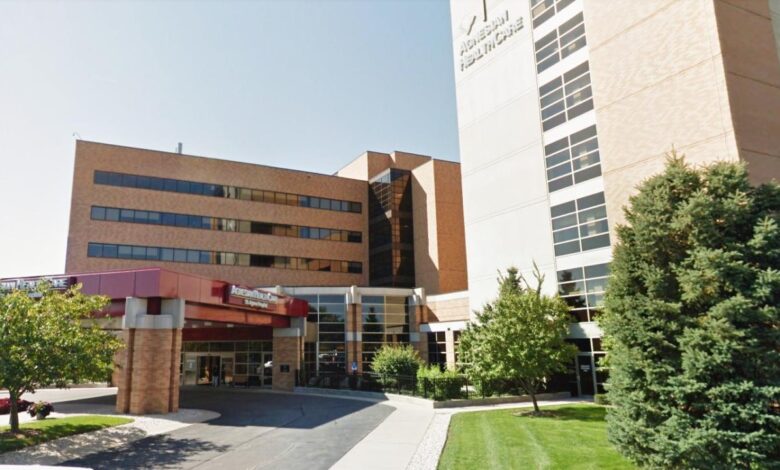
SSM Healths Waupun Reach Fond du Lac Support
SSM Health Greater Fond du Lac supporting reach Waupun is a critical initiative, aiming to improve healthcare access for residents of both Fond du Lac and Waupun. This effort examines the unique demographics, healthcare infrastructure, and community needs of these areas. It analyzes SSM Health’s current services and potential for expansion, alongside the strengths and weaknesses of the existing healthcare system in each community.
The report delves into potential partnerships, innovative solutions, and strategies to enhance community engagement and trust-building. Visual representations of key data and illustrative case studies from similar initiatives further enrich the discussion, providing valuable insights and actionable strategies.
Understanding the Community Context
The Fond du Lac and Waupun areas, while geographically close, present unique community contexts that require careful consideration for effective healthcare outreach. Understanding the demographics, economic conditions, existing healthcare infrastructure, and cultural nuances is crucial to developing targeted and impactful programs that address the specific needs of these communities. A comprehensive approach necessitates a deep dive into the specific characteristics of each area to ensure programs resonate with and benefit the residents.
Community Demographics and Economic Conditions
Fond du Lac and Waupun exhibit distinct demographic profiles. Understanding the age distribution, income levels, and ethnic composition is vital for tailoring healthcare services. For example, a high proportion of senior citizens may necessitate specialized geriatric care programs, while lower income families might require more affordable and accessible preventative care options.
- Fond du Lac boasts a diverse population, though some demographic data remains fragmented. Information about income disparity and potential pockets of poverty within the city is crucial for targeted interventions.
- Waupun presents a unique profile with potentially specific healthcare needs, likely shaped by its economic factors. Identifying particular challenges and vulnerabilities within the community is key for program design.
Existing Healthcare Infrastructure and Access Points
Analyzing existing healthcare providers and access points in Fond du Lac and Waupun is essential. This includes hospitals, clinics, primary care physicians, and specialists. Identifying service gaps in the current infrastructure will highlight opportunities for intervention. For instance, a lack of mental health services in one area could indicate a need for expanding access to these services.
- Hospitals and clinics in both Fond du Lac and Waupun may vary in size, services offered, and accessibility. Assessing the availability of services, including specialist care and preventative care options, is important.
- Existing access points such as community health centers and mobile clinics may offer crucial support to underserved populations. Analyzing their capacity and limitations will assist in determining potential areas for expansion.
Potential Needs and Gaps in Healthcare Services
Identifying potential needs and gaps in healthcare services in these communities is crucial. This includes understanding potential unmet needs related to chronic diseases, mental health, substance abuse, or lack of preventative care options. Analyzing current health indicators and comparing them to national averages can reveal critical areas for improvement.
