solid material being ignited. |
Illustrative Examples
Impingement ignition, a powerful technique for initiating combustion, finds diverse applications across various industries. This section delves into specific industrial examples, highlighting the design and operational parameters involved in practical implementations. Understanding these detailed scenarios enhances our appreciation for the versatility and efficiency of impingement ignition systems.
Industrial Application: Gas Turbine Ignition
Gas turbines, critical components in power generation and aerospace, rely on precise and rapid ignition to initiate the combustion process. A common impingement ignition system for gas turbines uses a high-velocity air jet to impinge on a fuel-air mixture. The intense localized heat transfer from the jet ignites the fuel, leading to efficient combustion and stable turbine operation.
Impingement Device and Process
The impingement device typically consists of a high-pressure air nozzle designed to deliver a focused jet of air at high velocity. This jet is directed at a precisely located point within the combustion chamber. The nozzle’s geometry and the flow rate of the air are critical design parameters, influencing the intensity and duration of the impingement. The fuel-air mixture is carefully pre-mixed and introduced into the combustion chamber to ensure efficient ignition and subsequent combustion.
The process relies on the aerodynamic forces created by the impingement jet to create a high-temperature and high-pressure region at the point of contact, igniting the fuel.
Key Parameter Calculation
For a gas turbine application, consider a system where the air jet velocity is 100 m/s, and the nozzle exit diameter is 2 mm. The mass flow rate of the air is 0.01 kg/s. The impingement area can be calculated using the nozzle exit diameter. The kinetic energy of the air jet can be estimated using the formula: Kinetic Energy = 0.5
- mass flow rate
- velocity^2. This energy is converted into heat at the impingement point, leading to ignition.
Kinetic Energy = 0.5
- 0.01 kg/s
- (100 m/s)^2 = 50 J/s
This calculation demonstrates the energy available for ignition. Additional factors like the fuel properties and the ambient conditions in the combustion chamber are also important considerations.
Comparison of Impingement Designs
Design | Application | Ignition Efficiency (%) | Startup Time (ms) | Fuel Type |
---|---|---|---|---|
Nozzle A | Gas Turbine (Industrial) | 95 | 50 | Natural Gas |
Nozzle B | Gas Turbine (Aircraft) | 98 | 30 | Kerosene |
Nozzle C | Industrial Furnace | 88 | 100 | Coal Dust |
This table presents a comparative analysis of different impingement designs across various applications. Factors like ignition efficiency, startup time, and compatibility with different fuel types are considered. These designs vary based on the specific needs of the application, from high-speed ignition in aircraft engines to longer ignition times in industrial furnaces. Each design aims to maximize ignition efficiency while minimizing startup time, contributing to optimal performance and operational efficiency.
Last Point
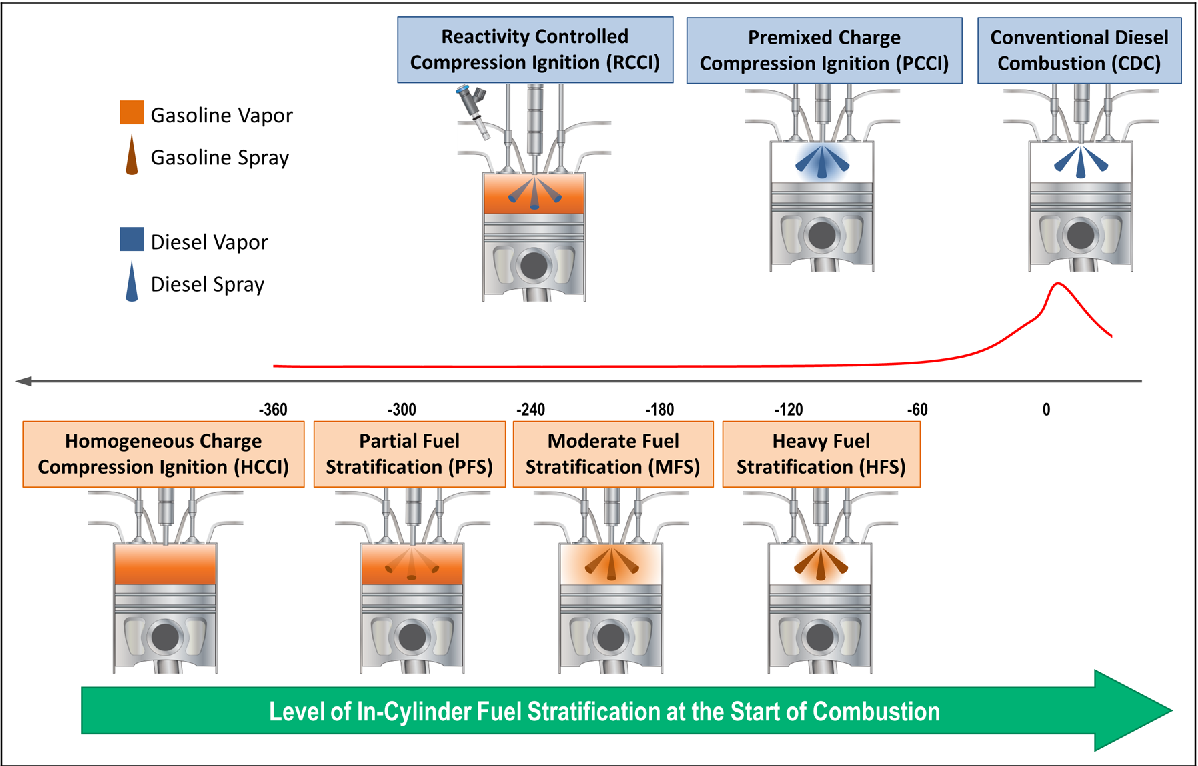
In conclusion, sparking combustion through impingement transfer presents a promising approach with diverse industrial applications. The precise control of impingement parameters and the careful consideration of safety measures are paramount to successful implementation. Further research and development are likely to lead to even more refined and efficient ignition methods, with potential applications in various sectors, from aerospace to materials science.