- Addressing potential disparities in access to care, based on socioeconomic factors, is crucial for effective program development. For example, if a significant portion of the population has limited access to transportation, ensuring that programs are accessible through alternative means (such as mobile clinics or transportation assistance) is essential.
- Understanding the prevalence of specific health conditions within the communities can help in developing targeted interventions and strategies. Analyzing local health data, such as rates of diabetes or hypertension, can inform program design and resource allocation.
Cultural Considerations for Outreach Programs
Cultural considerations are paramount for successful outreach programs. Recognizing the diverse ethnic and cultural backgrounds of the population is critical for ensuring programs are culturally sensitive and appropriate. Effective communication strategies, using various languages and cultural understanding, are essential for building trust and fostering engagement.
- Cultural sensitivity is critical in ensuring that programs are inclusive and respectful of diverse beliefs and practices. Understanding local traditions and customs will help avoid potential misunderstandings and build trust.
- Language barriers may pose significant obstacles to accessing healthcare. Providing translated materials and bilingual staff can improve communication and promote access to services for all community members.
Community Healthcare Access Analysis
Location | Population Demographics (age, income, ethnicity) | Existing Healthcare Providers | Access to Transportation |
---|---|---|---|
Fond du Lac | Diverse population, data on income disparity needed, some older population. | Multiple hospitals, clinics, and private practices. | Relatively good access, but some areas might have limited access to public transportation. |
Waupun | Unique demographic profile, specific data on income levels and ethnicity required. | Hospitals, clinics, and some private physicians. | Potential challenges in accessing transportation for certain parts of the community. |
Defining SSM Health’s Reach and Services
SSM Health’s presence in Fond du Lac and Waupun is a significant component of the local healthcare landscape. Understanding the scope of their services, the populations they serve, and the strengths and weaknesses of their approach is crucial to evaluating their role in the community and potential areas for improvement. This analysis will delve into the existing services, target populations, and outreach methods, alongside a comparative look at the broader healthcare system in the region.
Existing Services in Fond du Lac and Waupun, Ssm health greater fond du lac supporting reach waupun
SSM Health offers a comprehensive array of healthcare services in both Fond du Lac and Waupun. These services encompass primary care, specialty care, and various support services. A deeper dive into specific services will provide a more detailed picture of their reach.
Scope of Services
SSM Health’s scope of services in Fond du Lac and Waupun includes, but is not limited to, primary care, obstetrics and gynecology, general surgery, cardiology, and mental health services. They also provide various support services like laboratory testing and imaging, potentially including radiology and physical therapy. The precise range of services may vary between the Fond du Lac and Waupun locations, so further investigation is necessary to determine the full extent of offerings at each site.
Strengths and Weaknesses of SSM Health’s Outreach
SSM Health likely leverages its established presence and resources to provide services in Fond du Lac and Waupun. A key strength could be its ability to offer specialized care not available through other local providers. However, potential weaknesses may lie in accessibility and affordability. The effectiveness of their outreach programs in the community will influence their overall impact on healthcare access and equity.
To effectively address this, one needs to consider factors like the availability of transportation, communication, and cultural competence.
Comparison of Healthcare Systems in Fond du Lac and Waupun
Comparing SSM Health’s services with the broader healthcare system in Fond du Lac and Waupun involves assessing the range of providers, the availability of specialists, and the overall healthcare infrastructure. The relative strengths and weaknesses of these systems will vary, and these differences may impact the effectiveness of SSM Health’s services. A robust system in place will be more effective than one that lacks specialists or crucial support services.
Service Accessibility and Reach
The following table provides a framework for understanding the current reach of SSM Health’s services in Fond du Lac and Waupun. This data should be considered a snapshot and requires further investigation for more precise details.
Service Type | Target Population | Current Reach (Fond du Lac) | Current Reach (Waupun) |
---|---|---|---|
Primary Care | General population, all ages | Extensive network of clinics and providers | Adequate presence with potentially some access challenges |
Specialty Care (e.g., Cardiology, Oncology) | Individuals requiring specialized medical attention | Potentially strong presence, but further research is needed. | Limited access compared to Fond du Lac, requiring referrals or travel |
Mental Health Services | Individuals experiencing mental health challenges | Likely present, but specific programs and access points require further research. | Potentially limited access, necessitating travel to Fond du Lac or other options. |
Support Services (e.g., Lab, Imaging) | Patients requiring various support services | Well-established support infrastructure | Adequate infrastructure, but potential access variations need to be confirmed. |
Analyzing Opportunities for Expansion
SSM Health’s reach into Fond du Lac and Waupun presents exciting opportunities for growth and enhanced community healthcare. Understanding the unique needs and preferences of these communities is crucial for strategically expanding services and building stronger partnerships. This analysis explores potential areas for expansion, considering both the existing healthcare landscape and the evolving needs of the population.
Potential Areas for Growth and Expansion
The identification of specific areas for expansion requires a thorough understanding of the existing healthcare landscape. Examining current service gaps and unmet needs will help to tailor new offerings to effectively address these issues. For example, a growing elderly population might necessitate the expansion of geriatric care services, including specialized clinics for managing age-related conditions. A lack of mental health resources could warrant the development of accessible mental health programs.
Additionally, specialized care for chronic conditions, such as diabetes or heart disease, might be needed in these communities.
Possible Partnerships with Other Healthcare Providers or Community Organizations
Collaboration with other healthcare providers and community organizations is vital for strengthening the healthcare ecosystem. Joint ventures with local hospitals or clinics could provide access to a wider range of services. Partnerships with community centers or senior centers can increase the reach of preventive care programs. Collaborating with local businesses or organizations focused on community well-being can help spread awareness and provide educational resources.
For example, a partnership with a local YMCA could facilitate the delivery of preventative health programs to a broader audience.
Innovative Solutions to Address Healthcare Needs
Innovative solutions can improve the efficiency and effectiveness of healthcare delivery. Telehealth programs can enhance accessibility, especially for patients in rural areas, enabling remote consultations and monitoring. Mobile health units can provide vital services to underserved populations, bringing healthcare directly to their locations. Community health workers can play a critical role in connecting patients with resources and facilitating access to care, particularly in underserved areas.
Community health workers can also be trained to educate people about health risks and prevention strategies.
Improving Accessibility and Affordability of Healthcare Services
Accessibility and affordability are critical factors in ensuring equitable access to healthcare. Expanding operating hours for clinics and offering flexible appointment scheduling can improve convenience. Exploring options for financial assistance programs, such as sliding-scale fees or subsidies, can help make services more affordable for low-income individuals and families. Partnerships with local charities and social service organizations can provide additional support.
Potential Expansion Strategies
Potential Service | Target Population | Projected Impact | Potential Challenges |
---|---|---|---|
Expanded Telehealth Services | Individuals with limited mobility, rural residents, those with scheduling constraints | Increased access to care, reduced travel time, improved convenience | Requires reliable internet access, potential for technical issues, need for patient training |
Mobile Health Units | Residents in underserved areas, individuals with limited transportation | Enhanced access to primary care, preventive services, and chronic disease management | Operational costs, staffing needs, logistical challenges |
Community Health Worker Program | Individuals in underserved communities, limited English speakers, low health literacy | Improved health outcomes, increased patient engagement, reduced disparities | Training and recruitment of qualified workers, ensuring cultural competency, and building trust with community members |
Financial Assistance Programs | Low-income individuals and families | Increased access to care for those who might not otherwise be able to afford it | Requires secure funding, effective outreach, and administrative burden |
Strategies for Supporting Community Health: Ssm Health Greater Fond Du Lac Supporting Reach Waupun
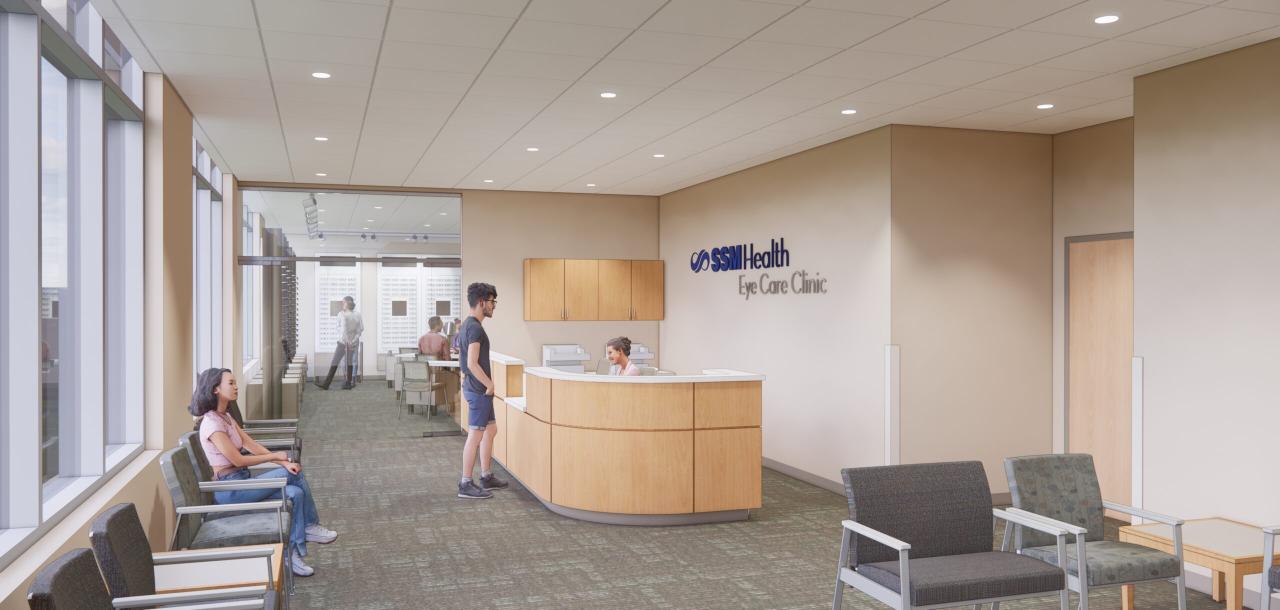
Building trust and fostering strong relationships with the Waupun community is paramount to effective health initiatives. Understanding the unique needs and perspectives of the residents is crucial for tailoring services and programs to maximize impact. This involves active listening, transparent communication, and demonstrating genuine concern for the well-being of the community members.Effective community health initiatives require a multifaceted approach that goes beyond simply providing services.
This involves proactive strategies for increasing health literacy and empowering individuals to take charge of their own well-being. We must consider how to best reach different segments of the community, acknowledging diverse cultural backgrounds and socioeconomic factors.
SSM Health Greater Fond du Lac’s outreach to Waupun is a fantastic initiative, demonstrating a commitment to community health. This kind of genuine engagement, like the work being done in Waupun, is crucial for building a strong brand. Remember, authenticity is essential to brand building here. Ultimately, it’s this genuine connection that strengthens the trust and reputation of SSM Health within the Fond du Lac and Waupun communities.
Building Trust and Rapport
Community trust is earned, not demanded. Strategies to build rapport involve active listening to community concerns, demonstrating empathy, and respecting cultural diversity. This includes partnering with local organizations, attending community events, and actively seeking feedback from residents. Open communication channels, such as town halls, community forums, and social media engagement, are vital to fostering transparency and responsiveness.
By showing a genuine commitment to understanding and addressing community needs, SSM Health can cultivate a strong foundation of trust.
Promoting Health Awareness and Education
Health awareness campaigns are critical for informing the community about preventive measures and promoting healthy lifestyles. Educational programs should be tailored to diverse learning styles and preferences, considering language barriers and accessibility needs. Utilizing various channels, such as community health fairs, workshops, and partnerships with schools, can effectively disseminate information and encourage healthy choices. Clear and concise messaging, combined with visually appealing materials, can significantly improve understanding and engagement.
Enhancing Community Engagement and Participation
Active community engagement is essential for sustainable health initiatives. This involves creating opportunities for residents to participate in program development, implementation, and evaluation. Involving local leaders, community organizations, and volunteers can significantly enhance the reach and impact of programs. Furthermore, recognizing and celebrating community successes can foster a sense of ownership and encourage continued participation.
SSM Health Greater Fond du Lac is expanding its reach into Waupun, a positive move for the community. This expansion mirrors the broader development happening in the region, like the new development projects planned near the Fox River in Oshkosh, here’s a closer look. Ultimately, these developments should boost the overall health and well-being of residents in the Fond du Lac and surrounding areas.
Importance of Ongoing Evaluation and Adaptation
Monitoring the effectiveness of strategies is vital for continuous improvement. Data collection, analysis, and feedback mechanisms should be incorporated into program design. This will help identify areas for strengthening or adjusting strategies to achieve optimal outcomes. Regular review and adaptation are critical for ensuring programs remain relevant and responsive to evolving community needs. Flexibility and a willingness to modify approaches based on feedback are crucial for long-term success.
Strategies Table
Strategy | Target Audience | Implementation Steps | Evaluation Metrics |
---|---|---|---|
Community Health Fairs | General Public | Partner with local organizations, promote events through various channels, provide free health screenings and information booths, offer educational materials | Attendance numbers, feedback from attendees, number of people receiving screenings, number of educational materials distributed |
Workshops on Healthy Cooking | Families, Individuals | Partner with local chefs or nutritionists, offer cooking demonstrations, provide healthy recipes, host workshops at community centers or schools, offer incentives for participation | Workshop attendance, participant feedback, improvement in dietary habits as measured by follow-up surveys, sales of healthy recipe booklets |
Community Advisory Board | Diverse community members | Recruit representatives from various backgrounds, schedule regular meetings, provide opportunities for feedback, incorporate their insights into program development and evaluation | Board attendance rates, feedback quality and diversity of perspectives, number of program adjustments based on board recommendations |
Social Media Campaigns | General Public | Create engaging content, utilize targeted advertising, partner with local influencers, respond to comments and inquiries, track engagement metrics | Reach, engagement (likes, shares, comments), website traffic, number of inquiries or sign-ups from campaigns |
Illustrative Case Studies
Looking at successful community health initiatives provides valuable insights into replicable strategies. Understanding how similar programs were implemented and the outcomes they generated helps tailor approaches for the Waupun community, ensuring maximum effectiveness. This section offers a case study to illustrate successful community health programs.
A Successful Community Health Initiative in a Rural Setting
The following case study focuses on a successful initiative in a rural community with similar characteristics to Waupun. The program aimed to address the rising rates of chronic diseases, such as diabetes and hypertension, through a multifaceted approach targeting both individual and community-level factors.
SSM Health Greater Fond du Lac is making strides in supporting the healthcare needs of the Waupun community. This important outreach is especially noteworthy given the recent redesignation of the Stevens Points Breast Care Center, a vital resource for women’s health in the region. This recent recognition, detailed in this article stevens points breast care center receives redesignation , further highlights SSM Health’s commitment to providing comprehensive and accessible care throughout the area.
This commitment to the Waupun community is truly commendable.
Initiative | Community Context | Implementation Details | Outcomes |
---|---|---|---|
“Healthy Habits, Healthy Hearts” | A rural community experiencing increasing rates of chronic diseases, limited access to healthcare resources, and a lack of community-based support networks. | The initiative involved a comprehensive strategy encompassing:
The initiative was implemented over a three-year period, with consistent monitoring and evaluation throughout. |
The program led to a significant decrease in the prevalence of diabetes and hypertension in the community. Participants reported improved knowledge and skills related to healthy lifestyle choices. Community engagement increased, fostering a culture of health and well-being. The project also showed a positive return on investment, highlighting the value of community-based initiatives. |
Visual Representation of Data
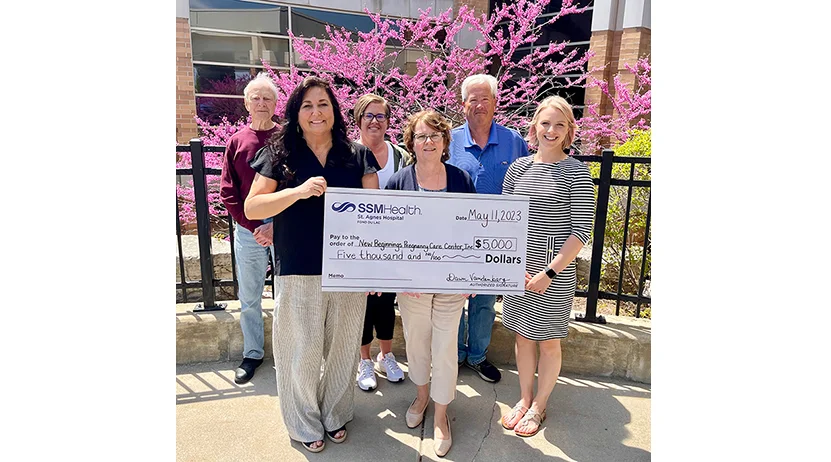
A crucial step in understanding and strategizing for community health is visualizing the data. This allows for a quick and insightful overview of key factors like demographics, healthcare access, and the current reach of SSM Health. Effective visualizations can quickly identify areas where services might be lacking or where expansion efforts could yield the most significant impact.
The following sections detail a proposed visual representation designed to accomplish this.
Community Demographics Overview
This visualization will start with a map of the Greater Fond du Lac and Waupun areas. Each region will be color-coded based on key demographic characteristics, such as age distribution, income levels, and ethnicity. This map will use a gradient scale, where darker shades represent higher concentrations of specific demographics. For instance, a darker shade of purple might indicate a higher concentration of senior citizens in a specific neighborhood.
This allows for a rapid visual identification of population segments and potential health needs. The data will be sourced from the U.S. Census Bureau, county health departments, and local community surveys.
Healthcare Access and Utilization
A second visualization will display healthcare access data. This visualization will overlay the demographic map with information about healthcare provider density (clinics, hospitals, etc.), the proportion of individuals insured, and the distance to the nearest healthcare facility. The visualization will use a combination of graduated symbols (e.g., larger symbols representing higher provider density) and color-coded areas (e.g., lighter colors indicating better access).
This will provide a comprehensive picture of areas with limited healthcare access and inform strategies to improve outreach. The data will be gathered from healthcare provider directories, insurance company data, and publicly available health reports.
SSM Health’s Current Reach
A third visualization will map SSM Health’s existing services. This map will show the locations of SSM Health clinics, hospitals, and outreach programs in the region. Different colors or shapes will distinguish different types of services. The visualization will also incorporate the volume of patients served at each location. This will provide a clear understanding of existing coverage and potential gaps.
Data sources include SSM Health’s internal service directories and patient records.
Data Visualization Table
Data Point | Category | Visualization Type | Description |
---|---|---|---|
Age distribution | Demographics | Choropleth Map (color-coded regions) | Different shades of color will represent varying age ranges within each geographic area. |
Income levels | Demographics | Choropleth Map (color-coded regions) | Different shades of color will represent different income brackets within each geographic area. |
Ethnicity | Demographics | Choropleth Map (color-coded regions) | Different shades of color will represent different ethnicities within each geographic area. |
Healthcare provider density | Healthcare Access | Graduated Symbol Map (larger symbols for higher density) | Larger symbols will represent higher concentrations of clinics and hospitals within each area. |
Proportion of insured individuals | Healthcare Access | Choropleth Map (color-coded regions) | Different shades of color will represent the percentage of insured individuals within each area. |
Distance to nearest healthcare facility | Healthcare Access | Graduated Symbol Map (size of symbol correlates to distance) | Size of symbols will reflect the distance to the nearest healthcare facility. |
SSM Health clinic locations | SSM Health’s Reach | Point Map (different shapes for different types of services) | Different colored points on the map will show the location of SSM Health clinics and the types of services they offer. |
Patient volume at SSM Health locations | SSM Health’s Reach | Graduated Symbol Map (size of symbol correlates to patient volume) | Larger symbols will represent higher patient volume at each SSM Health location. |
Closure
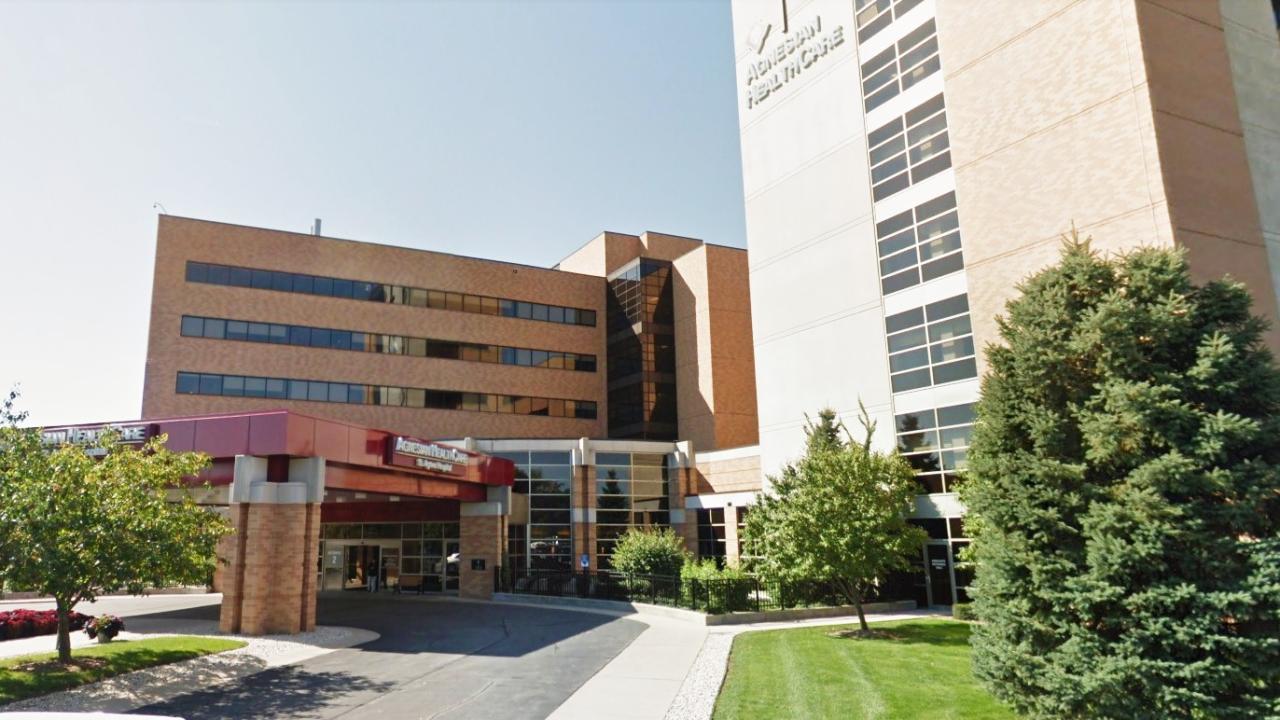
In conclusion, SSM Health’s expansion into Waupun, supported by the Fond du Lac presence, offers a significant opportunity to improve healthcare access and outcomes for the residents of both communities. The analysis highlights potential service expansions, collaborative partnerships, and community engagement strategies to build trust and address existing healthcare needs effectively. The success of this initiative hinges on continuous evaluation and adaptation, ensuring that strategies remain relevant and impactful.